Ceramic Sand Casting A Modern Approach to Metal Casting
Ceramic sand casting is an innovative method in the realm of metal casting, combining traditional techniques with modern material science to produce high-precision and high-quality metal components. This method is particularly useful in manufacturing complex shapes and large parts, serving industries ranging from aerospace to automotive and beyond. The process involves using a ceramic-based sand that allows for enhanced performance characteristics compared to traditional methods.
The Process of Ceramic Sand Casting
The ceramic sand casting process begins with creating a mold. The mold is formed by mixing a fine ceramic sand with a binder to create a model. Ceramic sand has advantageous properties, including high thermal stability and resistance to deformation under heat. Once the mixture is prepared, it is packed around a pattern that represents the final product, ensuring that all details are captured accurately.
After the mold is formed, the pattern is removed, leaving a cavity that will be filled with molten metal. Unlike conventional sand casting, which often uses silica sand, ceramic sand can withstand higher temperatures and offers better dimensional accuracy. This precision is particularly beneficial for industries that demand tight tolerances and complex designs, allowing manufacturers to produce components that meet stringent specifications.
Once the mold is ready, molten metal, often aluminum or iron, is poured into the cavity. The choice of metal depends on the application and the desired properties of the final product. After the metal has cooled and solidified, the mold is broken away to reveal the cast component. This method of casting minimizes defects such as sand inclusions and improves the surface finish of the final product.
Advantages of Ceramic Sand Casting
The primary advantages of ceramic sand casting lie in its ability to produce finer details and improve the overall quality of the castings. One of the remarkable properties of ceramic sand is its ability to resist degradation and maintain its shape even under high-temperature conditions. This leads to fewer defects and rejections, which can significantly reduce production costs and time.
ceramic sand casting
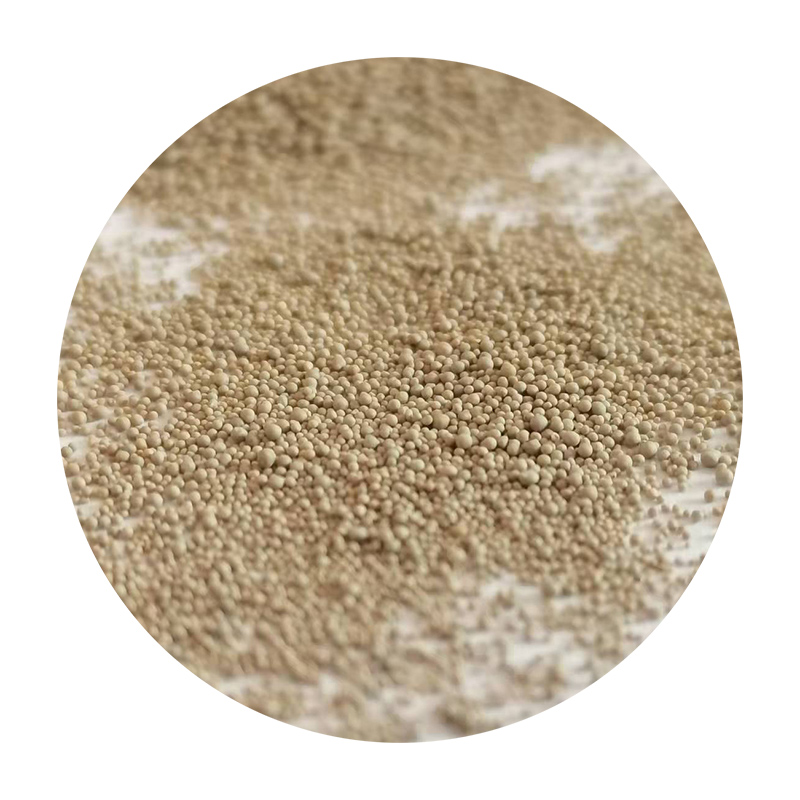
Another important aspect is the ecological footprint of ceramic sand casting. Ceramic materials are more environmentally friendly compared to conventional sand casting processes. Traditional sand casting can produce a considerable amount of waste and often requires extensive cleaning and reclamation processes. In contrast, ceramic sand can be recycled and reused, minimizing waste in the production cycle.
Applications of Ceramic Sand Casting
Ceramic sand casting has found applications in various industries. In the aerospace sector, it is used to produce components that require high thermal resistance and strength-to-weight ratios. Components like turbine blades and engine parts benefit from the precision and performance that ceramic sand molds can provide.
The automotive industry also utilizes ceramic sand casting for producing engine blocks, transmission housings, and other critical components that demand high structural integrity and precise dimensions. In addition, the method is increasingly being adopted in the manufacture of medical devices and equipment, where accuracy and reliability are paramount.
The Future of Ceramic Sand Casting
As technology advances, the ceramic sand casting method continues to evolve. Innovations in binder systems and sand formulations promise further improvements in casting quality and efficiency. Moreover, the integration of computer-aided design (CAD) and computer-aided manufacturing (CAM) technologies is paving the way for even more complex geometries and optimized production processes.
In conclusion, ceramic sand casting represents a significant step forward in the metal casting industry. With its ability to produce high-quality components with exceptional detail, combined with its advantages in terms of waste reduction and environmental impact, it is poised to play a crucial role in the future of manufacturing. As industries continue to push for advancements in precision engineering and sustainable practices, ceramic sand casting is likely to become an increasingly popular choice for manufacturers around the globe.
Post time:ऑक्टोबर . 06, 2024 09:59
Next:sand casting manufacturing process