The Role of Sand in the Casting Process An In-Depth Analysis
When it comes to manufacturing metals and other materials, casting plays a pivotal role in creating complex shapes that would otherwise be challenging to achieve through other methods. One of the critical components of the casting process is sand, which serves as the primary material for making molds. This article explores the significance of sand in casting, its properties, types, and its impact on the overall casting quality.
Understanding the Basics of Sand Casting
Sand casting is one of the oldest and most widely used methods for metal casting. The process involves creating a mold from a mixture of sand and a bonding agent, typically clay, which is then used to shape molten metal. The primary advantage of sand casting is its versatility; molds can be easily shaped to create intricate designs. Moreover, sand is readily available, inexpensive, and relatively easy to work with, making sand casting an attractive option for manufacturers.
Properties of Good Casting Sand
The effectiveness of sand in casting hinges on several essential properties. Firstly, the grain size of the sand is crucial; fine grains can produce smoother surfaces but may lead to poor mold strength, while coarse grains enhance mold strength but can compromise surface finish. Secondly, the shape of the sand particles is significant. Angular particles interlock better, leading to improved compactness and mold strength.
Another critical property is the clay content. Clay acts as a binder, helping to hold the sand grains together when forming the mold. The right balance of clay ensures that the mold can withstand the pressure of the molten metal without collapsing. In addition, the moisture content of the sand is vital. Too much moisture can lead to steam explosions when the molten metal is poured, while insufficient moisture may result in poor mold integrity.
sand in cast
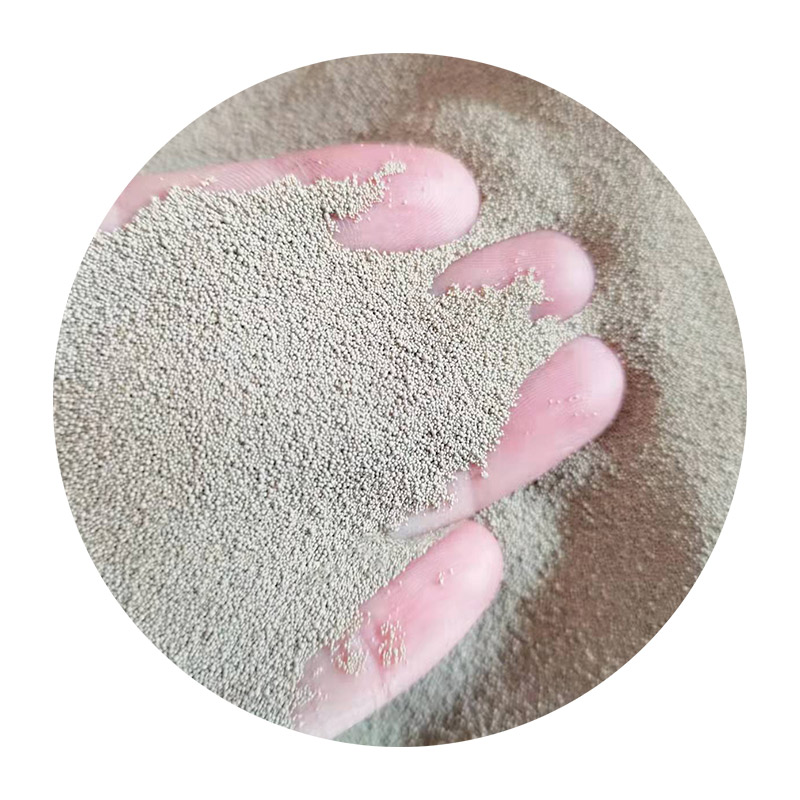
Types of Sand Used in Casting
There are several types of sand used in casting, each with its unique properties. The most common type is silica sand, predominantly composed of silicon dioxide. Silica sand is favored due to its high melting point and availability. However, other types of sand, such as olivine sand, zircon sand, and chromite sand, are also utilized, particularly for specific applications that require higher thermal stability or better surface finishes.
The Impact of Sand Quality on Casting Outcomes
The quality of sand used in the casting process has a direct correlation with the final product's quality. Poor-quality sand can lead to defects in the cast metal, such as sand inclusions, poor surface finish, and dimensional inaccuracies. These defects can result in significant financial losses and compromise the structural integrity of the finished product. Therefore, manufacturers must pay close attention to the choice of sand and perform regular quality checks to ensure that the casting process remains efficient and effective.
Future Trends in Sand Casting
As technology advances, so does the casting process. Recent trends indicate a growing interest in using alternative materials and additives to improve the properties of sand casting. For instance, the incorporation of synthetic sands or the use of 3D printing technology to create molds is gaining traction. These innovations not only enhance the quality of the casting but also reduce the environmental impact associated with traditional sand casting.
In conclusion, sand plays an indispensable role in the casting process, acting as the foundational material for mold creation. Its properties, types, and quality significantly influence the success of the casting operation and the integrity of the final product. As the industry evolves, staying informed about the advancements in sand materials and their application in casting will be essential for manufacturers aiming to maintain competitive standards in metal casting. With careful consideration and innovation, the future of sand casting looks promising, heralding new opportunities and challenges in the manufacturing realm.
Post time:12-р сар . 14, 2024 05:24
Next:spékaný písek