Understanding the Costs of Sand Casting
Sand casting, one of the oldest and most versatile manufacturing processes, involves creating metal parts by pouring molten metal into a sand mold. This method is widely used across various industries, including automotive, aerospace, and construction. However, one question that often arises is, How much does sand casting cost? To tackle this, we need to consider several factors that influence the overall expense of the process.
1. Material Costs
The first major component of sand casting costs is the materials used. The primary materials include sand, metal alloys, and binders. The type of metal selected will significantly impact the costs; for instance, aluminum and bronze tend to be less expensive than specialized alloys such as titanium. Moreover, the quality of sand and the type of binder used for the mold can also affect pricing. High-quality sand and specialized binders may increase the initial costs but can lead to better mold integrity and surface finish.
2. Tooling and Setup Costs
Before the actual casting can take place, tooling must be created, which includes the design and production of the molds. This phase can be quite costly, especially for complex shapes or larger parts that require precision. The cost of creating the mold will generally depend on its material, complexity, and the equipment used. For a simple sand mold, costs can range from a few hundred to several thousand dollars. Furthermore, if the production volume is high, the upfront tooling investments can be spread over more units, reducing the per-piece cost.
3. Labor Costs
how much does sand casting cost
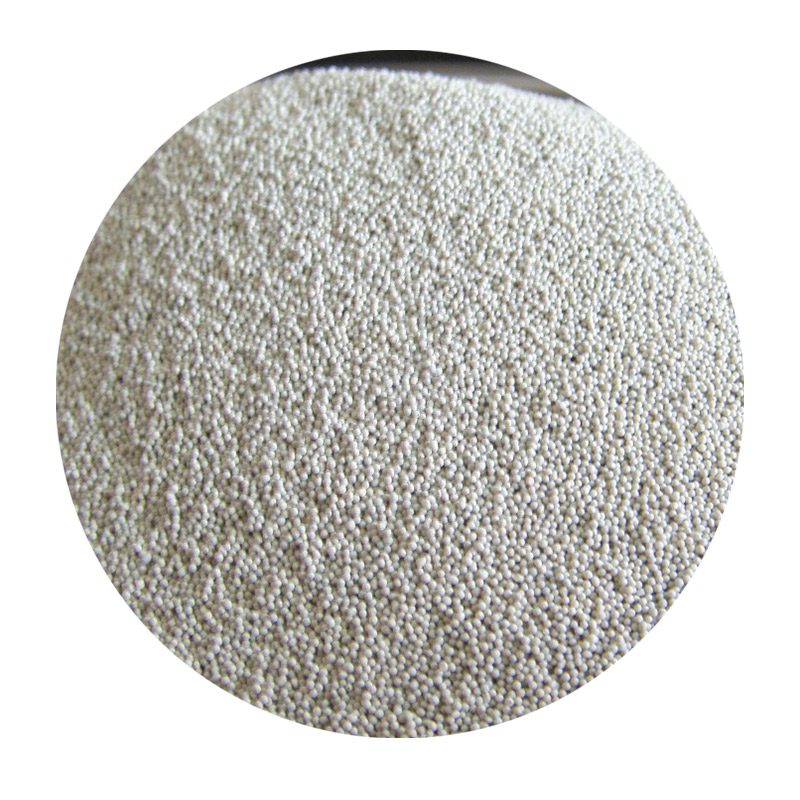
Labor is another significant factor contributing to the total cost of sand casting. The manufacturing process requires skilled workers to prepare molds, pour metal, and conduct post-casting operations like machining and finishing. The labor costs can vary by region, based on local wages and the intricacy of the operations required. For example, if a casting facility is located in an area with a high cost of living, labor expenses will naturally be higher.
4. Production Volume
The scale of production plays a crucial role in determining the cost per unit of sand casting. In general, sand casting is more economical for larger batches. The initial costs associated with mold creation can be spread over a larger number of units, thus reducing the overall cost per piece. Conversely, for low volume or single-part production, the initial tooling costs can dominate the total expense, making it less economically viable.
5. Finishing and Post-Processing Costs
Once the casting has cooled and solidified, it often requires additional finishing processes such as grinding, machining, or surface treatment to meet specific tolerances and surface quality. These finishing operations add to the overall cost. Depending on complexity and required specifications, these processes can range from minimal additional costs to substantial ones.
Conclusion
In summary, the cost of sand casting can vary widely based on several factors, including material choice, tooling design, labor rates, production volume, and finishing requirements. While it can be cost-effective for large volumes, the expenses can climb significantly for small runs due to the upfront investment in tooling and setup. Therefore, before embarking on a sand casting project, it’s essential to evaluate these factors and conduct a thorough cost analysis to ensure that the process aligns with your production needs and budget constraints. By understanding these components, manufacturers can make more informed decisions and better navigate the intricacies of sand casting costs.
Post time:Okt . 01, 2024 07:28
Next:Wysokowolumenowe odlewanie piaskowe w produkcji przemysłowej i jego zalety