Understanding the Differences Between Sand Casting and Permanent Mold Casting
Casting is a crucial manufacturing process that allows for the creation of complex shapes and structures by pouring liquid material into a mold. Among the various casting methods available, sand casting and permanent mold casting stand out due to their unique characteristics and applications. Understanding the differences between these two methods helps manufacturers select the right approach for their specific needs.
Sand Casting Overview
Sand casting is one of the oldest and most widely used casting methods, primarily due to its versatility and cost-effectiveness. In this process, a mold is created from a mixture of sand and a bonding agent, usually clay. The sand mold is formed by compacting the sand around a pattern that reflects the desired shape of the final product. Once the mold is formed, the pattern is removed, leaving a cavity into which molten metal is poured. After the metal solidifies, the sand is broken away to reveal the finished part.
One of the primary advantages of sand casting is its ability to accommodate large and complex shapes. Sand molds can be easily modified, making it possible to produce a wide variety of designs without the need for expensive tooling. Additionally, sand casting is highly cost-effective for low to medium production runs; the materials used are relatively inexpensive, and the process can be accomplished with minimal equipment.
However, sand casting does have some drawbacks. The surface finish of parts produced through this method is typically rougher than that of parts made with other casting techniques. Moreover, the dimensional accuracy is not as high, which can lead to the necessity for further machining in some cases.
Permanent Mold Casting Overview
Permanent mold casting, on the other hand, utilizes molds made from metal, usually aluminum or iron, which can be reused multiple times. The process involves a two-part mold that is preheated, and then molten metal is poured into the cavity. The use of metallic molds allows for better heat conduction, leading to faster cooling times and, consequently, improved surface finishes and dimensional accuracy.
One of the main advantages of permanent mold casting is the high-quality finish and precise dimensions it can achieve. This method is particularly well-suited for producing smaller, more intricate parts that require excellent surface quality. Additionally, because the molds can be reused, there is less material waste compared to sand casting. This makes permanent mold casting more environmentally friendly and efficient for high-volume production runs.
difference between sand casting and permanent mold casting
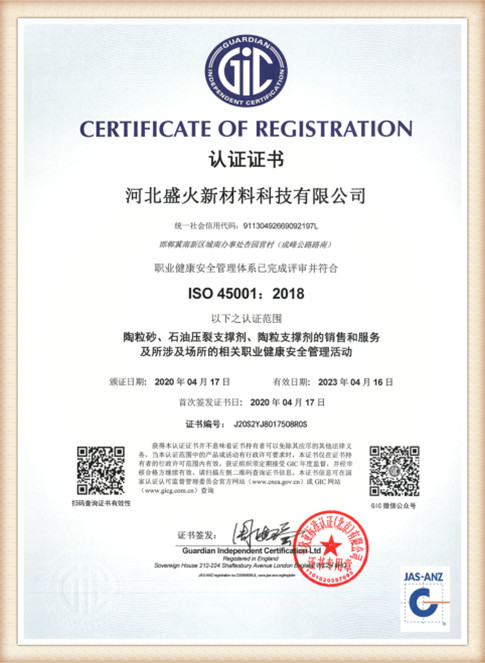
However, permanent mold casting does require a higher initial investment due to the cost of metal molds, which can make it less economical for low-volume production. Furthermore, the complexity of the part being produced can be a limiting factor, as intricate designs that may be easily formed in sand casting may not be feasible with permanent molds.
Key Differences Between Sand Casting and Permanent Mold Casting
1. Mold Material Sand casting utilizes sand and bonding agents, while permanent mold casting employs reusable metal molds. 2. Surface Finish Parts produced through permanent mold casting typically exhibit superior surface finishes compared to those produced by sand casting.
3. Dimensional Accuracy Permanent mold casting generally offers higher dimensional accuracy, making it suitable for precision components, whereas sand casting may require additional machining.
4. Production Volume Sand casting is often more economical for low to medium production runs, while permanent mold casting excels in high-volume productions due to the reusability of molds.
5. Initial Costs Sand casting has lower initial costs, making it accessible for small producers, while the investment in permanent mold casting is higher due to the cost of metal molds.
Conclusion
Both sand casting and permanent mold casting have their advantages and limitations, making them suitable for different applications. Understanding the specific requirements of a project, such as volume, complexity, and desired finish, is critical for selecting the appropriate casting method. By leveraging the strengths of each process, manufacturers can optimize production efficiency and quality in their casting operations.
Post time:Okt . 18, 2024 13:24
Next:Exploring the Key Elements of Sand Casting in Manufacturing Processes