Sand Casting Iron An Overview of the Process and Its Applications
Sand casting, one of the oldest known metalworking techniques, is still widely used today, particularly in the production of cast iron parts. This method involves creating a mold from a mixture of sand, clay, and water, into which molten metal is poured to produce a solid object. The versatility and cost-effectiveness of sand casting make it a popular choice in various industries.
The Sand Casting Process
The sand casting process begins with the preparation of the mold. Fine silica sand is mixed with a binding agent, typically clay, which helps the mold hold its shape during the pouring of the molten iron. Water is added to the mixture to facilitate binding and make it pliable. The sand is then packed tightly into a two-part mold, comprised of the cope (top half) and the drag (bottom half), which can be separated to remove the finished cast.
Once the mold is prepared, it is crucial to create a cavity that mirrors the final shape of the desired cast iron object. This is done using a pattern, often made from wood, plastic, or metal, which is shaped to match the design specifications. After the pattern is placed in the sand and removed, it leaves behind an imprint that serves as the mold cavity.
Next, the molten iron, typically heated to temperatures exceeding 1,500 degrees Celsius (2,732 degrees Fahrenheit), is poured into the mold. The choice of cast iron is vital, known for its high fluidity, excellent casting properties, and good durability. Various alloys of cast iron can be used depending on the required mechanical properties of the finished product, such as gray iron, ductile iron, or white iron.
After the molten iron fills the mold and starts to cool, the next step involves waiting for the metal to solidify. This cooling process can take anywhere from minutes to hours, based on the size and thickness of the casting. Once the iron has cooled sufficiently, the sand mold is broken away to reveal the cast iron object.
Advantages of Sand Casting
sand casting iron
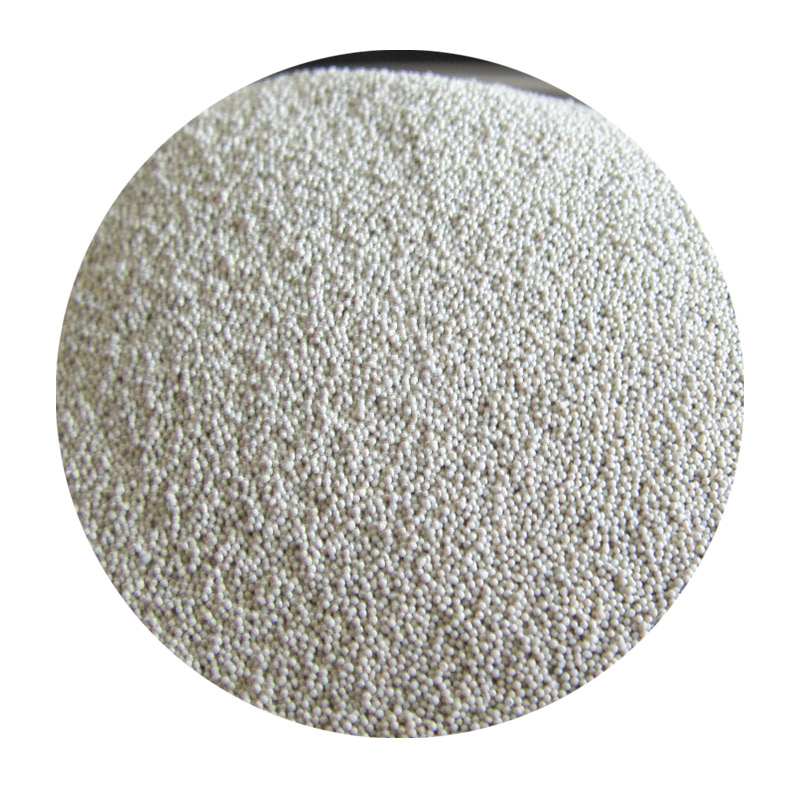
Sand casting offers several advantages that have contributed to its longevity in metalworking. First and foremost, the process is highly adaptable to a broad range of designs and sizes. From small components to large castings weighing several tons, sand casting can accommodate various dimensions and complex shapes that other casting processes might struggle with.
Another significant advantage is cost-effectiveness. The materials used in sand casting are comparatively inexpensive, and the process does not require complex machinery or setups, making it an attractive option for small-scale operations and prototypes. Furthermore, sand molds can often be reused, reducing waste and production costs.
However, one must be aware of the limitations of sand casting. The surface finish of cast products tends to be rougher than those produced through other methods such as investment casting. Additionally, the dimensional accuracy can vary, requiring further machining in some cases. Nevertheless, for many applications, the benefits outweigh these drawbacks.
Applications of Sand Casting Iron
Sand casting of iron is utilized in numerous industries, from automotive to construction. Components like engine blocks, valve bodies, and machine bases are commonly produced using this method, while decorative items and art sculptures also find their place in sand casting. The ability to produce complex shapes and features makes sand casting particularly suitable for manufacturing parts that require intricate designs.
In the future, advancements in technology, including computer simulations and automated sand molding machines, are likely to enhance the efficiency and accuracy of sand casting. As industries continue to explore sustainable practices, the inherent recyclability of sand and metal will contribute to the appeal of this age-old technique.
Conclusion
In summary, sand casting iron remains an essential process in modern manufacturing, combining practicality with versatility, cost-effectiveness, and adaptability. Its ability to produce complex shapes with relative ease ensures its relevance across various sectors. As industries evolve, sand casting will continue to play a crucial role in shaping the future of metalworking.
Post time:नोभ . 04, 2024 11:56
Next:sanding block 3d print