Sand Casting Procedure An Overview
Sand casting is one of the oldest and most widely used metal casting processes, allowing for the creation of complex shapes and large components at relatively low costs. This procedure has endured through the years due to its simplicity and versatility. This article will provide an overview of the key steps involved in the sand casting process.
Step 1 Pattern Making
The first step in sand casting is the creation of a pattern, which is a replica of the final product that will be cast. Patterns are typically made from materials such as wood, metal, or plastic and can be crafted in a single piece or in sections that will be assembled during production. The design of the pattern needs to account for shrinkage, which occurs as the metal cools and solidifies. A well-made pattern ensures accuracy in the final product and can significantly influence the quality of the casting.
Step 2 Mold Preparation
Once the pattern is complete, the next step is to create the mold. The mold is formed using a mixture of sand, clay, and water, known as molding sand. This mixture is compacted around the pattern, and when the pattern is removed, it leaves a cavity in the shape of the part to be cast. The mold is typically made in two halves, known as the cope and drag, which are then fitted together for the pouring phase. Accurate mold preparation is crucial because it determines the surface finish and dimensional accuracy of the casting.
Step 3 Pouring
With the mold ready, the next step is pouring the molten metal into the mold cavity. The metal is usually heated in a furnace until it reaches a liquid state. The choice of metal can vary but often includes aluminum, iron, or bronze, depending on the desired properties of the final product. Pouring is a critical phase; it must be done carefully to minimize defects such as air pockets or inclusions. Proper pouring techniques and controlling the flow of metal are essential to ensure a smooth filling of the mold.
sand casting procedure
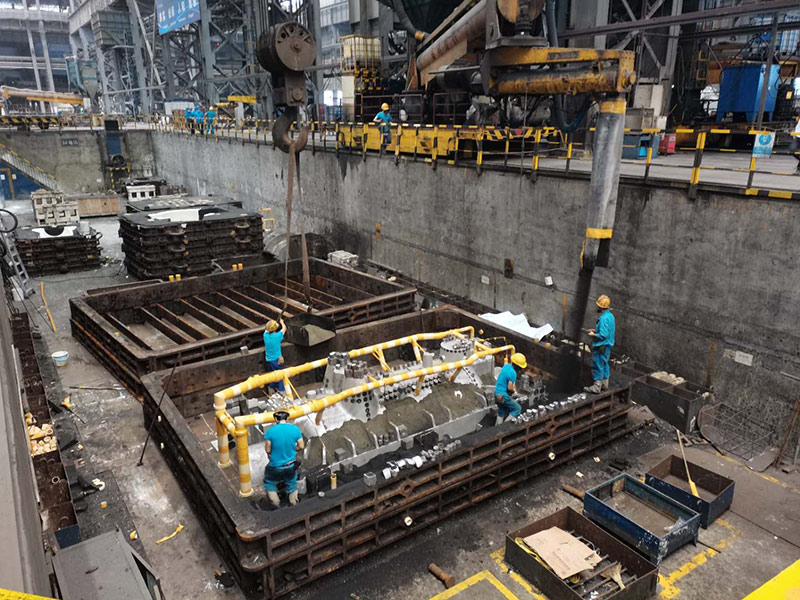
Step 4 Cooling
After the mold has been filled, the metal must cool and solidify within the mold. The cooling time depends on several factors, including the type of metal used, the thickness of the casting, and the surrounding environment. During this phase, the metal transitions from its liquid state to solid, and it is crucial to monitor the process to prevent issues such as cracking or warping.
Step 5 Mold Removal
Once the metal has sufficiently cooled, the mold is broken apart to retrieve the casting. This step requires care to avoid damaging the newly formed part. The casting is then cleaned to remove any sand or residual particles, often through processes such as sandblasting or shot peening.
Step 6 Finishing
Finally, the casting may require finishing processes to achieve the desired surface quality and dimensional tolerances. This can include machining, grinding, or polishing, depending on the specific requirements of the project. Finishing enhances the aesthetic quality of the final product and improves its functionality.
Conclusion
Sand casting is a fundamental process in manufacturing that offers a balance of cost-effectiveness and the ability to create intricate designs. By following these essential steps—pattern making, mold preparation, pouring, cooling, mold removal, and finishing—manufacturers can produce high-quality castings that meet diverse industrial needs. Its enduring relevance in the metalworking industry underscores the importance of mastering the sand casting procedure for both new and experienced foundry professionals.
Post time:अक्ट . 12, 2024 06:59
Next:Create a 3D Printable Sanding Block for Your DIY Projects