Sand Casting Tolerances Understanding the Essentials for Quality Manufacturing
Sand casting is a widely used manufacturing process that allows for the creation of complex metal parts by pouring molten metal into a sand mold. This technique is favored in many industries due to its versatility and cost-effectiveness, particularly for low to medium production runs. However, achieving precise dimensions and high-quality finishes with sand casting can be a challenge. This is where understanding sand casting tolerances becomes crucial for manufacturers and designers.
Tolerances in sand casting refer to the allowable variations in the dimensions of the final cast part. These tolerances are important because they directly impact the functionality, fit, and performance of the finished product. The significance of tolerances is particularly pronounced in applications where components must interface with other parts, such as in machinery, engines, and structural assemblies.
Types of Tolerances in Sand Casting
1. Dimensional Tolerances These specify how much a dimension can deviate from the nominal size. Common dimensional tolerances in sand casting depend on several factors, including the material, the casting process, and the size of the part. Generally, sand castings are produced with tolerances in the range of ±1/16 inch for larger parts, but for smaller components, tolerances can be tighter, around ±0.01 inches.
2. Geometric Tolerances These involve the shape and fit of the final product. They ensure that features like flatness, angularity, and roundness conform to specified standards. Geometric tolerances are essential for parts that need to fit together accurately, as any deviation can lead to assembly issues.
3. Surface Finish Tolerances The quality of the surface finish is critical in many applications, especially those subject to wear and tear. Sand casting typically yields a rougher surface compared to other casting methods, such as investment casting. Surface roughness is measured in microinches, with typical sand castings having a roughness value between 250 to 500 microinches, depending on the mold design and material used.
sand casting tolerances
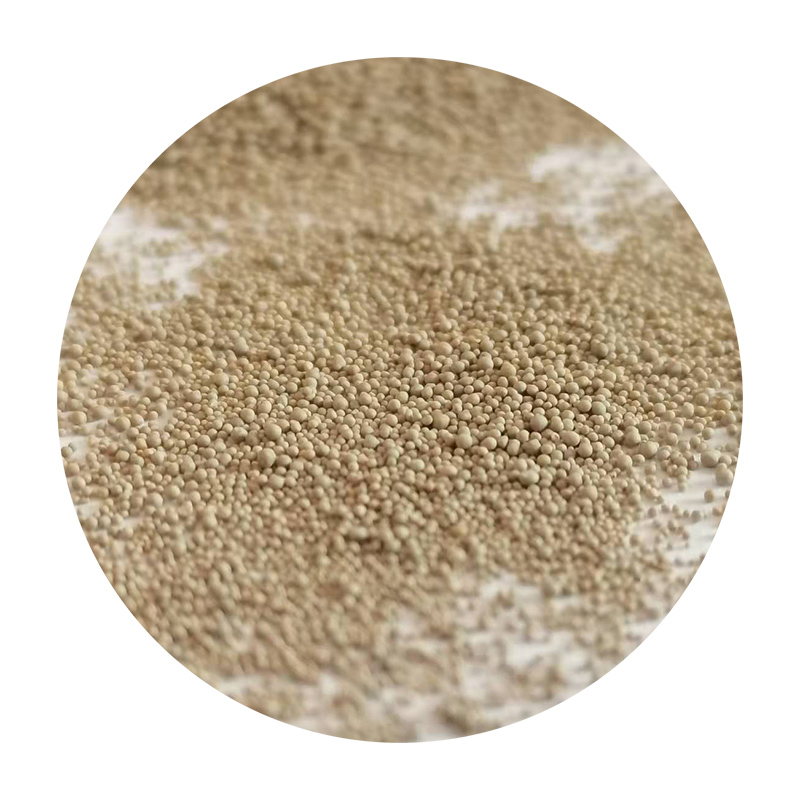
Factors Influencing Tolerances
Several factors influence the tolerances that can be achieved in sand casting
- Mold Material The type of sand and binder used to create the mold can affect its stability and detail reproduction, directly impacting the tolerances. - Pattern Design The design of the pattern used to create the mold can introduce deviations. For example, shrinkage must be accounted for, as metals typically expand when molten and contract upon cooling.
- Casting Process Control Variations in pouring temperature, speed, and cooling rates can lead to dimensional changes. Therefore, stringent process controls are essential to maintain tolerances.
Conclusion
In conclusion, understanding sand casting tolerances is vital for manufacturers aiming to produce high-quality cast parts. By recognizing the types of tolerances—dimensional, geometric, and surface finish—along with the factors that influence them, manufacturers can better control their processes, reduce waste, and improve the quality of their products. Establishing clear tolerances at the design stage and maintaining rigorous control throughout the casting process can significantly enhance the reliability and performance of sand-cast components, ensuring that they meet the needs of modern engineering applications. As industries continue to evolve, a solid grasp of these tolerances will remain an essential aspect of successful sand casting practices.
Post time:ऑक्टोबर . 13, 2024 21:47
Next:Pricing for 3D Sand Printers and Their Impact on the Market