The Importance of Resin Coated Sand in Modern Foundry Practices
Resin coated sand has emerged as a pivotal material in the foundry industry, significantly enhancing the quality of castings and the efficiency of the molding process. Acting as a versatile medium, this specialized sand is designed to meet the increasing demands of modern manufacturing, facilitating better performance and superior outcomes in metal casting applications.
At its core, resin coated sand is conventional silica sand that has been treated with a thermosetting resin. This innovative process binds the sand particles together, creating a more durable molding material capable of withstanding the intense heat generated during the metal casting process. Unlike traditional molding sands, resin coated sands exhibit excellent strength characteristics, allowing for intricate mold designs with sharp details and clean surface finishes.
One of the primary advantages of using resin coated sand is its superior dimensional accuracy. In industries where precision is critical, such as automotive and aerospace manufacturing, the ability to produce complex geometries without sacrificing quality has made resin coated sand an indispensable choice. The material's robust nature helps to maintain mold shape under heavy metal loads and thermal stresses, significantly reducing the occurrence of defects like warping or dimensional inconsistencies.
Moreover, resin coated sand also features improved flowability, which enhances the compaction of the sand in the molding process
. This characteristic allows for better filling of mold cavities and results in reduced porosity in the final casting. The reduced porosity is particularly beneficial because it leads to a stronger final product, minimizing the risk of failure in critical applications where structural integrity is paramount.resin coated sand
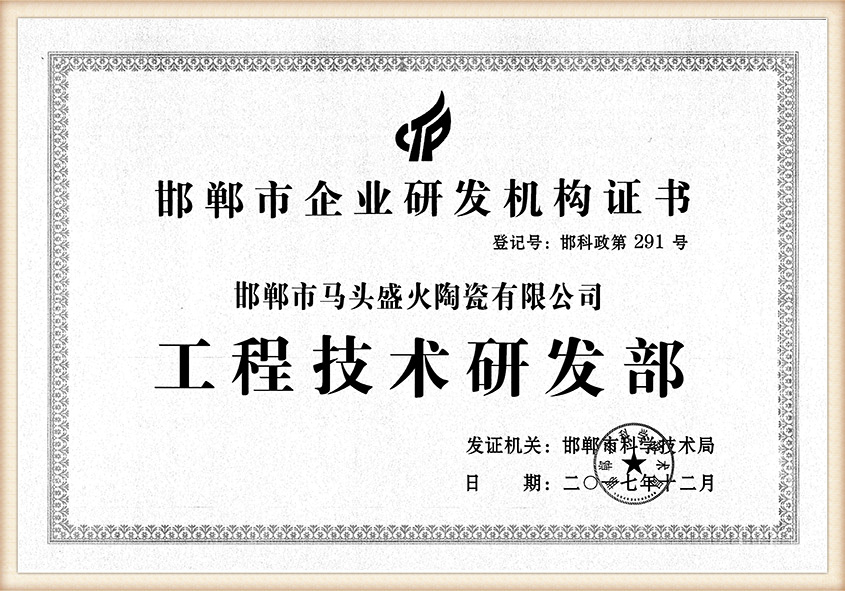
Environmental considerations are increasingly influencing material choices in the foundry sector. Resin coated sand systems offer a more environmentally friendly alternative compared to traditional sand casting techniques. Many modern resins are formulated to be low in volatile organic compounds (VOCs), thereby minimizing emissions during the curing process. Additionally, advancements in reclamation technologies enable the effective recycling of spent sand, reducing waste and lowering material costs for foundries.
The versatility of resin coated sand extends beyond merely improving mechanical properties; it also accommodates a variety of resins and additives tailored for specific applications. Foundries can customize formulations based on the type of metal being cast, the complexity of the mold, and the desired surface finish. This adaptability ensures that manufacturers can achieve optimal results across diverse casting environments.
Despite the advantages, transitioning to resin coated sand presents challenges. The initial cost of the raw materials can be higher than that of traditional sands, prompting some foundries to hesitate in making the switch. However, the long-term benefits, such as reduced rework, enhanced product quality, and increased throughput, often justify the initial investment.
To sum up, resin coated sand plays a crucial role in the evolution of foundry practices, delivering unmatched quality and efficiency in metal casting. As the industry continues to adapt to new technologies and environmental standards, the use of this advanced material is likely to become even more prevalent. Foundries that harness the benefits of resin coated sand will not only improve their operational efficiency but also contribute to a more sustainable manufacturing future.
Post time:सेप . 02, 2024 08:05
Next:Sanding Ceramic Mug - Personalized & Durable Designs