Fine Casting Sand A Crucial Element in Metal Foundry Processes
Fine casting sand plays an essential role in the metal foundry industry, serving as the foundational material for creating molds in which molten metals are poured to form various components. This article explores the properties of fine casting sand, its types, applications, and the impact of its quality on the casting process.
What is Fine Casting Sand?
Fine casting sand, often referred to simply as casting sand, is a finely granulated material composed primarily of silica (SiO2) and other additives. Its grain size typically ranges from 0.1 mm to 0.5 mm, ensuring that it can form a tight mold that is essential for producing intricate shapes and fine details in casted components. The properties of casting sand, such as its permeability, cohesiveness, and thermal stability, significantly influence the quality of the final cast product.
Types of Fine Casting Sand
There are various types of fine casting sands used in the foundry industry, each with specific properties suitable for different applications
1. Silica Sand The most common type, silica sand is inexpensive and readily available. Its high melting point and strength make it ideal for a range of metal casting processes.
2. Zircon Sand This type of sand has a higher thermal resistance than silica, making it suitable for casting high-temperature alloys. It also offers lower thermal expansion, reducing the risk of defects in high-precision castings.
3. Chromite Sand Known for its excellent resistance to thermal shock, chromite sand is used for casting ferrous metals. Its unique composition allows it to withstand high temperatures and maintain dimensional accuracy.
4. Green Sand A mixture of naturally occurring sand, clay, and water, green sand is commonly used in the sand casting process. Its moisture content provides necessary bonding properties, making it easy to manipulate and shape.
fine casting sand
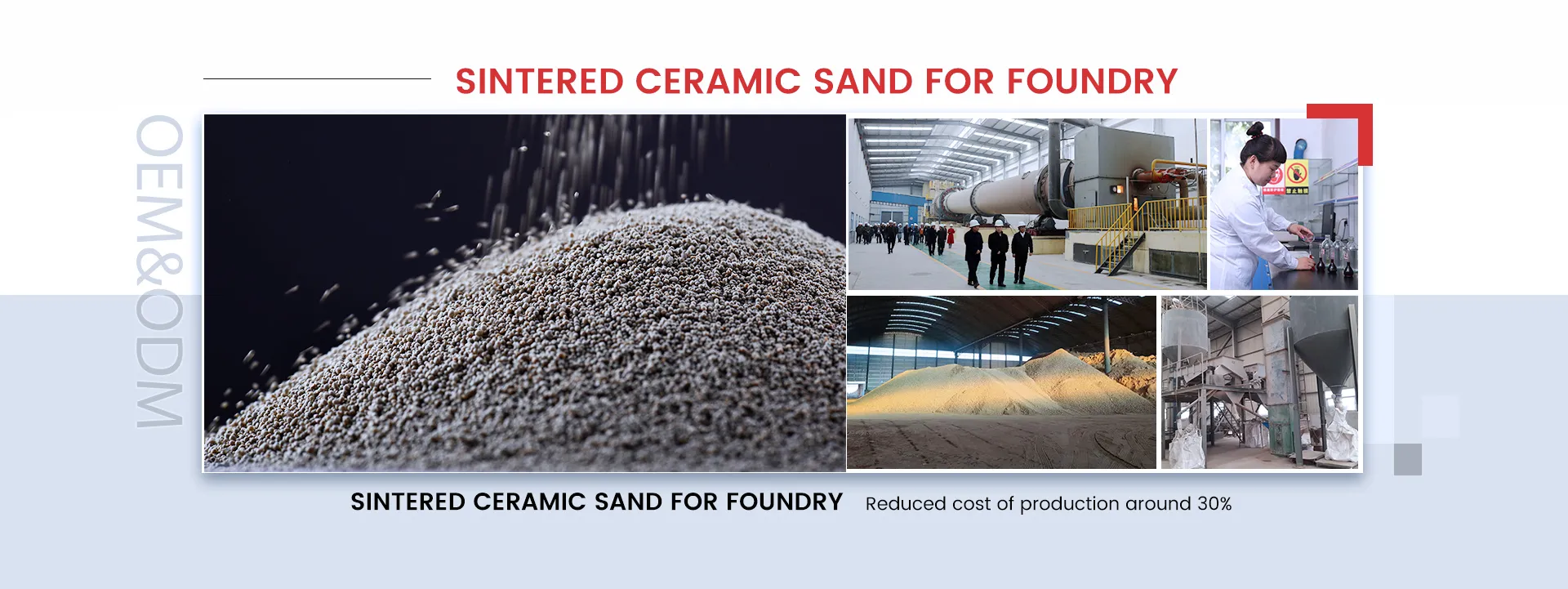
5. Synthetic Sand Engineered to enhance specific properties, synthetic sands can offer superior performance, reduced environmental impact, and less variability compared to natural sands.
Applications in Foundry Processes
Fine casting sand is used across various casting techniques, including sand casting, where it is packed around a pattern to create a mold. Once the mold is formed and the pattern removed, molten metal is poured into the cavity. The characteristics of the sand affect the cooling rate of the metal, the mold's strength, and the surface finish of the final product.
Fine casting sand is not only crucial in producing metal components for the automotive, aerospace, and machinery industries but also for art and sculpture, where detailed work is essential. As manufacturers continue to push for precision and efficiency, the importance of selecting suitable fine casting sand remains paramount.
Quality and Performance Considerations
The quality of fine casting sand directly impacts the casting process and the final product's integrity. Factors such as grain size distribution, roundness, moisture content, and chemical composition are vital in ensuring optimal performance. For instance, well-graded sands provide better compaction and strength, which can lead to fewer casting defects.
Furthermore, advancements in technology have allowed for better testing and characterization of sands, enabling foundries to optimize their sand selection processes. Continuous innovation in sand recycling methods has also contributed to sustainability, reducing waste and ensuring that high-quality sand can be reused effectively.
Conclusion
Fine casting sand is an indispensable component of the metal casting industry, influencing everything from mold creation to the quality of finished products. Understanding its properties and types allows manufacturers to make informed decisions, ultimately leading to enhanced productivity and superior castings. As the demand for high-quality cast components grows, the need for reliable and effective fine casting sand will continue to be a focus for foundries around the world.
Post time:Oct . 13, 2024 11:59
Next:ceramic foundry sand