Types of Foundry Sand A Comprehensive Overview
Foundry sand is a critical component in the metal casting process, used to create molds that shape molten metal into desired forms. Understanding the different types of foundry sand is essential for foundry operations, as each type has unique properties that make it suitable for specific applications. This article explores the most common types of foundry sand and their characteristics.
1. Silica Sand
Silica sand is the most widely used foundry sand. Comprising primarily quartz grains, it is prized for its high melting point and excellent thermal stability. Silica sand can withstand high temperatures without breaking down, making it ideal for casting ferrous metals. Its availability and cost-effectiveness also contribute to its popularity. However, the fine grain size can lead to a higher rate of sand erosion, which might affect mold integrity over time.
2. Green Sand
Green sand is a mixture of silica sand, clay, and water. The term green refers to the fact that it is used in a moist state, rather than dried. The clay acts as a binder, giving the sand the necessary plasticity to form intricate shapes. Green sand molds are widely used for ferrous and non-ferrous metal casting due to their excellent ability to retain shape and strength. However, the moisture content must be carefully controlled to prevent issues with mold collapsing during casting.
3. Resin Sand
types of foundry sand
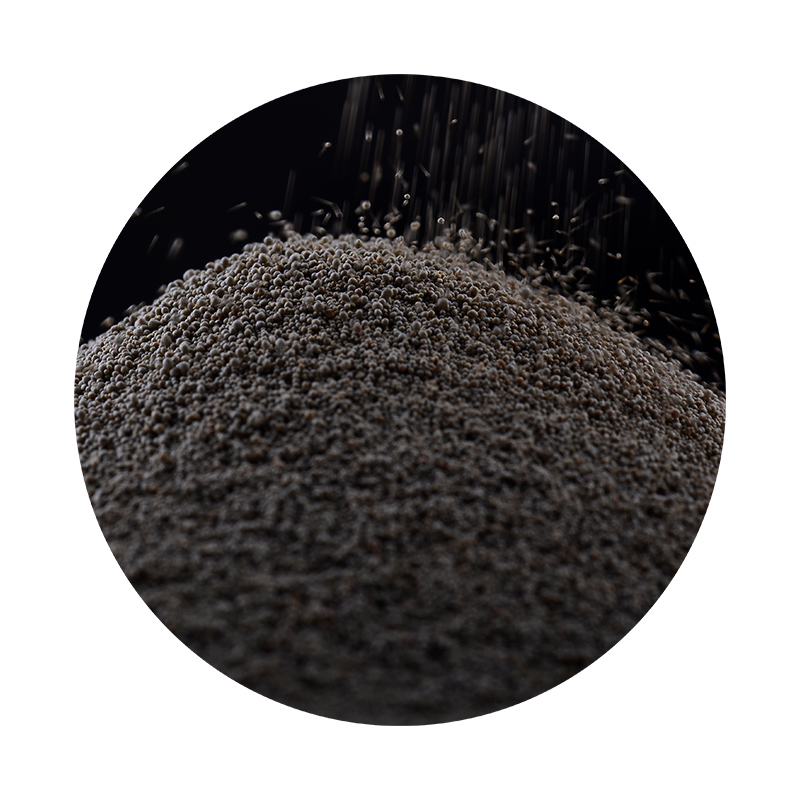
Resin sand uses a synthetic resin as a binder instead of clay. This type of sand is known for its excellent surface finish and dimensional accuracy, which reduces the need for extensive machining after casting. Additionally, resin sand can withstand higher temperatures compared to green sand, making it suitable for more complex metal castings. However, the production process for resin sand can be more costly, and it may require specialized handling to manage emissions during the curing process.
4. Shell Sand
Shell sand is created by coating fine sand grains with a thermosetting resin. The resins are cured to form a hard shell, offering enhanced durability and a finer surface finish. Shell sand is particularly useful for casting intricate designs, as it can capture fine details better than traditional sand. This type of sand is often used in applications where high precision is required, such as in aerospace or automotive parts. However, the cost of shell sand can be higher due to the additional processing involved.
5. Carbonaceous Sand
Carbonaceous sand contains carbon-based materials, which can improve the mold's strength and heat resistance. This type of sand is often used in applications involving heavy or high-stress castings. Carbonaceous sand can help reduce oxidation and improve the mechanical properties of the final product. However, it may not be as commonly used as silica or green sand, primarily due to its specialized applications.
Conclusion
Each type of foundry sand serves specific functions in metal casting, influencing the final product's quality and characteristics. Foundries must choose the appropriate sand type based on factors such as the type of metal being cast, desired finish quality, and production costs. By understanding the various types of foundry sand, foundries can optimize their casting processes and improve overall efficiency, leading to better-quality castings that meet the demands of diverse industries.
Post time:सेप . 07, 2024 21:45
Next:Sand Printing Casting