Advancements in 3D Printing for Sand Casting
The manufacturing landscape is evolving at an unprecedented pace, particularly in the realm of metal casting. Among the most groundbreaking developments in this field is the application of 3D printing technology for sand casting. This innovative approach not only enhances efficiency and accuracy but also opens the door to a myriad of design possibilities that traditional methods simply cannot match.
Understanding Sand Casting
Sand casting is one of the oldest and most widely used casting methods, where a liquid metal is poured into a mold made of sand. The mold is created by compacting sand around a pattern that represents the final shape of the casting. Once the metal solidifies, the sand mold is removed, revealing the finished product. While effective, traditional sand casting has its limitations, including long lead times for creating patterns and molds, difficulty in achieving complex geometries, and concerns over accuracy and surface finish.
The Role of 3D Printing
3D printing, or additive manufacturing, refers to the process of creating a three-dimensional object layer by layer from a digital model. When applied to sand casting, 3D printing can be used to produce sand molds and cores directly, bypassing the need for traditional patterns altogether. This shift has significant implications for speed, cost, and design flexibility.
Advantages of 3D Printed Sand Molds
1. Speed and Efficiency One of the most significant advantages of 3D printing for sand casting is the drastic reduction in lead time. Traditional methods often require several weeks to create patterns and molds. In contrast, 3D printing can produce sand molds in a matter of days, if not hours. This rapid turnaround is particularly beneficial for industries that require quick prototyping and shorter production runs.
2. Design Freedom The layer-by-layer approach of 3D printing enables the fabrication of complex geometries that would be remarkably challenging, if not impossible, using traditional sand casting techniques. Features such as intricate internal channels or undercuts can be designed and produced without the constraints imposed by conventional mold-making processes.
3d printing for sand casting
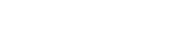
3. Cost-Effectiveness While there may be upfront costs associated with acquiring 3D printing technology, the long-term savings can be substantial. By eliminating the need for traditional patterns and reducing material waste, manufacturers can lower overall production costs. Additionally, the ability to rapidly iterate designs can lead to faster product development cycles and reduced time to market.
4. Customization In today’s manufacturing landscape, customization is king. With 3D printing, manufacturers can easily adjust designs for unique applications or customer specifications without incurring significant costs or lead time penalties. This is particularly advantageous for niche markets or specialized components.
5. Reduced Material Waste Traditional sand casting methods generate significant waste in the form of excess material and failed patterns. 3D printing, however, allows for more precise use of materials, contributing to a more sustainable manufacturing process by minimizing waste and making it possible to recycle used sand.
Challenges and Future Prospects
Despite its numerous advantages, 3D printing for sand casting is not without its challenges. Material properties, surface finish, and post-processing requirements are areas that need ongoing research and development. Additionally, the technology’s adoption across the industry requires a cultural shift, as many manufacturers are accustomed to traditional practices.
Looking ahead, the future of 3D printing in sand casting is promising. As advancements in materials science and printing technology continue, we can expect to see improvements in the strength and durability of 3D printed molds. Furthermore, with the rise of Industry 4.0, integrating 3D printing into smart manufacturing ecosystems will likely enable even greater efficiencies and innovation.
Conclusion
In summary, 3D printing for sand casting represents a transformative development within the manufacturing sector. By enabling faster production times, greater design flexibility, and reduced waste, this technology is poised to redefine the boundaries of what is possible in metal casting. As more companies begin to embrace 3D printing, we will likely witness a profound shift in manufacturing paradigms, leading to enhanced creativity and improved operational efficiencies in the years to come. The journey of 3D printing in sand casting is just beginning, and its potential for revolutionizing the industry is boundless.
Post time:अक्ट . 06, 2024 21:05
Next:components of sand casting