The Role of Sand in Ceramic Fire Bricks An Overview
Ceramic fire bricks, also known as refractory bricks, play a crucial role in various high-temperature applications, including fireplaces, kilns, and furnaces. These bricks are specifically designed to withstand extreme heat and thermal shock while providing structural integrity and durability. One of the essential components used in making ceramic fire bricks is sand, which significantly influences their properties and performance.
Composition and Properties
Ceramic fire bricks are primarily made from a mixture of clay, feldspar, and other refractory materials, with sand being a key ingredient. The inclusion of sand, particularly silica sand, enhances the overall strength and resistance of the bricks against thermal stresses. Silica, the primary component of sand, has a high melting point—over 1,700 degrees Celsius—which makes it ideal for high-temperature applications.
The presence of sand in the composition of ceramic fire bricks also contributes to their low thermal expansion coefficient. This means that these bricks can endure rapid temperature changes without cracking or breaking. This characteristic is essential in applications such as wood-fired ovens or industrial furnaces, where the temperature can fluctuate dramatically.
Manufacturing Process
The manufacturing of ceramic fire bricks typically involves mixing clay and sand with water to form a homogeneous paste. This mixture is then shaped into bricks using molds. After shaping, the bricks undergo a drying process to remove moisture before being fired in a kiln at high temperatures. During firing, the minerals in the clay and sand undergo various chemical reactions, which bind the materials together and enhance their refractory properties.
Different types of sand can be used in the production of ceramic fire bricks, including quartz sand and foundry sand, depending on the desired characteristics of the final product. Each type of sand can influence the brick's color, texture, and thermal properties, allowing manufacturers to customize bricks for specific applications.
sand ceramic fire brick
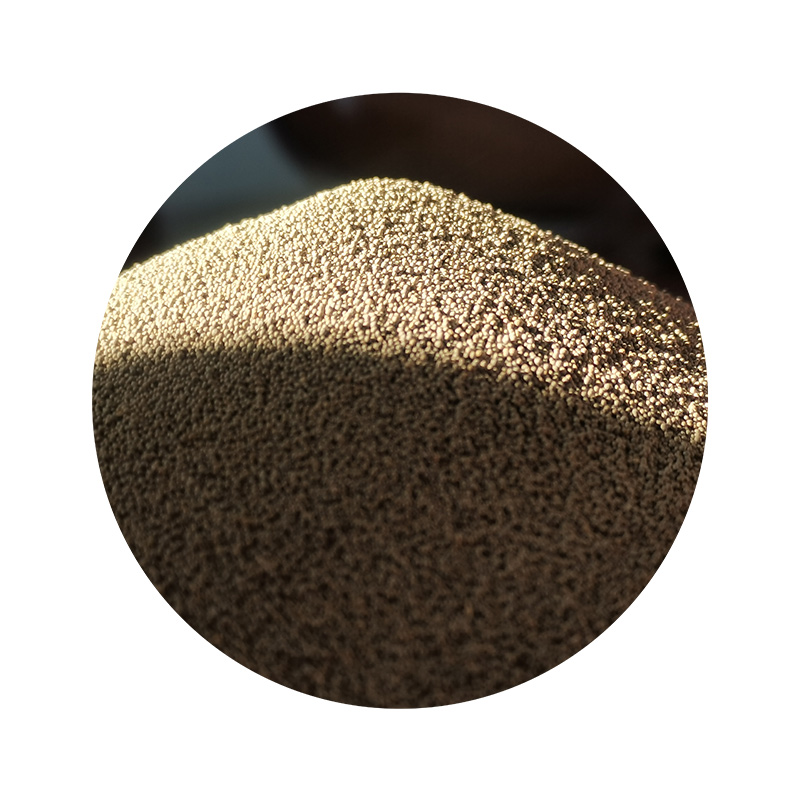
Applications
Ceramic fire bricks are widely used in various industries due to their excellent heat resistance and durability. In industrial settings, these bricks are essential for lining kilns and furnaces involved in metal smelting, glass production, and ceramics manufacturing. They provide thermal insulation and protect the structural integrity of the equipment by withstanding extreme temperatures.
In residential applications, ceramic fire bricks are popular for building fireplaces, stoves, and pizza ovens. Their ability to retain heat improves energy efficiency and provides a reliable source of warmth. Moreover, their aesthetic appeal, often available in various colors and textures, allows them to blend seamlessly with home decor.
Environmental Considerations
As with many manufactured products, the use of sand in ceramic fire bricks raises some environmental considerations. The extraction of sand from natural sources can lead to ecological imbalances, prompting manufacturers to explore sustainable alternatives. Recycling waste materials, such as industrial by-products, can also reduce the dependence on natural sand without compromising the quality of the fire bricks.
Conclusion
In summary, sand is a vital component in the manufacturing of ceramic fire bricks, contributing significantly to their strength, thermal resistance, and overall performance. With their wide range of applications in both industrial and residential settings, ceramic fire bricks continue to be an indispensable material in high-temperature environments. As sustainability becomes increasingly important, the ceramic industry must innovate to balance performance with environmental responsibility. The future of ceramic fire bricks will likely involve advancements in both technology and materials, ensuring that they remain a valuable resource for generations to come.
Post time:अक्ट . 21, 2024 13:25
Next:can you sand 3d prints