Types of Sand in Foundry
Sands play a critical role in the foundry industry, serving as the primary material for molding and casting processes. The properties of sand can greatly influence the final outcome of cast products, affecting characteristics like surface finish, dimensional accuracy, and strength. Here, we will explore the various types of sand used in foundries, highlighting their unique properties and applications.
1. Silica Sand
Silica sand is the most commonly used sand type in the foundry industry, primarily due to its availability and beneficial properties. Composed mainly of silicon dioxide (SiO2), silica sand provides good thermal stability and excellent permeability, allowing gases to escape during the casting process. This helps prevent defects such as blowholes in the final product. Its grain size and shape can be adjusted for different applications, making it versatile for various casting needs. However, it can be quite abrasive and may wear down molds over time.
2. Green Sand
Green sand is a mixture of silica sand, clay, water, and other additives. It is widely used for making molds in foundry processes due to its ability to retain moisture and form cohesive molds. The clay content gives the sand its green color, and it must be rejuvenated or reused after each casting cycle to maintain its properties. Green sand molds are beneficial for their ease of use and because they allow for rapid production rates. They are particularly suitable for iron and steel castings.
3. Resin Sand
Resin sand is an advanced molding material that incorporates resin as a binder instead of traditional clay. This type of sand provides superior surface finish and dimensional accuracy due to the rigid molds created by the resin. The resulting castings often require less machining and finishing work. Resin sand molds are typically used for high-precision applications, such as automotive parts and intricate components. The faster setting time and ability to produce thinner walls make resin sand a popular choice, despite its higher cost compared to green sand.
types of sand in foundry
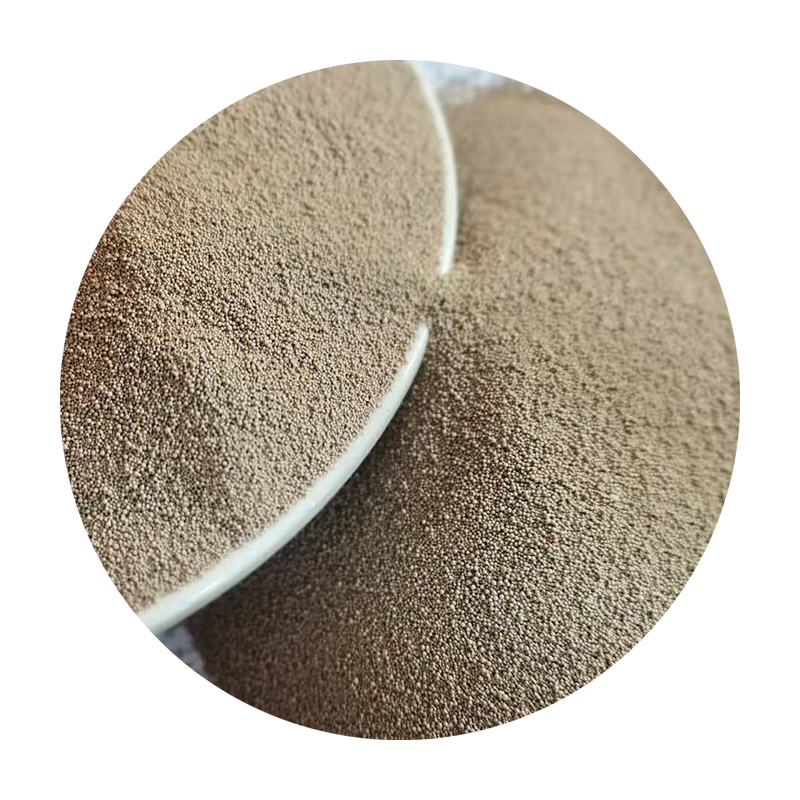
4. Shell Sand
Shell sand is created by coating fine sand grains with a thermosetting resin, allowing for the creation of thin-walled molds. This type of sand is particularly beneficial for high-volume production where accuracy and surface quality are critical. Shell molding provides excellent dimensional accuracy and a smooth finish, making it suitable for complex shapes. However, the process requires specialized equipment and can be more expensive than traditional sand systems.
5. Investment Casting Sand
Investment casting, also known as lost wax casting, employs a different type of sand process, using a more controlled and refined sand mixture for creating molds. The process involves creating a wax pattern, which is then coated with a ceramic shell. While investment casting may use various sands for specific applications, the key characteristic is the high level of detail and smooth finish it produces, making it ideal for intricate designs such as jewelry and medical components.
6. Chromite Sand
Chromite sand, composed of chromium oxide, is used for producing molds in high-temperature applications. It has excellent thermal stability, high resistance to thermal shock, and does not expand significantly when heated. These properties make chromite sand ideal for steel and high-alloy casting, where conventional silica sand may not withstand the extreme temperatures involved. Its ability to reduce casting defects also adds to its desirability in specialized applications.
Conclusion
The choice of sand in the foundry industry significantly impacts the efficiency of the casting process and the quality of final products. From traditional silica and green sands to advanced resin and shell sands, each type serves specific purposes based on desired characteristics. Understanding the various types of sand and their properties helps foundry engineers make informed decisions, ensuring optimal production outcomes and reduced waste. As foundry technology continues to evolve, the exploration of new sand materials and compositions will undoubtedly enhance casting processes even further.
Post time:नोव्हेंबर . 12, 2024 12:06
Next:china sand casting factory