The Art of Casting Sand for Metal An Essential Foundry Technique
Casting has been one of humanity's oldest and most significant manufacturing processes, shaping civilization through its ability to transform raw materials into functional and artistic objects. Among various casting techniques, sand casting, specifically, plays a pivotal role in the metalworking industry. This method, characterized by its versatility, affordability, and capability of producing complex shapes, has become a predominant technique for metal casting across the globe.
The Basics of Sand Casting
At its core, sand casting involves creating a mold from a mixture of sand, clay, and water. The process begins with the creation of a pattern, which is a replica of the final product. Patterns can be made from various materials, including wood, plastic, or metal, depending on the required production volume and desired precision. Once the pattern is ready, it is buried in sand to form a mold.
The sand mixture, often referred to as green sand, is compacted around the pattern, and once it hardens, the pattern is removed, leaving a cavity in the shape of the desired object. The mold then undergoes an inspection process to ensure it meets the design specifications and is free from defects. Finally, molten metal is poured into the cavity, filling the void left by the pattern.
Advantages of Sand Casting
One of the standout advantages of sand casting is its adaptability to a wide array of metals, including aluminum, iron, and copper alloys. This flexibility enables manufacturers to create everything from intricate decorative pieces to large structural components. Additionally, the process is well-suited for both small batches and large-scale productions, making it a popular choice for various industries, such as automotive, aerospace, and art.
The raw materials used in sand casting are not only cost-effective but also readily available. Green sand, the most common type, contains silica sand, which is abundant and inexpensive. This economy of resources allows for competitive pricing and accessibility for companies of all sizes. Furthermore, sand molds can be reused multiple times, reducing waste and improving efficiency.
casting sand for metal
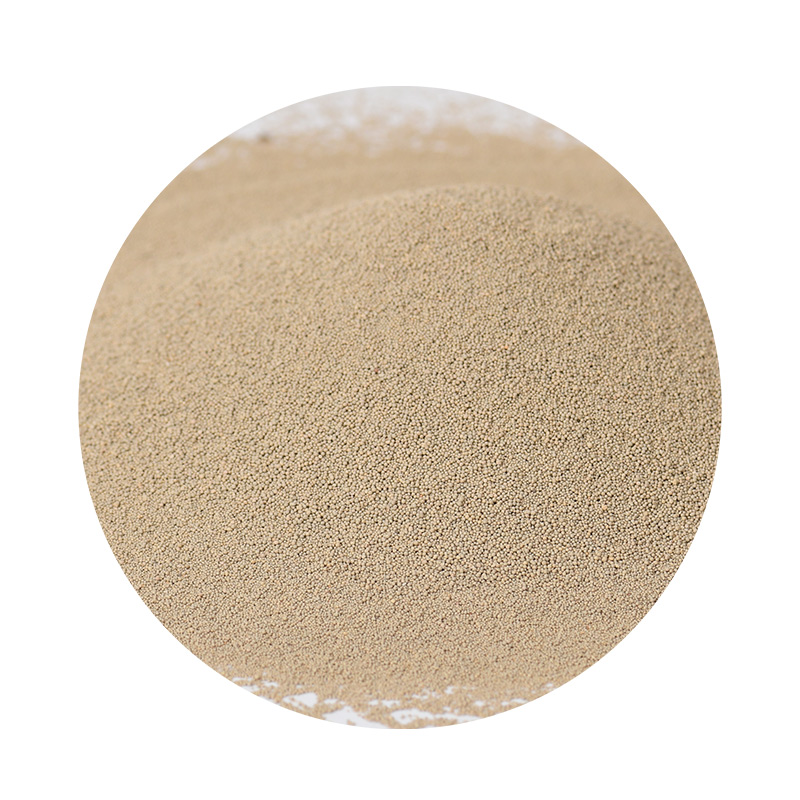
The Environmental Impact
In recent years, the foundry industry has been facing scrutiny regarding its environmental footprint. Traditional sand casting can lead to challenges, such as dust pollution and the management of spent sand. However, advancements in technology and sustainable practices are helping to mitigate these concerns. Many foundries are now employing filtration systems to capture dust emissions and recycling spent sand for repeated use. Additionally, some companies are exploring the use of eco-friendly binders that reduce harmful emissions during the casting process.
The Future of Sand Casting
As industries continue to evolve, so too do the methods and materials used in sand casting. Innovations in 3D printing technology are beginning to reshape the landscape of mold production. With 3D printers, manufacturers can create intricate patterns and molds that were previously impossible with traditional techniques. This method not only speeds up the production process but also allows for greater design flexibility and precision.
Moreover, the integration of artificial intelligence and machine learning into the casting process is enhancing quality control and optimizing production efficiency. By analyzing data from past casts, these technologies can predict potential issues and adjust parameters in real-time, resulting in fewer defects and higher-quality outcomes.
Conclusion
Sand casting remains a cornerstone of the metalworking industry, combining ancient techniques with modern advancements. Its adaptability and economic advantages ensure that it will continue to be a vital method for creating a diverse range of metal products. As the industry embraces sustainable practices and technological innovations, sand casting is poised for a bright future, maintaining its relevance in a rapidly changing manufacturing landscape. Through the enduring art of casting sand for metal, we not only celebrate the ingenuity of past artisans but also pave the way for future innovations in metal production.
Post time:Okt . 01, 2024 12:58
Next:Seramik Yüzeyleri Nasıl Zımparalanır Adım Adım Kılavuz