Understanding Materials Used for Sand Casting
Sand casting, one of the oldest and most widely used metal casting processes, involves the use of sand as a mold material. This versatile procedure can accommodate a variety of metals, making it a popular choice in industries ranging from automotive to aerospace. Understanding the materials employed in sand casting is vital for optimizing the casting process and achieving high-quality results.
The Sands
The primary material used in sand casting is sand, which serves as the main mold component. The most common type of sand is silica sand, known for its abundant availability, cost-effectiveness, and excellent thermal properties. Silica sand grains are typically sharp and angular, which aids in forming a strong mold. Other types of sand used in casting include zircon sand, chromite sand, and olivine sand. Each type has unique properties that can enhance the casting process, such as increased strength, thermal stability, and lower thermal expansion.
Binders
To enhance the mechanical strength of sand molds and cores, binders are added to the sand mixture. The most widely used binder in sand casting is clay, specifically sodium bentonite. This natural clay acts as a cohesive agent, allowing sand grains to stick together and form a durable mold. Other binders, such as resin-bonded sands or chemically bonded sand systems, are also employed for specific applications. These modern binder systems offer improved dimensional accuracy and surface finish compared to traditional clay-bound sands.
Additives
what materials are used for sand casting
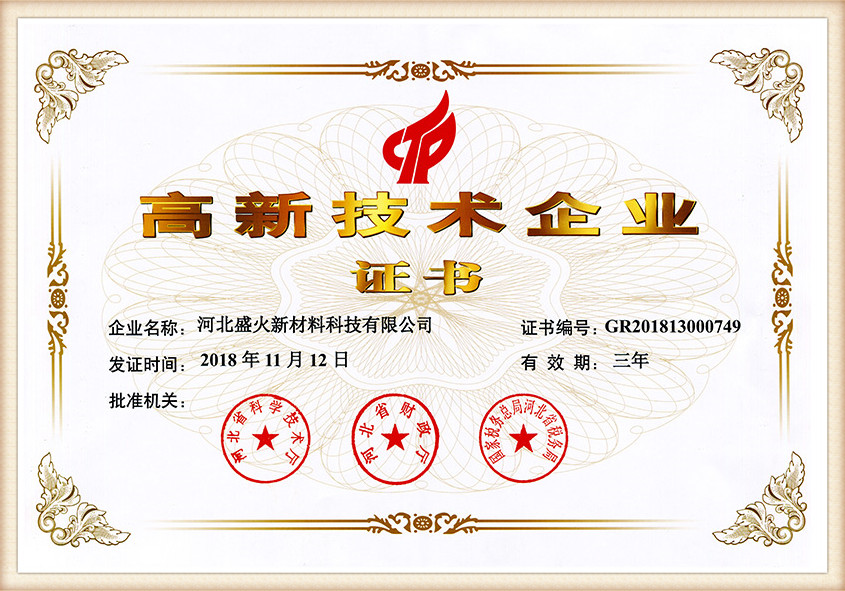
Various additives are incorporated into the sand mixture to improve its properties. For example, organic additives can be used to enhance the mold's permeability, allowing gases to escape during the pouring of molten metal. In contrast, inorganic additives may be used to increase the mold's strength and resistance to deformation under heat. These additives play a crucial role in minimizing defects such as sand burn-on or mold collapse, which can compromise the integrity of the final casting.
Metals
Sand casting is compatible with a wide range of metals, including aluminum, iron, bronze, and magnesium. The choice of metal largely depends on the desired properties of the final product. For instance, aluminum alloys are favored for their lightweight and corrosion-resistant qualities, making them ideal for automotive components. On the other hand, cast iron is valued for its excellent wear resistance and machinability, often utilized in manufacturing engine blocks and heavy machinery parts.
Coatings
Coatings are applied to the molds to improve surface finish and prevent metal from sticking to the mold. These coatings, typically made from graphite, oil, or special ceramic mixtures, create a barrier between the molten metal and the sand, reducing the likelihood of defects and ensuring easier mold removal.
Conclusion
In summary, the materials used in sand casting, including various types of sand, binders, additives, metals, and coatings, play a critical role in determining the quality and performance of the final product. Understanding these materials and their properties allows manufacturers to tailor the sand casting process to meet specific requirements, ensuring high standards of quality and efficiency in production. Ultimately, sand casting remains a fundamental technique in the metalworking industry, driven by ongoing innovations in materials and processes.
Post time:ऑगस्ट . 30, 2024 21:23
Next:3d sand printing casting