Types of Sand Used in Sand Casting
Sand casting is one of the oldest and most versatile metal casting processes, widely used in various industries to produce complex metal parts. The success of sand casting largely depends on the type of sand used, as different sands have unique properties that affect the overall quality of the casting. This article explores the primary types of sand used in sand casting, their characteristics, benefits, and applications.
1. Silica Sand
Silica sand is the most commonly used type of sand in sand casting. It is made primarily of silicon dioxide (SiO₂) and is known for its excellent thermal properties, high melting point, and good flowability. Silica sand grains are angular and hard, which provides strength and durability when packed tightly in a mold.
One of the key advantages of silica sand is its availability; it can be sourced from many regions worldwide. Additionally, it is relatively inexpensive compared to other types of casting sands. However, silica sand has a downside it can create respiratory health issues when inhaled as fine dust. To mitigate this risk, modern sand casting facilities often implement effective ventilation systems to minimize dust exposure.
2. Chromite Sand
Chromite sand is used primarily in steel casting applications. It is derived from chromite ore and is known for its high melting point and excellent thermal conductivity. Chromite sand grains are dense and have a unique chemical composition that resists thermal degradation.
One significant advantage of chromite sand is its ability to withstand high temperatures without deforming, making it ideal for heavy metal casting applications. Furthermore, it provides excellent surface finish and dimensional accuracy in the resulting castings. However, chromite sand is more expensive than silica sand, which can limit its use to specific applications in the industry.
3. Zircon Sand
Zircon sand is another premium casting material that is prized for its excellent thermal and chemical stability. Composed of zirconium silicate (ZrSiO₄), it has an exceptionally high melting point and provides excellent resistance to thermal shock.
types of sand used in sand casting
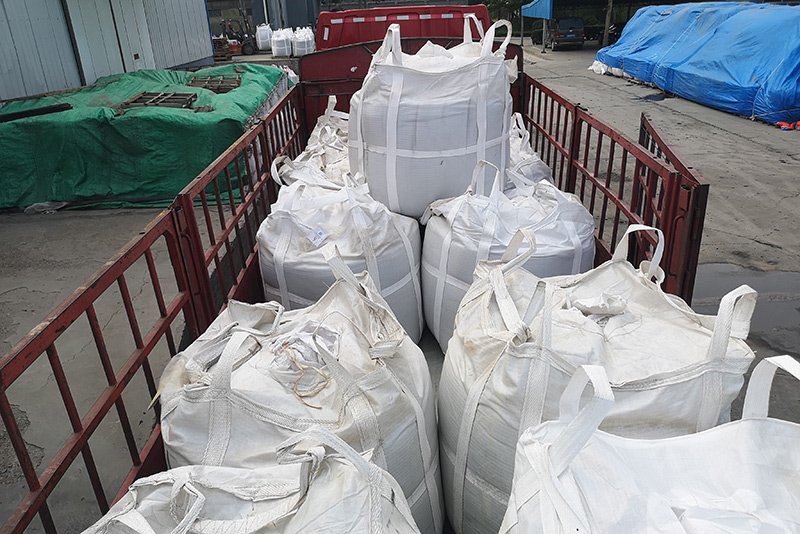
Zircon sand is particularly beneficial for applications that require intricate designs and high surface finishes. Its non-wetting nature means that it does not adhere to the molten metal, resulting in smoother surfaces and less defect formation. However, the high cost of zircon sand often restricts its use to high-end applications, such as aerospace and defense industries.
4. Olivine Sand
Olivine sand is a naturally occurring mineral sand made from magnesium iron silicate. It offers a unique combination of thermal stability, low expansion, and good bonding properties. Olivine sand is also environmentally friendly, as it does not produce harmful emissions during the casting process.
This type of sand is frequently used for making molds for ferrous and non-ferrous metal castings. Its exceptional ability to control mold temperature helps to reduce casting defects, making it a preferred choice in industries requiring high-quality castings. The primary drawback is that olivine sand is less readily available and can be more expensive than silica sand.
5. Green Sand
Green sand is a mixture of silica sand, clay, and water that is molded while damp. The water and clay help to bind the grains together, providing the necessary strength to hold the mold shape. Green sand is widely used in the foundry industry due to its cost-effectiveness and ease of molding.
One of the main advantages of green sand is its ability to be reused multiple times, making it a sustainable option for manufacturers. It allows for good detail reproduction, although it may require additional finishing processes to achieve the desired surface quality. Green sand’s adaptability has made it a staple in the production of cast iron and aluminum parts.
Conclusion
When it comes to sand casting, the choice of sand plays a pivotal role in determining the quality and characteristics of the final product. Whether it's the common silica sand or more specialized options like chromite, zircon, or olivine sand, each type brings its own set of advantages and limitations. As industries continue to evolve, the exploration and utilization of different sands will remain essential in meeting the increasingly stringent demands of manufacturing and engineering.
Post time:अक्ट . 12, 2024 10:52
Next:foundry sand in concrete