Properties of Foundry Sand
Foundry sand, a vital component in the casting industry, is utilized in the production of metal castings through various processes. This unique type of sand possesses specific properties that make it suitable for creating molds and cores. Understanding these properties is crucial for optimizing casting operations, reducing defects, and improving the quality of finished products.
1. Composition
The primary component of foundry sand is silica, usually in the form of quartz, which constitutes about 90-98% of the sand mixture. The remaining percentage may include clay, silt, and other additives that enhance the sand’s characteristics for casting. The uniformity of particle size and shape is critical; well-graded sand ensures better mold strength and reduces the likelihood of defects in the casting.
2. Grain Shape and Size
The shape and size of foundry sand grains directly impact its flowability, compaction, and mold strength. Spherical or rounded grains tend to flow easily, facilitating the mold-making process and achieving a dense packing of the sand. In contrast, angular or irregular grains may create void spaces and weaken the mold. The particle size is also essential; finer grains can provide better detail in the casting but may lead to higher gas retention, which can cause defects like sand inclusions.
3. Sand Strength
Foundry sand must possess adequate strength to withstand the pressures and temperatures encountered during the metal pouring process. The bonding characteristics of the sand, influenced by the presence of clay and moisture, contribute to its strength. Sands with higher clay content can offer enhanced binding capabilities, but excessive clay can lead to increased complications, such as difficulty in casting removal or defects in the final product. Understanding the balance of sand strength is therefore critical for effective core and mold production.
properties of foundry sand
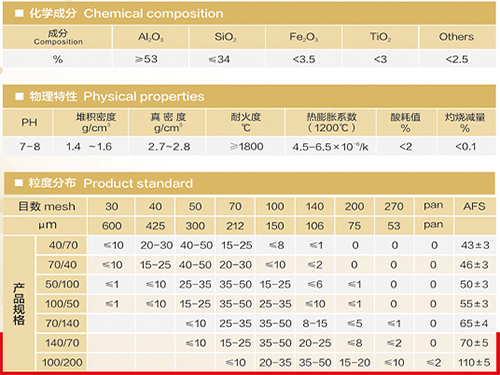
Thermal stability is another important property of foundry sand. The ability to withstand high temperatures without deforming or losing strength is vital for successful metal casting. Foundry sand is usually subjected to temperatures ranging from 1300°C to 1800°C, depending on the metal being cast. Sands with high thermal stability ensure that the molds retain their shape and structural integrity during the casting process, preventing issues such as cracking or sand erosion.
5. Moisture Control
Moisture content plays a significant role in the performance of foundry sand. Adequate moisture helps to enhance the binding properties of the sand, allowing it to maintain its shape when subjected to molten metal. However, excessive moisture can lead to issues like steam generation, resulting in casting defects. Proper control of moisture levels, often achieved through the use of additives or controlled drying processes, is essential for optimal performance.
6. Recyclability
One of the considerable advantages of foundry sand is its recyclability. After the casting process, used foundry sand can often be reclaimed, treated, and reused in subsequent casting applications. This not only reduces waste and environmental impact but also provides cost savings for foundries. The recycling processes may involve screening, cleaning, and blending with new sand to achieve the desirable properties for subsequent casts.
7. Environmental Considerations
With growing awareness regarding environmental sustainability, the foundry industry is increasingly focused on minimizing waste and recycling. Initiatives for the sustainable management of foundry sand include reusing reclaimed sand in construction, landscaping, and even in geotechnical applications. Understanding the properties of foundry sand aids manufacturers in making informed decisions about its use and management throughout its lifecycle.
Conclusion
In summary, the properties of foundry sand, including its composition, grain shape and size, strength, thermal stability, moisture control, recyclability, and environmental considerations, are pivotal in determining its effectiveness in casting applications. By comprehensively understanding these properties, foundries can optimize their processes, enhance the quality of cast metals, and contribute to more sustainable manufacturing practices. As industries evolve, the focus on innovative techniques and materials will ensure that foundry sand remains a cornerstone of metal casting operations.
Post time:नोव्हेंबर . 15, 2024 09:59
Next:sand casting process