Materials Used in Sand Casting
Sand casting is one of the oldest and most widely used metal casting processes, characterized by the use of sand as the mold material. This method is favored for its flexibility, cost-effectiveness, and capability to produce complex geometries with intricate details. A successful sand casting process relies heavily on the selection of suitable materials, which can significantly affect the quality and characteristics of the final product. This article delves into the various materials utilized in sand casting.
1. Sand
The primary material in sand casting is, of course, sand. The type of sand used in this process plays a pivotal role in determining the mold's properties. The most common type of sand used is silica sand due to its availability and excellent thermal properties. Silica sand is composed mainly of silicon dioxide (SiO2), which can withstand high temperatures without degrading.
To enhance the properties of silica sand, additives such as clay are often mixed in. Clay serves as a binder, helping the sand grains stick together, which is crucial for maintaining the mold's shape during the pouring of molten metal. Common types of clay used include bentonite, which is known for its strong binding properties. The optimum sand-to-clay ratio can vary based on the specific casting requirements.
2. Binders
In addition to clay, various chemical binders can be employed to improve the mold strength and stability. Organic and inorganic binders are used depending on the desired mold characteristics. For example, resin-bound sand systems utilize synthetic resins that provide superior strength and allow for greater detail in the finished product. This method, although more expensive, is often preferred for complex designs with intricate details.
3. Coatings
materials used in sand casting
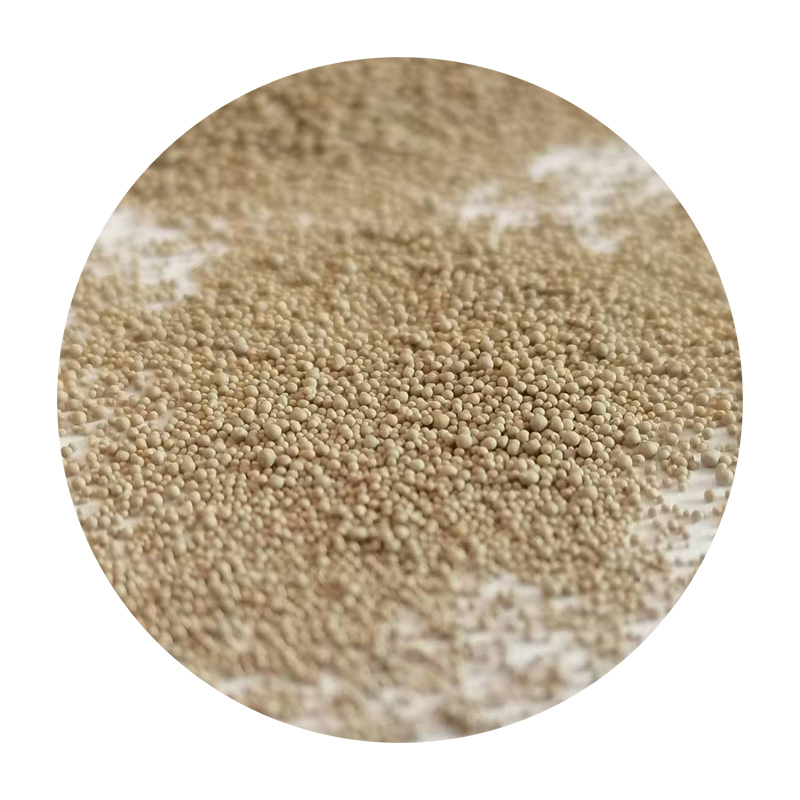
Mold coatings are another critical component in the sand casting process. These coatings serve two main purposes they help to reduce the adhesion of the molten metal to the sand mold and they provide a better surface finish to the cast part. Common coating materials include water-based slurries, which are applied to the inner surface of the mold. These coatings may contain materials like graphite, which reduces friction and improves the heat transfer from the metal to the mold.
4. Metals
The choice of metal to be cast is equally important. Sand casting can accommodate a wide variety of metals, including ferrous and non-ferrous alloys. Commonly cast materials include aluminum, iron, and copper alloys. Each type of metal has specific characteristics that influence the casting process, such as melting point, flow characteristics, and cooling rates. For instance, aluminum alloys are popular due to their lightweight and good corrosion resistance, while cast iron is favored for its wear resistance and excellent machinability.
5. Additives and Impurities
To enhance the properties of the final casting, various additives might be mixed into the molten metal. These can include elements like silicon to improve fluidity, and other alloying elements to achieve desired strength, ductility, or corrosion resistance. However, care must be taken to control impurities, as they can adversely affect the quality of the cast part.
Conclusion
In conclusion, the materials used in sand casting are crucial to the overall success and efficiency of the casting process. From the choice of sand and binders to the selection of metals and coatings, each material plays a significant role in shaping the final product. Understanding the properties and interactions of these materials allows foundries to optimize their processes, yielding high-quality castings that meet stringent industry standards. As technology advances, the exploration of new materials continues to enhance the capabilities of sand casting, making it a relevant and effective method in modern manufacturing.
Post time:ऑक्टोबर . 09, 2024 02:24
Next:Techniques for Enhancing Surface Finish on 3D Printed Objects Through Sanding Methods