The Economics of Sand Casting Understanding Pricing Factors
Sand casting, a versatile and age-old manufacturing process, plays a pivotal role in various industries, including automotive, aerospace, and heavy machinery. Understanding the price of sand casting involves a deep dive into its many components, from materials and labor to equipment and overhead costs. In this article, we will explore the factors that influence the market price of sand casting and how businesses can navigate this landscape.
1. Material Costs
The primary component of sand casting is, unsurprisingly, sand. However, the type and quality of sand used can significantly impact prices. High-quality silica sand is often preferred for its excellent thermal properties. In addition to sand, other materials such as resin binders and metal alloys can contribute to the overall cost. The fluctuation of material prices based on supply and demand dynamics in the global market can lead to variations in sand casting prices.
2. Labor Expenses
Labor costs are another crucial factor. The skill level of the workforce and the complexity of the casting design can affect labor expenses. Specialized workers, such as mold makers and quality control inspectors, demand higher wages due to their technical expertise. Moreover, the location of the foundry can influence labor costs; for instance, facilities in regions with a higher cost of living generally incur more substantial wage expenses.
sand casting price
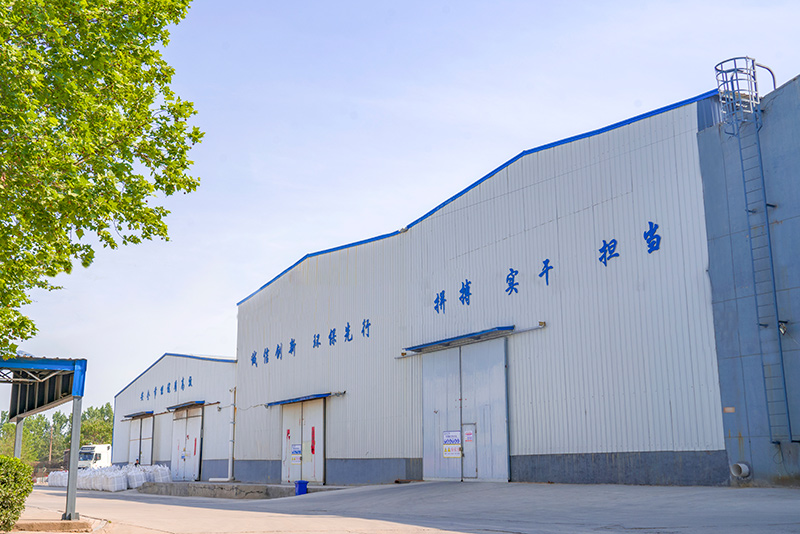
The initial investment in equipment and machinery is a significant element in calculating the price of sand casting. Foundries require various machines, including molding machines, furnaces, and finishing equipment, to produce high-quality castings. Each piece of equipment has associated maintenance costs, which can impact the final price of the casting. Moreover, technological advancements necessitate continuous investment to stay competitive, adding another layer to equipment costs.
4. Overhead and Operating Costs
Overhead costs, such as utilities, insurance, and facility maintenance, must also be factored into the price of sand casting. High energy costs, particularly for melting metals and running machinery, can lead to increased production expenses. Additionally, regulatory compliance regarding environmental concerns and worker safety may incur further costs that influence pricing strategies.
5. Market Demand and Supply
Finally, market demand significantly affects sand casting prices. When demand for cast parts rises, manufacturers may increase prices due to the higher cost of production and limited supply capabilities. Conversely, during economic downturns, surplus capacity and decreased orders can lead to price reductions as foundries compete for business.
Conclusion
Understanding the pricing of sand casting is essential for both manufacturers and consumers. By being aware of the various influencing factors, businesses can make informed decisions regarding their production processes and pricing strategies. As technology continues to evolve and global market dynamics fluctuate, staying abreast of these trends will be key to maintaining competitiveness in the sand casting industry. In an ever-changing economic landscape, the ability to adapt and optimize costs will determine the success of manufacturers engaged in this traditional yet critical manufacturing process.
Post time:सेप . 06, 2024 08:01
Next:The Golden Sands - Your Ultimate Beach Retreat