Sand Casting A Time-Honored Metal Casting Technique
Sand casting, also known as sand mold casting, is one of the most ancient and versatile metal casting processes still in use today. It dates back over 5,000 years, with evidence suggesting that it was used in ancient Egypt and China. While the basic principles of sand casting have remained largely unchanged, advancements in technology and materials have improved the precision and efficiency of the process, making it a popular choice for many industries.
At its core, sand casting involves creating a mold from sand, into which molten metal is poured. The process is relatively simple and can be broken down into several key steps pattern making, mold preparation, pouring, and finishing.
Pattern Making
The first step in the sand casting process is the creation of a pattern, which serves as a replica of the final product. Patterns are typically made of materials such as wood, metal, or plastic and are designed with slightly larger dimensions to accommodate for metal shrinkage during cooling. The pattern is crucial because it impacts the accuracy and quality of the final casting. Various pattern types exist, including solid patterns, split patterns, and core patterns, depending on the complexity and requirements of the casting.
Mold Preparation
Once the pattern is ready, the next phase is mold preparation. This involves packing sand around the pattern to form a mold. The sand used in casting is often mixed with clay and water to enhance its binding properties, creating a mold that can withstand the heat of molten metal. After packing, the mold halves are separated, and the pattern is removed, leaving an impression or cavity in the sand that mirrors the shape of the desired part.
In cases where internal features are required, workers use sand cores, which are created separately and placed into the mold. These cores are crucial for forming hollow structures within the casting.
Pouring
sand casting metal
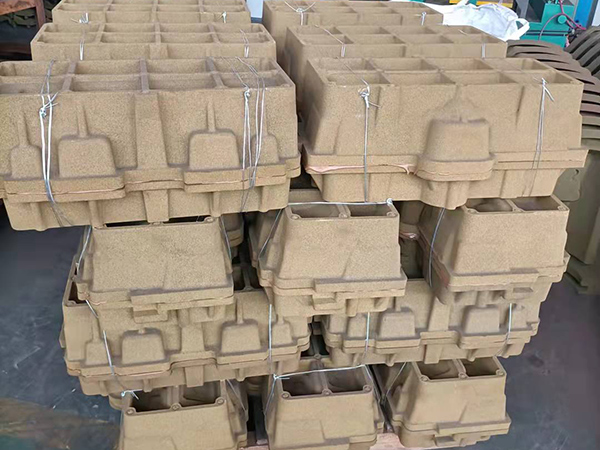
The next step is pouring the molten metal into the mold. The metal is heated in a furnace until it reaches a liquid state, and then it is carefully poured into the mold cavity. Control of pouring temperature and speed is critical; too rapid a pour can lead to defects, while pouring at incorrect temperatures can affect the mechanical properties of the final product. Once the molten metal fills the mold, it is allowed to cool and solidify, which can take several hours depending on the size and thickness of the casting.
Finishing
After the metal has cooled, the final step is finishing the cast product. The mold is broken away, usually by hand or with vibration systems, to reveal the casting. The casting may have rough edges and a sandy surface that require machining, grinding, or polishing to achieve the desired finish and tolerances. This finishing process is essential for ensuring that the casting meets the specifications required for its intended application.
Applications of Sand Casting
Sand casting is widely used for producing a variety of metal components across multiple industries. It is especially prevalent in sectors such as automotive, aerospace, and heavy machinery, where complex shapes and robust parts are needed. The ability to cast both ferrous and non-ferrous metals, such as iron, steel, aluminum, and bronze, further enhances its versatility.
One of the significant advantages of sand casting is its cost-effectiveness, particularly for low to medium production runs. The process allows for quick turnaround times and the ability to produce large components without the need for expensive tooling, which can be a barrier in other casting methods.
Conclusion
In summary, sand casting is a time-honored manufacturing technique that combines simplicity and effectiveness to produce high-quality metal parts. Despite the rise of more modern casting methods, sand casting remains a staple in metalworking due to its versatility, cost-effectiveness, and capacity to create intricate designs. As industries continue to evolve, sand casting will undoubtedly adapt, maintaining its relevance in the ever-changing landscape of manufacturing technology.
Post time:नोभ . 19, 2024 10:13
Next:Pros and Cons of the Sand Casting Process Explained in Detail