The Evolution of 3D Printed Sanding A New Era in Manufacturing
The advent of additive manufacturing, commonly known as 3D printing, has revolutionized various industries, from aerospace to healthcare. Among the many facets of this transformative technology, 3D printed sanding is emerging as a significant area of exploration. Sanding, traditionally a manual or machine-operated task, is evolving through innovations in 3D printing that enhance efficiency, precision, and the overall quality of finished products. This article delves into the advancements in 3D printed sanding, its applications, and the future implications of this technology.
Understanding 3D Printed Sanding
At its core, 3D printed sanding involves the integration of 3D printing techniques with sanding processes, resulting in custom sanding tools and fixtures that can be tailored to specific tasks. This convergence allows manufacturers to produce sanding blocks, tools, and even entire sanding machines using additive processes. The ability to create complex geometries and bespoke shapes, which would be challenging or impossible with traditional methods, positions 3D printed sanding as a game changer in surface finishing.
Enhancing Precision and Efficiency
One of the primary benefits of 3D printed sanding tools is the potential for increased precision. Traditional sanding tools often lack the necessary ergonomics or shape needed for intricate designs. With 3D printing, manufacturers can create sanding tools that perfectly fit the contours of the workpiece, ensuring an even and consistent finish. This customization not only enhances the quality of the final product but also significantly reduces the time required for manual labor.
Further, the efficiency of production improves as well. Traditional sanding processes can be labor-intensive and slow, requiring multiple passes to achieve the desired finish. However, with 3D printed solutions, manufacturers can quickly produce prototypes and iterate designs based on immediate feedback. This rapid iteration leads to shorter production cycles and faster time-to-market for new products.
Applications Across Industries
The applications of 3D printed sanding span various sectors, notably in woodworking, metalworking, and automotive industries. For instance, in woodworking, custom sanding blocks can be designed to match the intricate details of furniture or cabinetry, resulting in superior surface finishes and reduced waste of materials. In metalworking, 3D printed sanding tools can be utilized for refining complex machined parts, ensuring they meet strict quality standards.
3d printed sanding
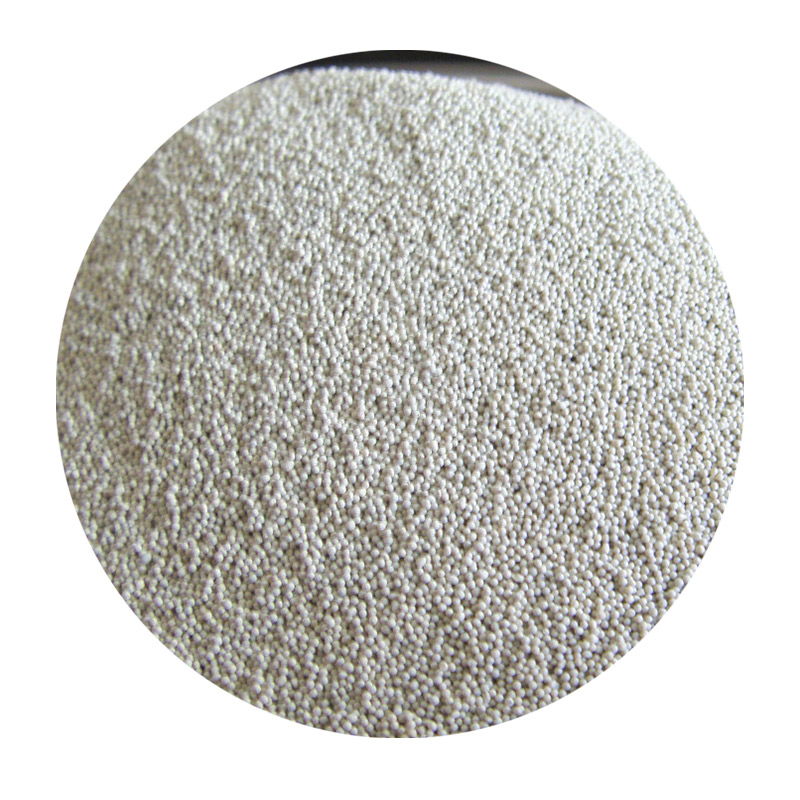
Moreover, the automotive industry is leveraging this technology to create customized sanding solutions for bodywork tailoring. As car designs become more intricate, the need for precise sanding tools increases. 3D printed solutions enable automotive manufacturers to meet these evolving demands with flexibility and speed.
Sustainability Benefits
In addition to improved efficiency and precision, 3D printed sanding presents notable sustainability benefits. Traditional sanding processes often generate significant amounts of waste, whether from excess material being removed or from tools that become obsolete. By employing 3D printing, manufacturers can minimize waste by creating only the tools they need, tailored specifically for each project. Furthermore, the potential to use recycled or bio-based materials in 3D printing makes this approach more environmentally friendly, aligning with the growing demand for sustainable manufacturing practices.
Challenges and Future Directions
Despite its advantages, the integration of 3D printed sanding tools in mainstream manufacturing is not without challenges. Materials used in 3D printing, such as plastics and composites, must possess specific qualities to withstand the mechanical stresses of sanding. Additionally, the initial investment in 3D printing technology can be high, which may deter some small manufacturers from adopting it.
Looking ahead, the future of 3D printed sanding is promising. As material technology advances and the costs of 3D printing decrease, larger segments of the manufacturing industry are likely to adopt this innovation. The development of hybrid systems that combine traditional machining with 3D printing could further enhance the capabilities of sanding processes, driving new levels of precision and efficiency.
Conclusion
The realm of 3D printed sanding is vast and full of potential. By leveraging this innovative technology, manufacturers can enhance precision, efficiency, and sustainability in their sanding processes. As the industry continues to evolve, it is crucial for businesses to remain abreast of these developments to harness the full benefits of 3D printed sanding tools. The future is bright for this intersection of technology and manufacturing, promising transformations that could redefine how we approach surface finishing for years to come.
Post time:ऑक्टोबर . 10, 2024 03:27
Next:application of sand casting process