The Significance of Sand Cast Iron in Modern Manufacturing
Sand cast iron has been a pivotal material in the realm of manufacturing for centuries. The process of sand casting involves pouring molten metal into a mold made of sand, which once solidified, takes on the shape of the desired object. Sand cast iron, in particular, presents a unique combination of properties that make it exceptionally suitable for various applications, from automotive components to intricate industrial machinery.
One of the primary advantages of sand cast iron is its excellent fluidity when molten. This characteristic allows it to fill intricate mold designs, capturing even the finest details, which is crucial for manufacturing complex parts. The versatility of sand casting means that it can be utilized to produce parts of varying sizes, from small components to large structural elements.
Moreover, sand cast iron exhibits remarkable strength and durability. This material is renowned for its high wear resistance, which makes it an ideal choice for parts subject to significant stress and friction. For instance, in the automotive industry, sand cast iron is frequently used for manufacturing engine blocks, cylinder heads, and crankcases. These applications leverage the material's ability to withstand high temperatures and extensive mechanical stress while maintaining structural integrity.
In addition to its mechanical properties, sand cast iron also offers advantages in terms of thermal conductivity. This property is beneficial in applications where heat dissipation is crucial, such as in brake rotors and engine components. The ability of sand cast iron to absorb and dissipate heat minimizes the risk of thermal fatigue, thus prolonging the lifespan of critical automotive parts.
Furthermore, the environmental impact of sand casting processes has garnered attention in recent years as sustainability becomes a priority in manufacturing. The sand used in the casting process is often reusable, reducing waste and the need for new materials. Additionally, advancements in recycling technologies now allow for the reuse of scrap cast iron, further minimizing the environmental footprint of sand cast iron production.
sand cast iron
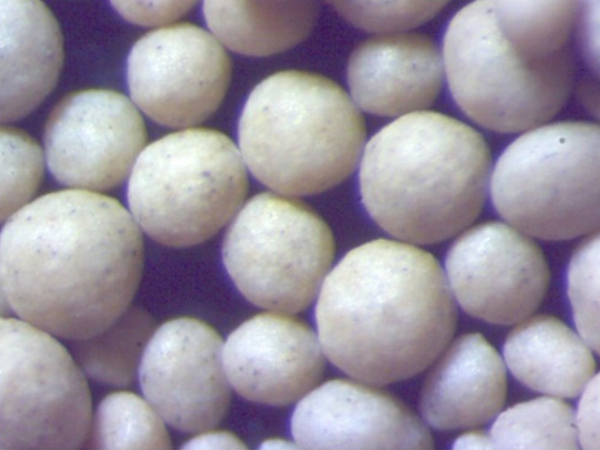
However, the sand casting process is not without its challenges. The quality of the final product can be influenced by various factors, including sand composition, mold design, and melting temperature. Achieving precision in sand casting can be more challenging compared to other manufacturing processes like die-casting or machining. As a result, manufacturers must invest in adequate quality control measures to ensure that the end products meet industry standards.
Despite these challenges, the advantages of sand cast iron continue to shape the landscape of modern manufacturing. Its cost-effectiveness relative to other materials, coupled with the ability to produce complex shapes and parts, makes sand cast iron an attractive choice for many industries. The material’s robust performance and adaptability will likely ensure its relevance for years to come, paving the way for innovations that can enhance its properties or broaden its applications.
In recent years, the exploration of alloying elements and new processing techniques has led to the development of specialized forms of sand cast iron, such as ductile iron and gray iron. These variants possess specific characteristics that can be tuned to meet the requirements of particular applications. For instance, ductile iron is known for its enhanced ductility and toughness, making it suitable for components subjected to dynamic loads, while gray iron offers superior machinability.
The future of sand cast iron in manufacturing looks promising, with ongoing research aimed at improving its properties and processing techniques. The integration of advanced technologies, such as 3D printing and computer simulations, is revolutionizing the sand casting process. These innovations allow manufacturers to design more complex and efficient molds, reducing material waste and production time, while also enhancing product quality.
In summary, sand cast iron remains a cornerstone of modern manufacturing, bridging traditional processes with contemporary technological advancements. Its unique properties, adaptability, and potential for sustainable practices will undoubtedly continue to drive its use across various industries. As manufacturers strive for efficiency and quality in an increasingly competitive market, the significance of sand cast iron is likely to endure, evolving alongside the demands of innovation in manufacturing.
Post time:नोभ . 10, 2024 16:45
Next:A Complete Guide to Sanding Epoxy Resin for a Smooth Finish