Sand Casting Procedure A Step-by-Step Guide
Sand casting is a widely used metal casting process, where molten metal is poured into a mold made from sand. This technique is favored for its versatility and cost-effectiveness, making it suitable for both small-scale and large-scale production. In this article, we will outline the key steps involved in the sand casting process.
Step 1 Pattern Making
The first step in the sand casting process is creating a pattern, which is a replica of the final product. Patterns can be made from various materials, including wood, metal, or plastic, depending on the complexity of the design and the material to be cast. It is crucial that the pattern accounts for shrinkage that will occur as the metal cools. The pattern is typically slightly larger than the desired finished part, and it is designed to be easily removed from the sand mold.
Step 2 Preparing the Mold
Once the pattern is ready, the next step is to create the mold. This involves packing sand around the pattern to form a hollow cavity. The sand used is usually a mixture of silica sand, clay, and water, which gives it the necessary binding properties. The mold can be created in two halves the cope (top half) and the drag (bottom half). After packing the sand, the pattern is carefully removed, leaving a perfectly shaped cavity in which the molten metal will be poured.
Step 3 Pouring the Metal
sand casting procedure
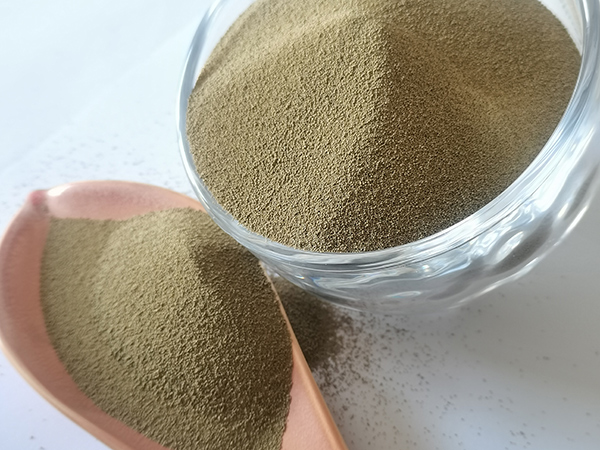
With the mold ready, it is time to pour the molten metal into the cavity. Before pouring, the metal must be melted and heated to a specific temperature, depending on the type of metal being used, such as aluminum, iron, or bronze. The pouring process must be performed carefully to avoid defects such as turbulence, which can lead to inclusions or air pockets within the final casting. Pouring should be done steadily and continuously until the mold is completely filled.
Step 4 Cooling and Solidification
After the metal is poured, it is left to cool and solidify within the mold. The cooling time will vary based on the size of the casting and the type of metal used. It is important to allow sufficient time for the metal to solidify completely to maintain dimensional accuracy and structural integrity.
Step 5 Finishing Touches
Once the metal has cooled, the mold is broken apart to retrieve the casting. The final step involves cleaning the casting to remove any sand or impurities. Additional finishing processes may include machining, grinding, or painting to achieve the desired surface finish and dimensions.
Conclusion
Sand casting is a fundamental and efficient method for producing complex metal parts. By following these steps—pattern making, mold preparation, metal pouring, cooling, and finishing—manufacturers can produce high-quality castings tailored to meet specific engineering requirements.
Post time:10 сар . 04, 2024 09:42
Next:Sanding-Techniken für eine verbesserte Oberflächenqualität beim 3D-Druck