Lost Foam Casting Applications An Overview
Lost foam casting is an innovative method of metal casting that has gained significant traction in various industries due to its numerous advantages. This technique is particularly notable for its ability to produce complex shapes with high precision and excellent surface finish. The process involves creating a foam pattern that is then coated with a refractory material and subsequently filled with molten metal. As the metal flows into the mold, the foam evaporates, leaving behind a strong metal part. This article explores the applications of lost foam casting across different sectors, its benefits, and future prospects.
Applications in Automotive Industry
One of the most significant applications of lost foam casting is in the automotive industry. The demand for lightweight components that do not compromise on strength has led manufacturers to adopt lost foam methods. By using this technique, they can create intricate engine parts, transmission cases, and suspension components that meet strict performance standards while minimizing weight. The ability to reduce tooling costs and lead times makes lost foam casting an attractive option for automotive manufacturers, particularly as they aim for rapid prototyping and production.
Aerospace Components
The aerospace industry has also found compelling uses for lost foam casting. Components such as turbine casings, brackets, and housings are often subjected to rigorous testing for strength, heat resistance, and overall performance. The lost foam process facilitates the creation of complex geometries that are difficult to achieve with traditional casting methods. Moreover, the precision and surface finish obtained from lost foam casting contribute to the durability and reliability required in aerospace applications, where failure is not an option.
Industrial Machinery
In the realm of industrial machinery, lost foam casting is utilized to manufacture parts that are both robust and intricate. Components such as pumps, valves, and frames often require detailed features that enhance their functionality. The flexibility of lost foam casting allows for innovative designs that optimize performance while reducing excess material use. This characteristic not only supports sustainability efforts but also lowers production costs by minimizing waste.
Art and Sculpture
lost foam casting applications
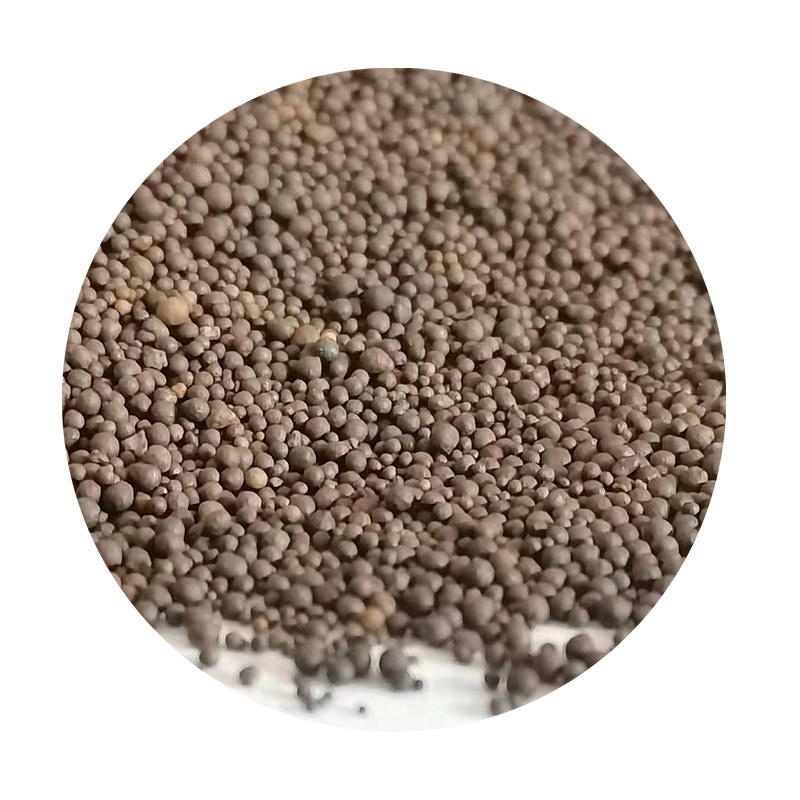
Beyond industrial applications, lost foam casting has established a niche in art and sculpture. Artists and sculptors leverage the technique to create unique and detailed works without the limitations imposed by traditional casting methods. The ability to reproduce fine details and textures makes lost foam casting a desirable option for artistic expressions, allowing for a fusion of creativity and technology.
Electrical Components
In the electrical and electronics sectors, the lost foam casting method offers an effective solution for manufacturing housings and enclosures for various devices. The technique enables the creation of lightweight yet sturdy parts that protect sensitive components from environmental factors. Additionally, the smooth surface finish achieved through lost foam casting minimizes interference with the electronic signals, which is crucial for devices operating at high frequencies.
Advantages of Lost Foam Casting
The allure of lost foam casting lies in its numerous advantages. Firstly, it allows for a higher design freedom compared to traditional casting methods, enabling the production of complex shapes without the need for elaborate molds. Secondly, it results in reduced machining costs, as parts usually require minimal additional processing. Furthermore, the overall material efficiency is superior, enriching the sustainability profile of manufacturing processes.
One of the leading benefits is the process's ability to handle a wide range of metals, including aluminum, iron, and copper alloys. This versatility makes lost foam casting a viable option for manufacturers across various sectors. The capacity to achieve high dimensional accuracy and surface finish also enhances the end product's quality, contributing to increased customer satisfaction and reduced failure rates.
Future Prospects
As industries continue to evolve, the potential for lost foam casting expands. Growth in sectors such as renewable energy, where complex and lightweight components are essential, signifies a promising future. Additionally, advancements in materials science and manufacturing technologies are likely to enhance the applicability of lost foam casting, facilitating the development of even more efficient processes.
In conclusion, lost foam casting has carved out its niche in many applications, from automotive and aerospace to art and industrial machinery. Its advantages in design flexibility, material efficiency, and production cost-effectiveness position it as a leading casting technique for the future. As technology progresses and industries seek innovative solutions to their manufacturing challenges, lost foam casting is poised to play a pivotal role in shaping the landscape of modern production.
Post time:डिस . 31, 2024 03:00
Next:Key Characteristics and Features of Foundry Sand for Effective Casting Processes