The Importance of Sanding in 3D Printing
3D printing has revolutionized manufacturing and prototyping across numerous industries, offering unparalleled opportunities for customization, rapid prototyping, and complex geometries. However, despite its many advantages, 3D printed products often require post-processing to achieve the desired surface finish and aesthetic appeal. One of the most critical steps in this post-processing phase is sanding. This article explores the importance of sanding in 3D printing, the techniques involved, and its impact on the final product.
The Need for Sanding in 3D Printing
While 3D printing can create intricate designs, it frequently leaves visible layer lines and rough surfaces, particularly when using Fused Deposition Modeling (FDM) technology. Layering is an inherent characteristic of additive manufacturing; however, it can detract from the quality of the final piece, especially in applications where aesthetics matter or where a smooth surface is critical for functionality, such as in mechanical parts that require close tolerances.
Sanding smooths out these imperfections and prepares the surface for further finishing processes, such as painting or applying other coatings. This is particularly important in industries such as automotive, aerospace, and consumer goods, where the look and feel of a product can significantly impact consumer perceptions and product performance.
Techniques and Best Practices for Sanding
1. Choosing the Right Sandpaper The efficacy of sanding largely depends on the sandpaper used. It is essential to start with a coarser grit (around 80-120) to remove larger imperfections and layer lines. Once these are diminished, the process should shift to finer grits (220 and above) to achieve a smoother finish.
2. Wet vs. Dry Sanding Wet sanding, which involves using sandpaper with water or other lubricants, can prevent clogging and produce less dust. It is particularly effective on materials like PLA and PETG, commonly used in 3D printing. Dry sanding is generally faster but can create more dust and may wear out the sandpaper more quickly.
3. Using a Sanding Sponge or Block For flat surfaces, a sanding block or sponge can help maintain even pressure and avoid uneven spots. These tools also allow for better control over the sanding process, ensuring a smooth and uniform finish.
sanding 3d printed
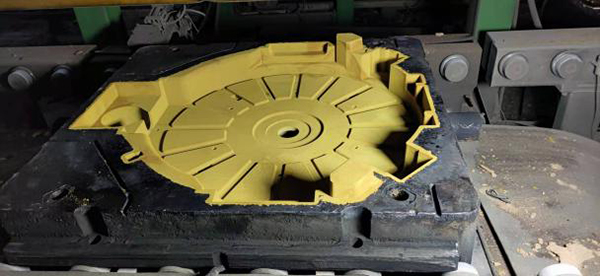
4. Light Pressure and Patience Applying too much pressure can lead to uneven surfaces or even damage the printed part. Light pressure, combined with patience, often yields better results. Sanding should be performed gradually, allowing the sandpaper to do the work without forcing it.
5. Cleaning Between Grits After using a coarser grit, it is vital to clean the printed part to remove any dust and debris before moving on to finer grits. This not only prevents larger particles from scratching the surface during the finer sanding process but also provides clearer feedback on the surface finish.
The Benefits of Proper Sanding
Proper sanding of 3D printed components can yield several benefits
- Enhanced Aesthetics A smooth, well-sanded surface can significantly enhance the visual appeal of a product, making it more attractive to consumers and stakeholders. - Improved Functionality For mechanical parts that fit together or need to slide against one another, a smoother finish can lead to reduced friction, wear, and overall improved performance.
- Better Adhesion for Finishes When preparing a surface for painting or coating, sanding creates a texture that allows the finish to adhere better, ensuring a longer-lasting and more durable surface.
- Increased Professionalism For businesses, delivering a product with a high-quality finish demonstrates professionalism and can differentiate a brand in a competitive market.
Conclusion
Sanding is an essential step in the post-processing of 3D printed products, transforming them from their raw printed state into polished, functional, and visually appealing items. By mastering the techniques of sanding, individuals and businesses can significantly enhance the quality and usability of their 3D printed parts. Whether for personal projects or commercial applications, investing time and effort in sanding can make a substantial difference in the final outcome.
Post time:Dis . 13, 2024 06:55
Next:Sustainable Approaches for Reusing Foundry Sand in Manufacturing Processes