Conclusion on Sand Casting
Sand casting, one of the oldest and most versatile manufacturing processes, holds significant importance in various industries. This technique has been used for centuries to produce intricate metal components. This conclusion aims to summarize key aspects of sand casting, discussing its advantages, limitations, and future potential.
Firstly, the primary advantage of sand casting lies in its flexibility. The process allows for the creation of complex shapes and large components, with sand molds accommodating a wide variety of designs. This characteristic is particularly valuable in industries such as automotive, aerospace, and art foundry, where unique and detailed parts are often required. The ability to produce components in various sizes, ranging from small intricate designs to massive engine blocks, highlights the process's versatility.
Conclusion on Sand Casting
However, while sand casting offers numerous advantages, it is not without its limitations. One of the primary challenges is the surface finish of the cast components. Typically, sand-cast products have a rough surface compared to those produced using more refined methods, like die casting. Consequently, additional processes, such as machining or polishing, may be necessary to achieve the desired finish, which can increase the overall production time and cost.
sand casting conclusion
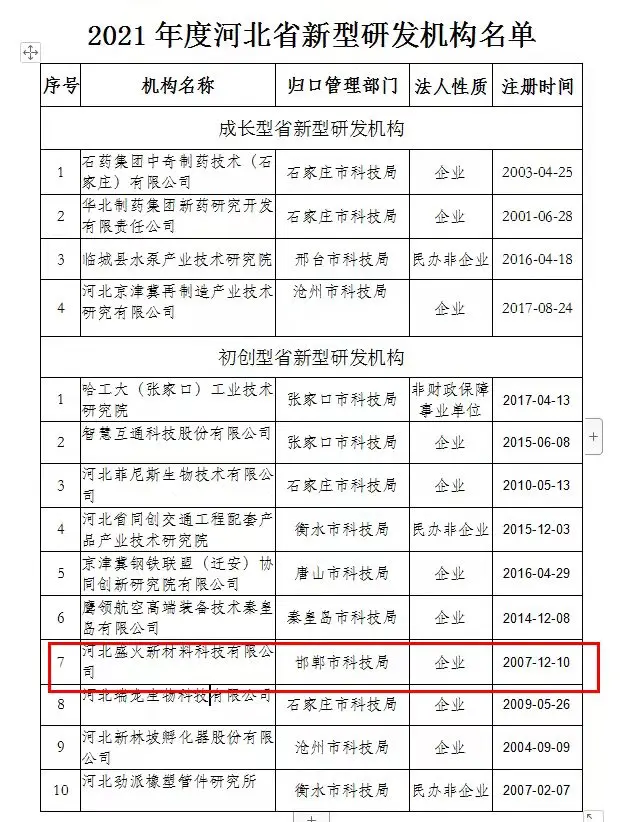
Another limitation is related to the dimensional accuracy of castings. Due to the nature of the sand mold, there can be variations in dimensions, which might not be acceptable for highly precise applications. This can lead to additional processes for quality control and adjustments, further complicating the workflow and potentially impacting delivery times.
Despite these challenges, the future of sand casting looks promising. With advancements in technology, innovations such as 3D printing are reshaping the landscape of mold creation. This integration of modern techniques allows for quicker production of molds and greater design flexibility, potentially overcoming some of the traditional limitations of sand casting. Furthermore, the development of new types of sand and binders, including environmentally friendly materials, is making the process more sustainable and appealing to eco-conscious manufacturers.
The growing demand for customized and complex parts in industries such as renewable energy and electric vehicles signifies a shift towards embracing sand casting as a viable solution. As manufacturers continue to seek efficient and cost-effective methods to produce high-quality components, sand casting stands poised to evolve and remain relevant.
In conclusion, sand casting is a time-tested process that offers a wealth of benefits including versatility, cost-effectiveness, and accessibility for diverse production scales. While it faces certain limitations in surface quality and dimensional accuracy, continuous advancements in technology and materials promise to enhance its capabilities. As we move into a future that emphasizes sustainability and customization, sand casting will undoubtedly remain a vital component of the manufacturing landscape, catering to the needs of various industries while innovating to meet new challenges. The synergy of traditional techniques with modern technologies ensures that sand casting will continue to be a foundational method in producing high-quality metal components for years to come.
Post time:डिस . 03, 2024 18:42
Next:sintering sand