Custom Sand Casting A Versatile Manufacturing Process
Custom sand casting is a popular and versatile manufacturing process that involves creating metal castings by pouring molten metal into molds made from sand. This method has been utilized for centuries and remains one of the most effective ways to produce intricate metal parts in various industries, including automotive, aerospace, and art. The flexibility and adaptability of sand casting make it an ideal choice for manufacturers looking to create unique structures tailored to specific applications.
One of the primary advantages of custom sand casting is its ability to produce complex shapes and geometries. Unlike other manufacturing techniques, sand casting allows for greater design freedom, accommodating a wide range of forms, from simple to highly detailed components. With the use of 3D modeling software, engineers can devise intricate designs that would be difficult or impossible to achieve with traditional machining processes. Furthermore, the sand molds can be easily modified to meet the unique specifications of a project, making it an excellent option for custom orders.
The process begins with the creation of a pattern, typically made from materials such as wood, plastic, or metal. This pattern serves as a negative impression for the sand mold. A mixture of sand and a bonding agent is then packed around the pattern to create the mold. Once the mold is formed, it is carefully removed, and the molten metal is poured into the cavity left by the pattern. After the metal solidifies, the sand mold is broken apart to reveal the finished casting.
custom sand casting
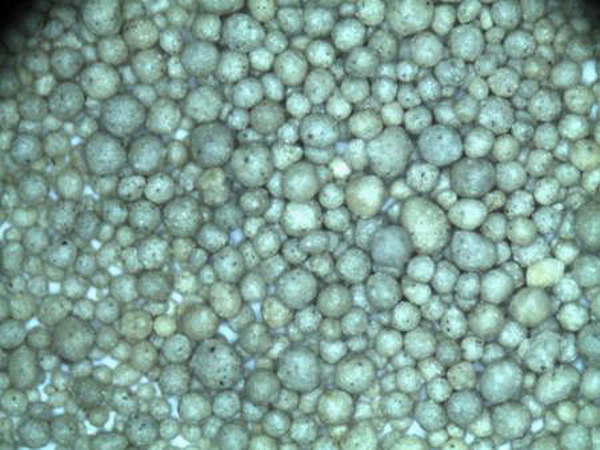
Custom sand casting is particularly advantageous for producing small to medium-sized production runs. For businesses that require unique components for specific applications, this method provides an economical solution. The setup costs associated with sand casting are relatively low compared to other manufacturing processes such as investment casting or die casting, making it feasible for small-scale production. Additionally, the materials used in sand casting are widely available, further reducing costs and making it accessible for various manufacturers.
Moreover, sand casting can accommodate a wide range of metal alloys, including aluminum, bronze, iron, and steel, which enhances its versatility across different applications. Depending on the desired properties of the finished product, manufacturers can select the most suitable alloy to meet the performance requirements. This flexibility in material selection is crucial, especially in industries that demand high-performance components that can withstand extreme conditions.
Another significant benefit of custom sand casting is its minimal environmental impact compared to other casting methods. The sand used in the process is chemically inert and can be reused multiple times, significantly reducing waste. Furthermore, advances in technology and better practices in foundries have led to improved efficiencies and reduced emissions during the casting process.
In conclusion, custom sand casting is an essential method for producing unique metal components tailored to specific needs. Its ability to create complex shapes, cost-effectiveness for small production runs, adaptability to different metal alloys, and reduced environmental impact make it a preferred choice among many industries. As manufacturing continues to evolve, the significance of sand casting in custom applications is likely to persist, proving to be a reliable and efficient method for creating high-quality metal parts. Whether for intricate sculptures or essential mechanical components, custom sand casting remains an indispensable tool in the world of manufacturing.
Post time:डिसेंबर . 13, 2024 00:42
Next:China's Leading Foundry for Quality Sand Casting Solutions and Services