Exploring 3D Sand Casting A Revolutionary Approach in Metal Manufacturing
In the world of manufacturing, the demand for precision, speed, and flexibility has never been higher. Among the myriad of techniques available, 3D sand casting has emerged as a revolutionary method, transforming traditional practices and enabling manufacturers to meet the complexities of today's industrial needs. This article delves into the innovative process of 3D sand casting, its advantages, and its potential impact on various industries.
What is 3D Sand Casting?
3D sand casting is an advanced casting process that utilizes additive manufacturing technologies to create sand molds for metal casting. Unlike conventional sand casting, where molds are made through manual or semi-automated processes, 3D sand casting employs 3D printers to produce highly intricate and customized molds from sand mixed with a binding agent.
The process begins with a digital model of the part to be cast, which is designed using computer-aided design (CAD) software. This digital model is then sliced into layers that the 3D printer uses to build the mold. The printer deposits the binding agent over the sand in precise patterns, layer by layer, until the mold is formed. Once the mold is complete, molten metal is poured into it, solidifying into the desired shape after cooling.
Advantages of 3D Sand Casting
1. Customization and Complex Geometries One of the primary advantages of 3D sand casting is its ability to produce highly complex and customized designs. Traditional sand casting often requires multiple components or complex tooling, which can be expensive and time-consuming to produce. With 3D sand casting, intricate designs can be printed directly into the mold, significantly reducing lead times and costs.
2. Rapid Prototyping The speed at which molds can be created with 3D sand casting makes it an ideal choice for rapid prototyping. Manufacturers can quickly iterate on designs, test functionality, and refine products without the need for extensive mold modifications. This agility accelerates the product development cycle, allowing companies to bring new products to market faster.
3d sand casting
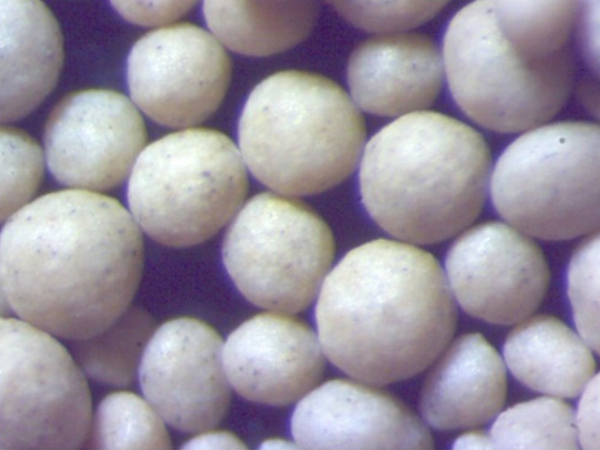
3. Material Efficiency 3D sand casting minimizes waste by using only the amount of sand necessary to create the mold. Traditional methods often result in excess material that must be managed or disposed of, while 3D printing technologies optimize material usage, making the process more environmentally friendly.
4. Reduced Labor Costs Automating the mold-making process significantly reduces the need for manual labor, allowing companies to cut down on labor costs. With fewer workers needed to manage the production, resources can be reallocated to other areas of the business.
5. Enhanced Quality The precision offered by 3D sand casting reduces the likelihood of defects caused by human error during the mold-making process. The digital nature of the design and printing means that each mold can be replicated with high fidelity, ensuring consistent quality in mass production.
Applications in Various Industries
The versatility of 3D sand casting has led to its adoption across a wide range of industries. In the automotive sector, manufacturers use this process to create lightweight engine components with complex geometries that improve performance and fuel efficiency. In the aerospace industry, it allows for the production of intricate components that can withstand extreme conditions.
Additionally, the energy sector benefits from 3D sand casting in the manufacturing of turbine parts, while medical applications take advantage of the technology for producing customized implants and surgical tools tailored to individual patient needs.
Conclusion
As industries continue to evolve, the demand for innovative and efficient manufacturing processes will grow. 3D sand casting stands at the forefront of this transformation, offering an array of advantages that make it a compelling alternative to traditional casting methods. Its ability to produce complex geometries, reduce costs, and enhance quality positions it as a game-changer in the world of metal manufacturing. As technology continues to advance, we can expect to see even more widespread adoption of 3D sand casting in the future, driving new possibilities across various sectors.
Post time:नोव्हेंबर . 11, 2024 07:44
Next:sand casting suppliers