An Overview of Sand Casting and Sand Types
Sand casting is a widely used metal casting process that has been in practice for centuries. It involves creating a mold from sand, into which molten metal is poured to create a variety of products, ranging from automotive components to intricate artistic sculptures. The success of the sand casting process heavily depends on the quality of the sand used, its properties, and the specific requirements of the casting project.
Types of Sand Used in Sand Casting
The primary type of sand used in sand casting is silica sand, which is composed mainly of silicon dioxide (SiO2). This sand is favored for its high melting point, excellent thermal stability, and durability. Silica sand is also readily available and cost-effective, making it a common choice in foundries. However, it must be treated and sometimes mixed with additives to enhance its performance during the casting process.
Another important type of sand used is chromite sand, which is derived from chromium ore. This type of sand offers higher thermal conductivity and lower thermal expansion compared to silica sand, making it ideal for casting high-strength metal alloys. It is particularly useful in applications requiring intricate details and exact tolerances.
Coal sand is another variant used in sand casting, particularly because of its unique properties that help in producing smooth surfaces and reduced casting defects. It is often used for specialized applications, particularly in creating molds that demand a high level of detail.
Characteristics of Molding Sand
sand casting sand
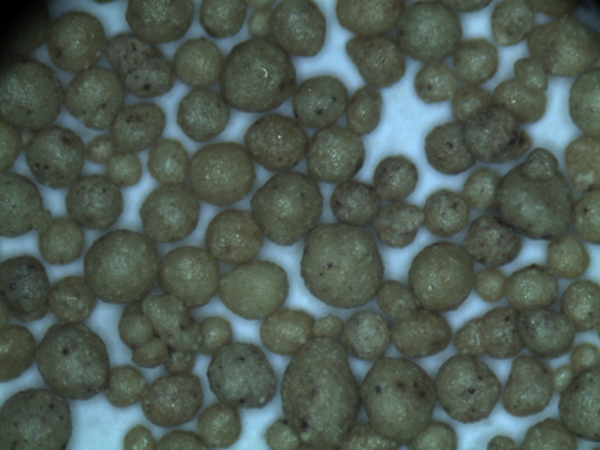
The properties of molding sand play a crucial role in the casting process. Key characteristics include grain size, shape, and distribution. Fine-grained sand can produce smoother surface finishes, while coarser grains provide better strength. The shape of the grains influences the molding sand's ability to retain its structure during the pouring of molten metal.
Another significant property of sand is its moisture content. Proper moisture levels are essential to achieve good mold strength and prevent cracking during the casting process. Foundries often control the moisture content meticulously to ensure optimal performance.
Further, the ability of sand to bind together when mixed with clay or other binding agents is another essential characteristic. Bentonite clay is commonly added to sand to improve its adhesive quality, enabling it to hold complex shapes during the casting process.
The Sand Casting Process
The sand casting process typically begins with the creation of a pattern that resembles the final product. The pattern is then used to form a mold in the sand. Once the mold is prepared, the molten metal is poured into it, filling the cavity left by the pattern. After the metal solidifies, the sand mold is broken away to reveal the finished casting.
Overall, the sand casting process is versatile and economical, capable of producing complex shapes and large quantities of metal parts. The choice of sand is fundamental to the quality of the final product, impacting everything from the strength and detail to the overall finish. As technology evolves, advancements in sand types and compatibility with various alloys will continue to enhance the possibilities within the sand casting industry.
Post time:10 сар . 02, 2024 01:02
Next:Benefits of Sand Casting in Manufacturing Processes and Its Popularity