The Transformative Impact of 3D Printing on Sand Casting
In recent years, the manufacturing industry has witnessed a massive shift driven by advancements in technology. One of the most intriguing developments is the integration of 3D printing into traditional sand casting processes. This synergy not only enhances the efficiency of manufacturing but also introduces new possibilities in design and production that were previously unimaginable.
Sand casting has been a fundamental method for producing metal parts for centuries. The process involves creating a mold from sand into which molten metal is poured. Traditionally, the creation of these molds can be labor-intensive, time-consuming, and prone to human error, particularly when dealing with complex geometries. However, with the advent of 3D printing, the landscape of sand casting is evolving dramatically.
The Transformative Impact of 3D Printing on Sand Casting
Moreover, the ability to quickly produce prototype molds using 3D printing enables a more agile development process. Engineers can design, test, and modify parts within days rather than weeks, drastically shortening the product development cycle. This rapid iteration capabilities allow companies to respond swiftly to market demands and innovate at an accelerated pace.
3d printing sand casting
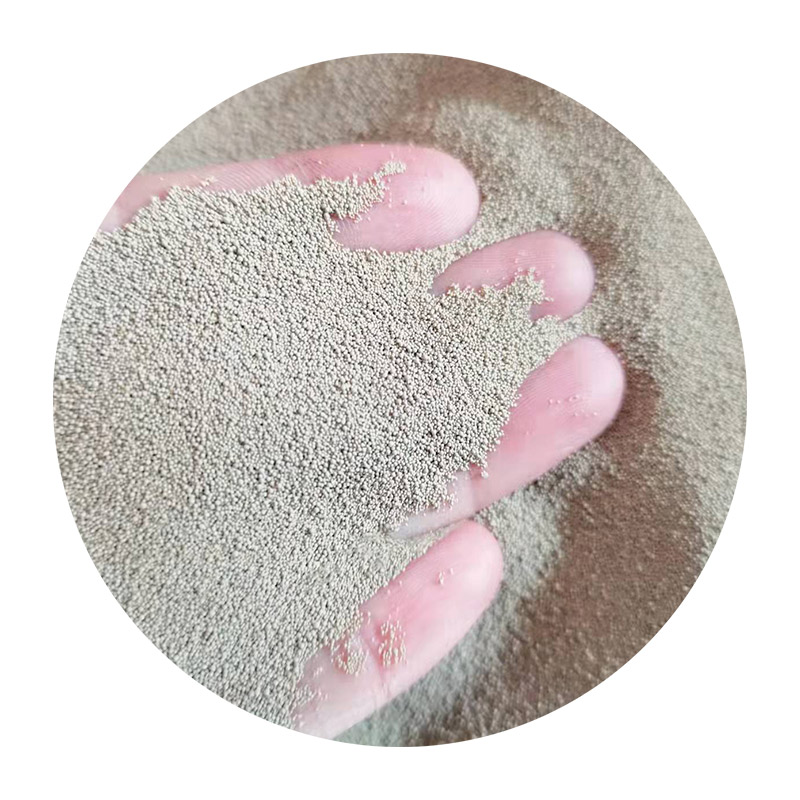
The incorporation of 3D printing in the sand casting process also leads to significant improvements in sustainability. Traditional mold-making methods often involve considerable material waste, but 3D printing allows for a more controlled and precise approach that minimizes excess materials. Additionally, the use of sand as the primary mold material is advantageous; it is abundant and recyclable, resulting in a more eco-friendly casting process. The ability to reuse and recycle sand effectively can lead to lower operational costs and a reduced environmental footprint.
However, the transition to a hybrid manufacturing model that combines 3D printing and sand casting is not without its challenges. One of the primary hurdles is the initial investment in 3D printing technology, which can be substantial for small and medium-sized enterprises. Additionally, there is a need for upskilling workers to operate new technologies and to understand the nuances of designing for 3D printing. Companies must invest in training programs to bridge this knowledge gap and fully leverage the capabilities of advanced manufacturing.
Despite these challenges, industries ranging from aerospace to automotive are beginning to embrace this innovative approach. For instance, aerospace companies utilize 3D-printed sand molds to produce lightweight, complex parts that contribute to fuel efficiency. Similarly, in the automotive sector, manufacturers are using these techniques to rapidly develop prototype components for testing and validation, thereby maintaining competitiveness in a fast-paced market.
As the technology continues to evolve, we can expect to see even greater integration of 3D printing with sand casting. The future holds promising possibilities, such as improving the properties of cast parts through the incorporation of composites and other materials within the sand molds. Furthermore, advancements in materials science may lead to more robust and versatile printing materials, enhancing the quality of the final products.
In conclusion, the fusion of 3D printing with sand casting signifies a monumental shift in manufacturing practices. This blend not only streamlines production processes but also fosters innovation while promoting sustainability. As the industry continues to adapt and evolve, manufacturers who embrace these changes are poised to gain a significant competitive edge in the marketplace. The path ahead is filled with potential and promises a future where traditional manufacturing techniques are enhanced through digital technologies, allowing for greater creativity, efficiency, and environmental responsibility.
Post time:डिस . 04, 2024 22:54
Next:sand casting stainless steel