Hard Sand Casting An Efficient Metal Casting Technique
Hard sand casting, also known as sand cast molding, is a widely utilized method in the metalworking industry, prized for its versatility and cost-effectiveness. This technique involves creating a mold from a mixture of sand and a binding agent. The resulting molds are capable of withstanding high temperatures and can be used to cast a variety of metals, including aluminum, iron, and bronze.
One of the fundamental advantages of hard sand casting is its ability to produce complex shapes and intricate designs. The sand used in this process can flow into detailed patterns, allowing for precise replication of even the most complicated components. The flexibility of sand molds makes it an ideal choice for prototyping and low to medium-volume production runs, catering to industries such as automotive, aerospace, and art.
The hard sand casting process begins with the preparation of the mold. The sand is usually mixed with a binding agent like clay or resin, which helps the mold retain its shape. Once the sand is compacted around the pattern, it is removed, leaving a cavity that mirrors the desired shape of the final product. Multiple cores can also be used to create hollow sections within the casting.
hard sand casting
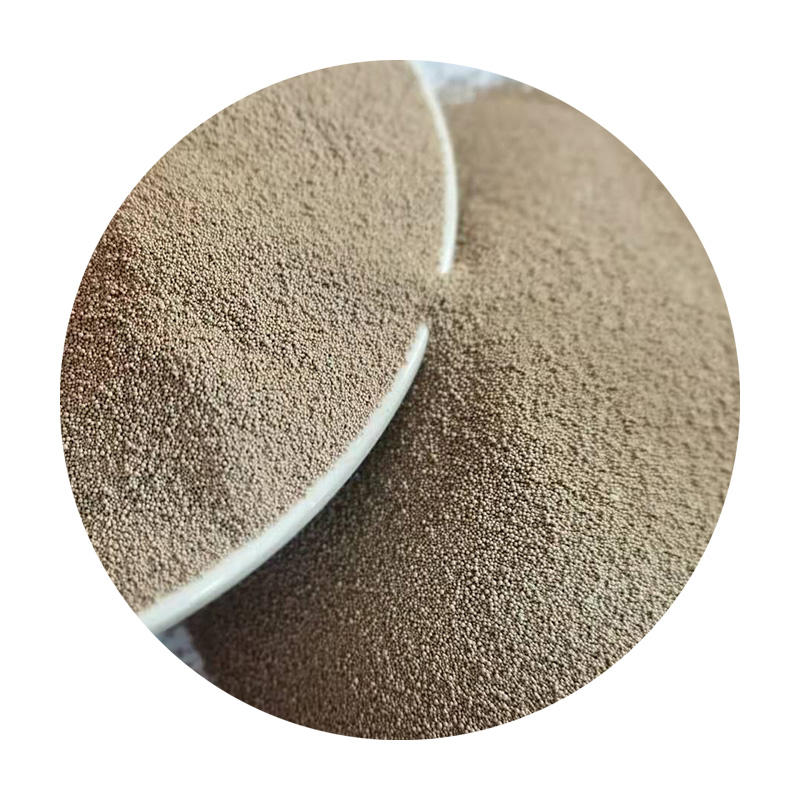
After the mold is prepared, molten metal is poured into the cavity. The temperature of the molten metal is crucial; it must be high enough to ensure proper fluidity while also preventing premature solidification. The metal fills the mold and begins to cool, solidifying over time. Once the cast piece has cooled adequately, the sand mold is broken away, revealing the finished component.
Post-casting operations are often necessary to refine the final product. These can include cleaning, machining, and surface treatment processes, which enhance the durability, aesthetics, and overall performance of the cast metal. This adaptability makes hard sand casting suitable for a wide range of applications.
Another noteworthy aspect of hard sand casting is its scalability. For small-scale operations, it allows artisans and small manufacturers to produce items with minimal investment. Conversely, for larger production needs, the process can be adapted to accommodate automated systems, ultimately increasing efficiency and output.
Despite its many advantages, there are some limitations to hard sand casting. Surface finish may not be as smooth as that achieved with other casting methods, and dimensional tolerances may require additional machining to meet specific requirements. However, the strengths of this traditional technique—such as its adaptability, efficiency, and overall cost-effectiveness—continue to make hard sand casting a preferred choice for metal casting applications around the globe. As industry demands evolve, this technique remains relevant, showcasing its enduring significance in manufacturing processes.
Post time:अक्ट . 12, 2024 20:40
Next:قیمتهای شن طلایی و روندهای بازار آن