Lost Foam Casting Materials An Overview
Lost foam casting is an innovative and efficient manufacturing method used for producing complex and high-precision metal parts. It combines the principles of traditional casting with modern techniques to create intricate shapes without requiring elaborate tooling. One of the critical components that contribute to the success of lost foam casting is the selection of suitable materials. This article explores the materials used in lost foam casting, their properties, advantages, and applications.
What is Lost Foam Casting?
Lost foam casting (LFC) is a process where a foam pattern (usually made from expanded polystyrene) is used to create a mold into which molten metal is poured. The foam pattern is coated with a refractory material to form a shell. When the molten metal is poured into the mold, the foam evaporates in a process similar to lost-wax casting, leaving a void that takes the shape of the original pattern. This technique allows for high accuracy and a smooth finish, reducing the need for extensive machining post-casting.
Types of Foam Materials
The primary material used for the pattern in lost foam casting is expanded polystyrene (EPS). EPS is favored because of its lightweight properties and ease of fabrication. It can be molded into complex shapes with high precision, making it an ideal candidate for lost foam casting. Additionally, EPS is cost-effective and widely available, which further enhances the feasibility of this casting method for various applications.
Other types of foam materials, such as polyurethane and polyvinyl chloride (PVC), can also be used, depending on the specific requirements of the casting process. For instance, polyurethane foams can offer better dimensional stability and durability, although they may be more expensive than EPS.
Coating Materials
The foam pattern needs to be coated with a refractory material to withstand the high temperatures of molten metal. Common coating materials include - Ceramic Refractories These are high-temperature materials that can endure the molten metal's heat. They are often applied in multiple layers to achieve the desired thickness and strength. - Investment Casting Materials Some manufacturers use materials similar to those found in investment casting, which can provide a smooth surface finish and superior dimensional accuracy.
lost foam casting materials
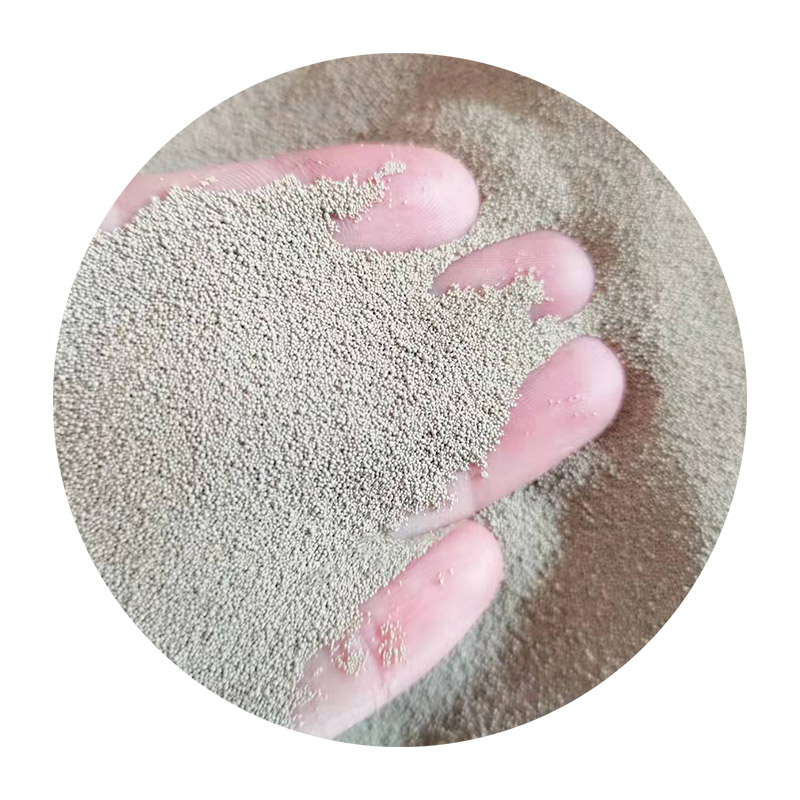
The choice of coating material depends on the alloy being cast and the expected thermal cycles during casting. Proper coating ensures that the foam does not burn too quickly and provides sufficient support for the molten metal.
Advantages of Lost Foam Casting Materials
The materials used in lost foam casting confer several benefits
- Precision and Complexity The foam pattern can be created with almost any geometric shape, enabling the production of highly detailed components. This precision is difficult to achieve with traditional sand casting. - Reduced Waste Unlike some conventional methods, lost foam casting generates minimal waste since the foam is completely vaporized and forms the cavity for the metal. This makes it an environmentally friendly option for manufacturers. - Cost Efficiency The overall costs associated with tooling and machining can be significantly reduced, making lost foam casting an economically attractive alternative for small to medium-sized production runs. - Versatility This casting method is suitable for a wide range of metals, including aluminum, iron, and various alloys, making it adaptable to many industries, from automotive to aerospace.
Applications
Lost foam casting is prevalent in sectors where precision and quality are paramount. It finds applications in
- Automotive Industry Production of engine blocks, cylinder heads, and other critical components. - Aerospace Manufacturing lightweight yet strong components for aircraft. - Industrial Machinery Creating intricate parts that require high strength and precision, such as gears and housings.
Conclusion
Lost foam casting has emerged as a viable option for manufacturing complex metal parts, owing primarily to its use of innovative foam and coating materials. The advantages of precision, cost efficiency, and reduced waste make it an attractive choice for industries looking to improve their manufacturing processes. As technology continues to evolve, the future of lost foam casting will likely see further advancements in materials and techniques, solidifying its place in modern manufacturing.
Post time:नोभ . 28, 2024 05:31
Next:Techniques for Achieving a Smooth Finish with Clear Resin Through Sanding