Sand Casting An Overview
Sand casting, also known as sand mold casting, is a widely used metal casting process characterized by its simplicity and versatility. Originating over 5,000 years ago, this method continues to be a preferred technique among foundries for producing complex metal components. The process involves creating a mold from sand, which is then used to shape molten metal into desired objects. This article explores the intricacies of sand casting, its advantages, challenges, and applications.
The Sand Casting Process
The sand casting process begins with the preparation of the sand mixture, which typically consists of silica sand, clay, and water. The sand must be carefully manipulated to achieve the right consistency to retain its shape during the casting process. Once the sand mixture is ready, it is packed around a pattern, which is a replica of the final product. The pattern is often made of metal or plastic and is slightly oversized to account for shrinkage during cooling.
After the sand is packed tightly around the pattern, it is then removed carefully to create a mold. The mold is often made in two halves, known as cope and drag. Once the halves are assembled, the mold is complete and ready for casting. Molten metal, typically aluminum, iron, or bronze, is poured into the mold cavity through a sprue. After the metal has cooled and solidified, the mold is broken apart to reveal the finished casting.
Advantages of Sand Casting
One of the primary advantages of sand casting is its adaptability. It can be used to produce very large parts as well as small, intricate components. The process is suitable for various metals, making it versatile for different industries. Additionally, sand casting is relatively inexpensive compared to other casting processes. The materials involved are widely available, and the tools required for production, such as the sand and mold, are cost-effective.
Another significant advantage is the ability to create complex geometries
. Intricate designs that are difficult to produce with other techniques can be easily achieved through sand casting. This flexibility makes it a popular choice in industries such as automotive, aerospace, and machinery, where both simple and complex parts are frequently required.sand casting
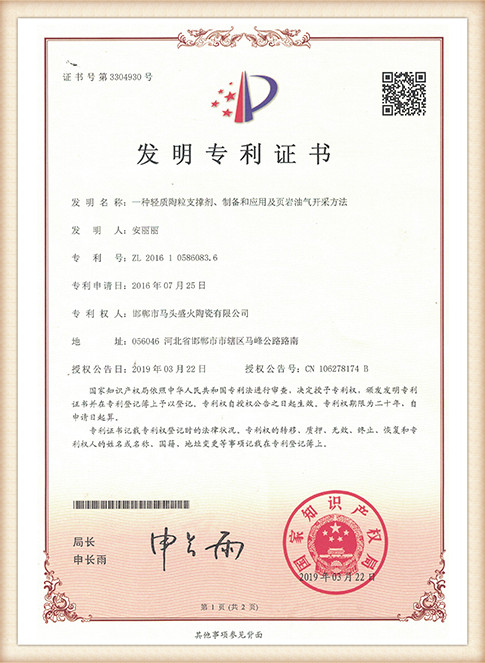
Challenges in Sand Casting
While sand casting presents numerous advantages, it is not without its challenges. One significant drawback is the surface finish of the castings. Parts produced through sand casting can have a rough surface compared to those made with more advanced techniques like investment casting. This may necessitate additional machining operations to achieve the desired smoothness and dimensional accuracy.
Moreover, the process can lead to defects in the castings, such as sand inclusions, misruns, and blowholes. These imperfections often require careful monitoring during the production process and may result in increased scrap rates. Therefore, foundries must invest in proper quality control measures to minimize defects and ensure high-quality outputs.
Applications of Sand Casting
Sand casting is used across various industries due to its flexibility and adaptability. The automotive industry relies heavily on sand casting for producing engine blocks, cylinder heads, and transmission cases. In aerospace, components such as turbine housings and structural parts are often manufactured using this technique. Additionally, the construction industry benefits from sand casting for items like brackets, supports, and foundations.
Beyond traditional industries, the art of sand casting is gaining traction in custom metalwork and artistic applications. Artists and sculptors are increasingly employing sand casting techniques to create unique sculptures and installation pieces, showcasing the method’s adaptability beyond industrial use.
Conclusion
In summary, sand casting is a time-honored technique that continues to play a critical role in modern manufacturing. Its ability to accommodate a wide variety of shapes and materials makes it an essential process in industries ranging from automotive to aerospace. While challenges such as surface finish and defect rates exist, the benefits of sand casting make it a valuable technique for creating both functional and artistic metal objects. As technology continues to evolve, the future of sand casting holds promising potential, especially as new materials and methods are integrated into the process. Sand casting stands as a testament to the innovation and durability of traditional manufacturing methods.
Post time:Dis . 12, 2024 16:55
Next:investment casting sand