Understanding Foundry Sand Specifications
Foundry sand is an essential material used in the metal casting process. It serves as a mold material, providing the necessary support and shape for various metal components during casting. The properties and specifications of foundry sand are critical for producing high-quality castings and achieving optimal manufacturing efficiency. This article explores the key specifications, types, benefits, and considerations when using foundry sand.
Types of Foundry Sand
Several types of foundry sands are utilized, each with specific characteristics tailored to different casting processes. The most common types include
1. Silica Sand The most widely used foundry sand due to its excellent thermal properties and availability. Silica sand is durable, has a high melting point, and can withstand the intense heat generated during the metal casting process.
2. Olivine Sand Composed mainly of the mineral olivine, this type of sand is noted for its high thermal stability and ability to withstand high temperatures. It is particularly effective for casting ferrous metals.
3. Clay Sand This sand is a mixture of sand and clay, enhancing its bonding properties. Clay sand is primarily used for making molds that require additional strength and flexibility.
4. Chromite Sand Derived from chromite ore, this sand is used for its unique thermal properties and lower thermal expansion. It is ideal for high-performance applications.
5. Zircon Sand Known for its high melting point and excellent resistance to thermal shock, zircon sand is often used in casting high-temperature alloys.
Key Specifications
When evaluating foundry sand, several specifications must be considered
1. Grain Size and Distribution The size and distribution of sand grains significantly affect the mold's surface finish and casting precision. Typically, foundry sands are characterized by their grain size distribution, which is classified into fine, medium, and coarse sands.
foundry sand specifications
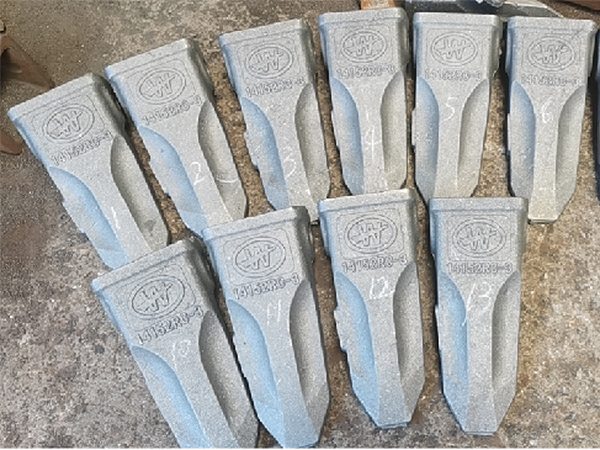
2. Shape and Roundness The shape of sand grains influences flowability and packing density. Ideally, foundry sands should have a well-rounded shape, promoting better compaction and reducing the likelihood of defects in castings.
3. Moisture Content The moisture levels in foundry sand can impact its properties, including cohesiveness and the ability to retain its shape. Too much moisture can lead to defects, while too little may inhibit proper mold formation.
4. Acidity (pH Level) The pH level of the sand can affect the chemical stability and the interaction with binders. A neutral pH is generally preferred for optimal performance.
5. Thermal Conductivity This property determines how effectively the sand transfers heat. High thermal conductivity is desirable for ensuring even heating and cooling during the casting process.
Benefits of Proper Specification
Using the right specifications for foundry sand can result in numerous benefits
- Improved Mold Strength Properly specified sand can lead to stronger molds that withstand the rigors of metal pouring, reducing the likelihood of mold collapse or deformation.
- Enhanced Surface Finish The right grain size and shape can achieve smoother surface finishes on castings, reducing the amount of post-processing required.
- Reduced Defects Adhering to specifications minimizes defects such as sand inclusion and blowholes, leading to higher yields and lower scrap rates.
- Cost Efficiency Optimizing sand selection and specifications can lead to more efficient production processes, ultimately reducing costs and improving profitability.
Conclusion
In conclusion, understanding foundry sand specifications is crucial for effective metal casting operations. The type of sand chosen, its properties, and adherence to specific criteria significantly impact the quality of castings produced. As the foundry industry continues to evolve, ongoing research and development focused on sand properties and specifications will play a vital role in enhancing manufacturing processes and ensuring the production of defect-free components. Proper selection and specification of foundry sand not only optimize the casting process but also contribute to sustainable manufacturing practices by reducing waste and improving material efficiency.
Post time:अक्ट . 13, 2024 13:46
Next:Qumda əridilmiş dəmirin xüsusiyyətləri və istifadə sahələri