Types of Foundry Sand
Foundry sand plays a pivotal role in metal casting processes, serving as the primary material used to create molds and cores. The importance of selecting the appropriate type of sand cannot be overstated, as it directly affects the quality of the final cast product, the efficiency of the casting process, and the overall costs involved. This article delves into the various types of foundry sand, their characteristics, and their applications in metal casting.
1. Silica Sand
Silica sand is the most common type of foundry sand and is widely used in the metal casting industry. Composed primarily of silicon dioxide (SiO2), this sand is known for its excellent thermal stability, high melting point, and ability to retain shape when heated. Silica sand is typically characterized by its grain size and shape, which can vary depending on its source.
In casting applications, silica sand is often bonded with various materials to create molds and cores. There are two main types of silica sand green sand and core sand. Green sand consists of silica sand mixed with clay and water, making it pliable and ideal for creating complex mold shapes. Core sand, on the other hand, is a finer sand that is used to create internal cavities within castings. Both forms of silica sand are favored for their ability to produce high-quality surface finishes.
2
. Zircon SandZircon sand, composed of zirconium silicate (ZrSiO4), is another crucial type of foundry sand. This sand possesses unique properties such as high resistance to thermal shock, low thermal expansion, and excellent chemical stability. Zircon sand is often used in high-temperature applications and in the production of molds for non-ferrous metal castings.
Due to its cost, zircon sand is typically used in more specialized foundries where the demands on casting quality and performance are particularly high. It is worth noting that zircon sand provides a better surface finish compared to silica sand, making it favorable for intricate components that require precision.
3. Chromite Sand
Chromite sand, derived from chromite ore (FeCr2O4), is a heavy mineral sand used primarily for steel and iron casting. It boasts excellent thermal conductivity and high melting resistance, making it ideal for the production of molds. Chromite sand is less abrasive compared to silica, leading to longer mold life and reduced wear on casting equipment.
types of foundry sand
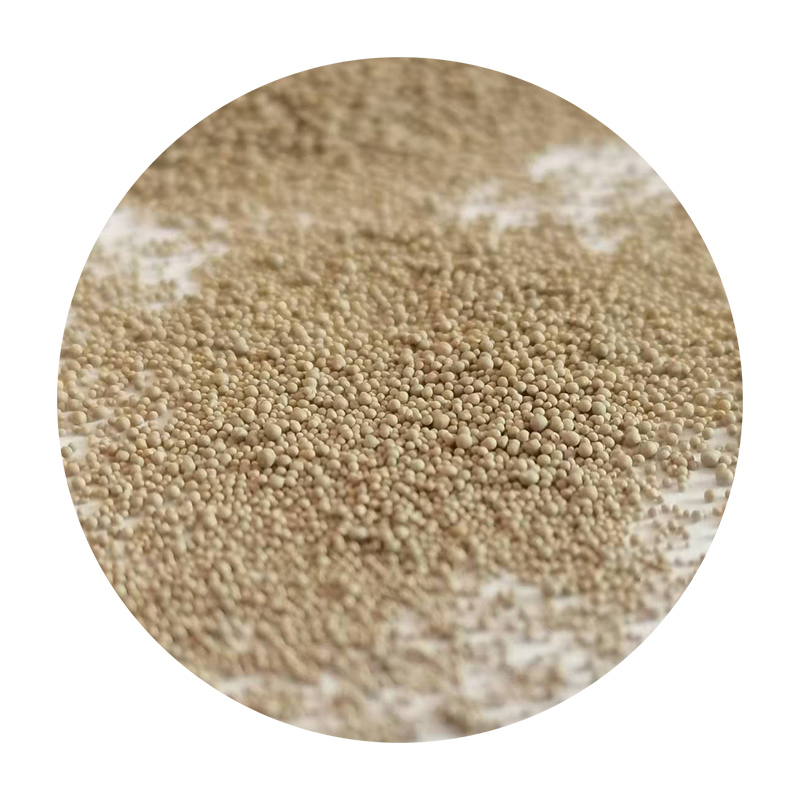
This type of sand is particularly popular in the production of heavy castings, such as those used in the automotive and aerospace industries. An added advantage of chromite sand is its ability to reduce the formation of defects in the foundry process, contributing to a higher quality finished product.
4. Olive Sand
Olive sand, a more specialized and less common type of foundry sand, is derived from the volcanic rocks found in certain regions. It is characterized by its dark color and relatively high density. Olive sand exhibits excellent resistance to high temperatures, making it suitable for particularly challenging casting applications.
Its unique properties allow olive sand to be used in the production of molds for critical components that demand optimal performance under extreme conditions. However, its availability and cost can limit its widespread use in the foundry industry.
5. Furan Sand
Furan sand is a type of chemically bonded sand that uses furan resin as a binder. This specialty sand is used in the production of molds that require high strength and accuracy. The process of casting with furan sand involves a curing reaction that takes place at room temperature, allowing for energy-efficient and rapid mold production.
Furan sand is particularly suited for high-volume production and for creating small, intricate components. While furan sand is more expensive than traditional green sand, its improved characteristics in terms of strength and surface finish justify the additional cost in many applications.
Conclusion
Selecting the appropriate type of foundry sand is essential for achieving optimal results in metal casting. Each type of sand, whether it be silica, zircon, chromite, olive, or furan, comes with its distinct set of properties that cater to different casting requirements. Understanding these properties allows foundry professionals to make informed decisions, ultimately leading to improved casting quality, enhanced efficiency, and reduced production costs. As the foundry industry continues to evolve, ongoing research and developments in sand technology will likely introduce new materials, further enhancing the capabilities of metal casting processes.
Post time:डिस . 05, 2024 11:06
Next:kan du sand 3d avtrykk