Sand Casting Metal A Versatile Manufacturing Process
Sand casting is one of the oldest and most widely used metal casting processes in the manufacturing industry. This method involves creating a mold from sand, which is then filled with molten metal to create a desired object. The versatility, cost-effectiveness, and ability to produce complex shapes make sand casting a popular choice for various applications. In this article, we will explore the sand casting process, its advantages, limitations, and its wide array of applications in different industries.
The Sand Casting Process
The sand casting process starts with the creation of a mold. This typically involves two halves of a mold, known as the cope and the drag, which are made from a mixture of sand, clay, and water. The first step is to create a pattern of the object to be cast, generally made from metal or plastic. The pattern is pressed into the sand to create a cavity, which is then packed down to ensure it holds its shape. After removing the pattern, the two halves of the mold are assembled, and any cores needed for complex internal shapes are added.
Once the mold is prepared, molten metal is poured into the cavity through a pouring basin, allowing it to fill all the areas of the mold. The metal is typically heated in a furnace until it reaches a liquid state. After the metal cools and solidifies, the mold is broken apart, and the cast object is removed. This is often followed by cleaning processes to remove any sand residue and to refine the surfaces of the cast piece.
Advantages of Sand Casting
One of the primary advantages of sand casting is its low cost compared to other metal casting processes. The materials needed for sand molds are inexpensive and readily available, making it an attractive option for both small-scale and large-scale production. Additionally, sand molds can be reused multiple times, further driving down costs.
Another significant benefit is the flexibility of the process. Sand casting can produce parts in various sizes and complex geometries, which may not be achievable with other manufacturing methods like injection molding. It also accommodates a wide range of metals, including aluminum, bronze, brass, and iron, making it suitable for numerous applications.
Furthermore, sand casting allows for rapid prototyping. Engineers and designers can quickly create molds for testing designs, leading to faster innovation cycles in product development. This adaptability is particularly important in industries where design requirements change frequently.
sand casting metal
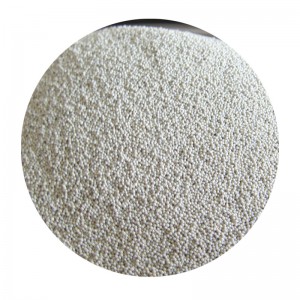
Limitations of Sand Casting
Despite its advantages, sand casting does have limitations. The surface finish of parts produced via sand casting can often be rough compared to castings produced by other methods such as investment casting or die casting. This may require additional machining processes to achieve the desired surface quality.
Another drawback is the potential for defects in the cast parts, such as sand inclusions, cold shuts, and porosity. While these issues can often be minimized with careful mold design and process control, they cannot be completely eliminated, which may compromise the performance and aesthetics of the final product.
Applications of Sand Casting
Sand casting is employed across a wide range of industries due to its versatility. In the automotive industry, it is used to create engine blocks, transmission cases, and various other components. The aerospace industry also relies on sand casting for lightweight parts that can withstand high pressures and temperatures.
Other industries using sand casting include agriculture, where it is used to produce machine components, and construction, where large metal pieces such as beams and frames are required. Even artistic applications, like sculptures and decorative metalwork, take advantage of sand casting.
Conclusion
In summary, sand casting is a crucial method in the field of metal manufacturing. Its cost-effectiveness and ability to produce complex shapes make it an attractive option for many industries. Despite its limitations in surface finish and the potential for defects, the versatility of sand casting ensures that it remains a popular choice for a multitude of applications. As technology continues to evolve, it is likely that sand casting will adapt and flourish, maintaining its place as a fundamental component of modern manufacturing processes.
Post time:सप्टेंबर . 28, 2024 06:13
Next:Fusione a schiuma persa un metodo innovativo per la produzione di componenti metallici