Understanding Resin Coated Sand An Essential Material in Modern Foundry Processes
In the world of foundry operations, the quest for improved efficiency, enhanced surface finish, and superior casting quality has led to the development and adoption of advanced materials. Among these, resin coated sand (RCS) has emerged as a significant innovation. This specialized material plays a crucial role in the sand casting process, which is one of the oldest and most widely used manufacturing methods for producing metal components.
What is Resin Coated Sand?
Resin coated sand consists of fine sand particles that are coated with a thermosetting resin. The primary purpose of this coating is to enhance the sand's bonding characteristics, creating a more durable mold or core during the casting process. Unlike traditional sand, which relies solely on moisture for adhesion, resin coated sand achieves structural integrity through the chemical properties of the resin when heated. This unique feature allows for the production of complex and precise shapes that are often difficult to achieve with conventional sand methods.
The Composition and Types of Resin Coated Sand
Typically, the base material of resin coated sand includes silica or other types of sand, which is then coated with a resin mixture, often made from furfuryl alcohol, epoxy, or phenolic resins
. The coating process usually involves mixing the sand with the resin and curing agents, followed by heating to solidify the resin onto the sand particles. This process can be tailored to meet specific application requirements, producing variations of RCS that offer distinct properties such as increased thermal resistance, improved strength, and enhanced surface finish.Advantages of Using Resin Coated Sand
1. Enhanced Strength and Durability The resin coating significantly increases the strength of the sand molds, allowing them to withstand higher pressures during the casting process. This property leads to fewer defects and improved dimensional accuracy in cast components.
resin coated sand
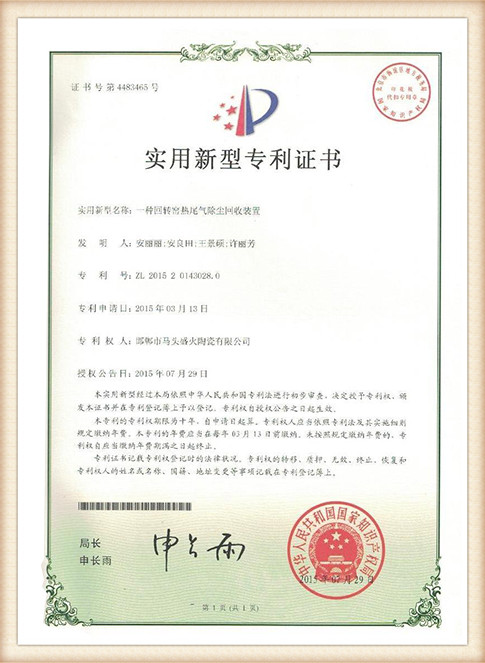
2. Improved Surface Finish Because of its excellent flowability and fine particle size, resin coated sand can produce molds with superior surface finishes, reducing the need for post-casting machining. This advantage is particularly important for high-quality applications, such as automotive and aerospace industries.
3. Reduced Casting Defects The use of RCS helps minimize defects such as sand inclusion and surface roughness, which are common issues with traditional sand casting. The controlled environment in which the resin binds to the sand helps create a more uniform and stable mold.
4. Versatility Resin coated sand is suitable for a wide range of metals, including aluminum, iron, and steel, making it a versatile choice for various casting applications. Its adaptability allows foundries to use the same material for different projects, simplifying inventory management.
Applications of Resin Coated Sand
The applications of resin coated sand span several industries. Predominantly, it is used in the production of intricate and high-precision components for automotive parts, machinery, and heavy equipment. As the demand for lightweight, high-strength materials grows, RCS is increasingly favored for its ability to produce complex geometries that meet stringent industry standards.
Conclusion
Resin coated sand has revolutionized the foundry industry by combining traditional casting techniques with modern material science. Its unique properties offer numerous advantages over conventional sand, making it an essential component in the production of high-quality metal castings. As industries continue to innovate and demand more advanced manufacturing solutions, the use of resin coated sand is poised to grow, further solidifying its position in the modern foundry landscape. Whether for automotive applications or intricate industrial components, RCS is undoubtedly a game-changer in achieving enhanced casting performance and efficiency.
Post time:डिस . 15, 2024 20:45
Next:Illustrative Cases of Products Created Through Sand Casting Techniques