The Importance of Sand Used in Sand Casting
Sand casting is one of the oldest and most widely used metal casting processes, dating back thousands of years. This technique involves creating a mold from sand, into which molten metal is poured to create a variety of components and structures. The choice of sand used in this process is crucial, as it significantly impacts the quality and characteristics of the final product.
Types of Sand Used in Sand Casting
The most common type of sand used in sand casting is silica sand, primarily due to its availability and excellent properties. Silica sand consists mainly of silicon dioxide (SiO2) and is favored for its high melting point, which makes it suitable for casting metals with melting temperatures significantly higher than that of the sand. Other types of sands are also utilized, such as olivine sand, which is known for its superior thermal properties and resistance to chemical reactions, and zircon sand, which has excellent thermal stability. Each type of sand has unique characteristics that affect the casting process and the resulting metal part.
Properties of Molding Sand
The properties of molding sand are vital for successful sand casting. Key properties include cohesiveness, refractoriness, permeability, and the ability to retain shape. Cohesiveness ensures that the sand particles stick together to form a stable mold, while refractoriness allows the mold to withstand the high temperatures of molten metal without breaking down. Permeability is essential for gas escape during the pouring process, preventing defects in the cast piece. Additionally, the sand must be able to retain its shape during the pouring process to ensure dimensional accuracy.
sand used in sand casting
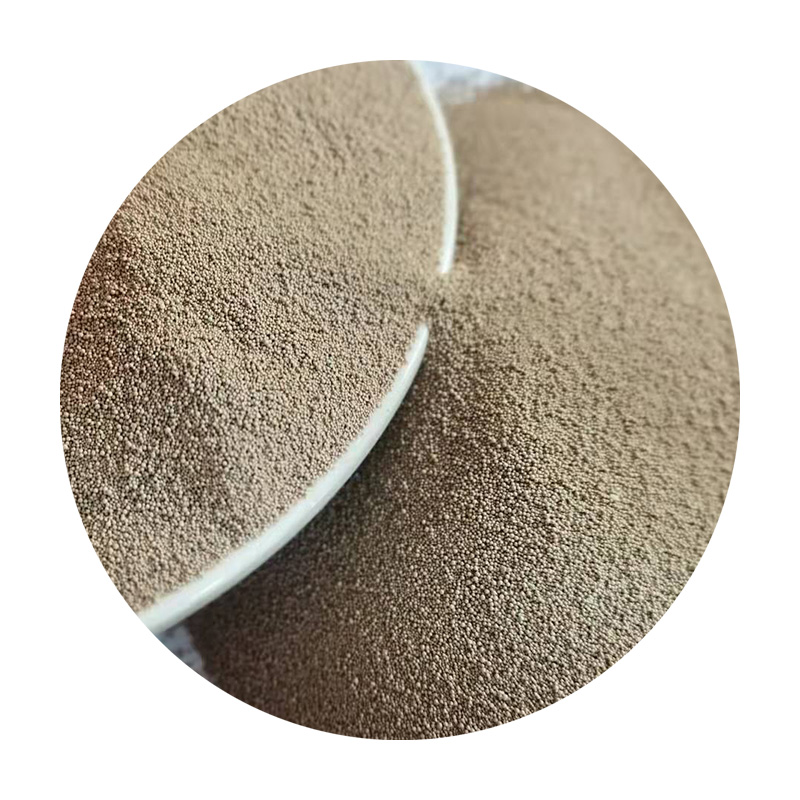
The Sand Casting Process
The sand casting process begins with the preparation of the molding sand, which is typically a mixture of sand, clay, and water. The clay acts as a binder, holding the sand grains together. Once the mixture is ready, it is packed around a pattern designed to create the shape of the desired object. After the mold is formed, the pattern is removed to leave a cavity, which is where the molten metal will be poured.
Following the pouring of the metal, the casting is allowed to cool and solidify. Once cooled, the mold is broken apart, and the metal part is removed. The sand can often be reused after proper treatment, adding to the sustainability of this process.
Conclusion
In conclusion, the choice and properties of sand used in sand casting play a pivotal role in determining the quality of the final product. Understanding the characteristics of different types of sand and their behavior during the casting process is essential for manufacturers aiming to produce high-quality castings. As industries evolve and new materials emerge, ongoing research and development in molding sands will continue to enhance the efficiency and effectiveness of sand casting, ensuring its relevance in modern manufacturing.
Post time:Nov . 06, 2024 18:39
Next:Exploring Cost Factors in Sand Casting Processes and Pricing Trends