The Importance of Ceramic Sanding Discs in Modern Manufacturing
In the realm of manufacturing and materials finishing, abrasive tools play a critical role in achieving high-quality surface finishes. Among these tools, ceramic sanding discs have gained significant popularity across various industries. This article delves into the characteristics, advantages, and applications of ceramic sanding discs, highlighting their importance in modern manufacturing processes.
Ceramic sanding discs are composed of alumina oxide, a material known for its durability and hardness. This unique material allows these discs to withstand high temperatures and resist wear, making them ideal for heavy-duty applications. Unlike traditional sanding discs made from less resilient materials, ceramic discs exemplify longevity and efficiency in removing material. This durability translates to longer tool life and reduced replacement costs, a primary consideration for manufacturers seeking cost-effective solutions.
One of the most notable advantages of ceramic sanding discs is their aggressive cut rate. Designed to tackle tough materials such as stainless steel and hardened alloys, these discs can quickly remove stock without compromising the surface finish. This exceptional cutting ability results in enhanced productivity, as less time is spent on each sanding task. In a fast-paced manufacturing environment, where efficiency is paramount, ceramic sanding discs provide a competitive edge.
Moreover, the heat resistance of ceramic abrasives minimizes the risk of thermal damage to both the disc and the workpiece. Overheating can cause blueing or warping of metal surfaces, leading to costly rework or material waste. By utilizing ceramic discs, manufacturers can maintain quality standards while ensuring that their production processes are efficient and reliable.
ceramic sanding discs
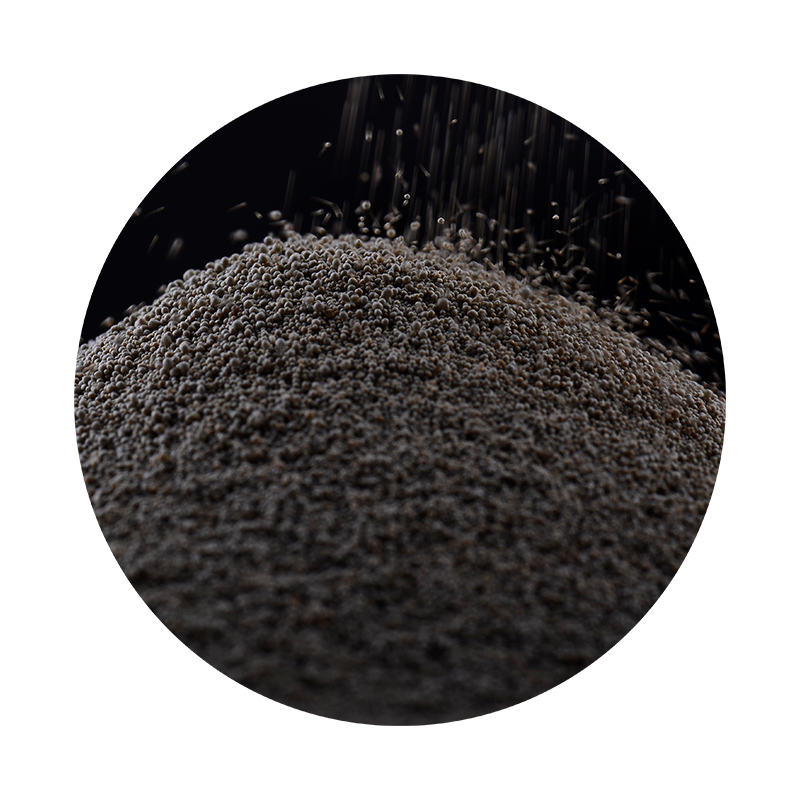
Another critical factor that makes ceramic sanding discs indispensable is their versatility. These discs are available in various grits, allowing users to select the appropriate disc for specific applications, from coarse grinding to fine sanding. Whether finishing metal components, automotive parts, or woodworking projects, ceramic sanding discs can be tailored to meet a wide range of fabrication needs.
In addition to their functional benefits, ceramic sanding discs also promote safety in the workplace. The robust construction of these discs leads to fewer breakages during use, reducing the risk of injury from flying debris or shattered fragments. This durability contributes to a safer working environment, which is an essential consideration for employers focused on the well-being of their workforce.
The rise of ceramic sanding discs in manufacturing is also supported by advancements in technology. Modern manufacturing techniques continue to enhance the performance of these abrasives, leading to the development of specialized products tailored for specific industries. As industries evolve and new materials emerge, ceramic sanding discs are poised to adapt, ensuring they remain a vital tool in the toolkit of manufacturers around the globe.
In conclusion, ceramic sanding discs are a cornerstone of effective material finishing in today's manufacturing landscape. Their durability, aggressive cutting, heat resistance, versatility, and safety features make them an ideal choice for a myriad of applications. As technology continues to advance, the significance of ceramic sanding discs will only grow, reinforcing their position as an essential component in achieving high-quality finishes and operational efficiency in manufacturing processes.
Post time:नोभ . 15, 2024 20:11
Next:low volume sand casting