Differences Between Sand Casting and Die Casting
Casting is a fundamental manufacturing process employed to create metal parts and components by pouring liquid metal into a mold. Among the various casting methods, sand casting and die casting are two prevalent techniques, each with its unique characteristics, advantages, and applications. Understanding the differences between sand casting and die casting is essential for selecting the appropriate method for specific manufacturing needs.
1. Process Overview
Sand casting is one of the oldest casting methods, dating back thousands of years. It involves creating a mold from sand, which can be easily shaped and reused. The process starts with creating a pattern of the desired part, which is then used to form a mold cavity in a mixture of sand and a binding agent. Once the mold is prepared, molten metal is poured into the cavity and allowed to solidify before the mold is broken apart to retrieve the finished part.
On the other hand, die casting utilizes a more advanced technique involving metal dies, often made from steel, to produce high-volume parts. In die casting, molten metal is injected into a pre-made mold under high pressure, which ensures a precise and consistent shape. The dies are cooled rapidly, allowing for quicker production cycles compared to sand casting.
2. Material Suitability
The types of materials used in each casting method can vary significantly. Sand casting is versatile in terms of material selection, accommodating a wide range of metals, including iron, aluminum, and various alloys. This flexibility makes it suitable for both ferrous and non-ferrous materials.
difference between sand casting and die casting
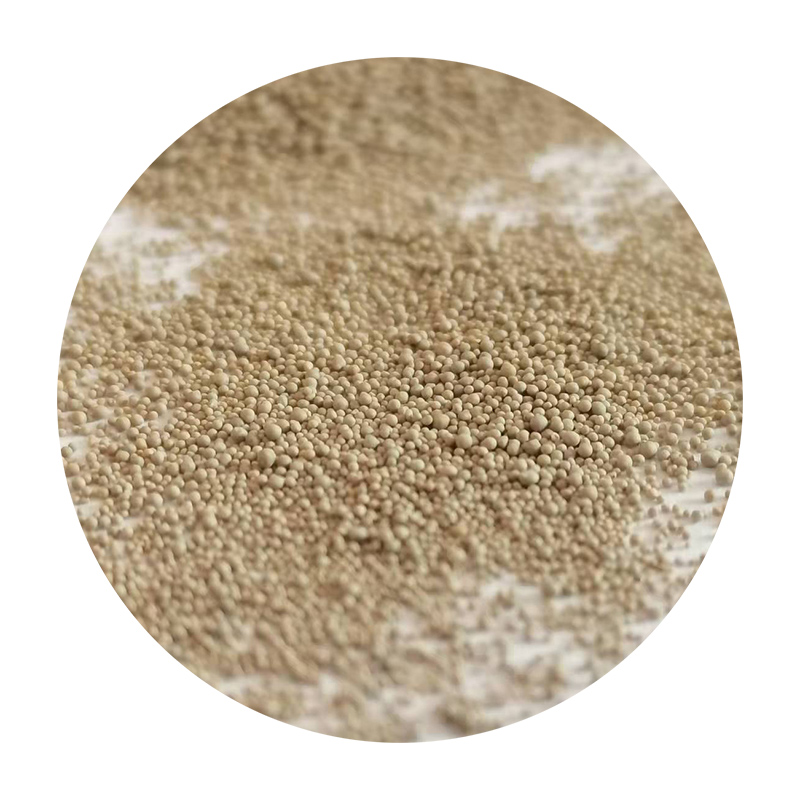
Conversely, die casting is typically limited to non-ferrous metals, primarily aluminum, zinc, and magnesium. These metals are preferred due to their desirable properties, such as light weight and corrosion resistance, as well as their ability to flow well under pressure.
3. Surface Finish and Tolerances
One of the most notable differences between the two methods is the surface finish and dimensional accuracy of the final product. Die casting generally produces parts with better surface finishes and tighter tolerances. This high precision reduces the need for extensive machining or finishing processes, making it ideal for intricate and complex designs.
In contrast, sand casting typically results in a rougher surface finish and may have larger tolerances. While this method can accommodate larger parts and complex shapes, additional machining might be necessary to achieve the desired finish or precision.
4. Cost and Production Volume
When it comes to cost, sand casting is often more economical for low-volume production due to the lower setup costs associated with making sand molds. However, for high-volume production, die casting becomes more cost-effective, as the initial investment in metal dies can be offset by the speed and efficiency of the production process.
In summary, the choice between sand casting and die casting largely depends on the specific requirements of the project, including material, production volume, tolerances, and cost considerations. Each method has its advantages and applications, making them suitable for different manufacturing needs. Understanding these differences enables manufacturers to make informed decisions, ensuring the best approach for their casting requirements.
Post time:सेप . 04, 2024 19:41
Next:describe sand casting