Sand Casting Foundry Process An Overview
Sand casting is one of the oldest and most widely utilized manufacturing processes for creating metal parts and components. This method offers a versatile solution for producing both large and small quantities of castings. The process involves several key steps and utilizes sand as the primary mold material. In this article, we will explore the fundamental aspects of the sand casting process, its advantages, applications, and considerations for quality.
The Sand Casting Process
The sand casting process begins with the creation of a pattern, which is a replica of the final product. Patterns can be made from various materials such as wood, metal, or plastic. The design of the pattern is critical since it must accommodate for shrinkage that occurs when the metal cools and solidifies. Once the pattern is prepared, the next step involves creating a mold.
1. Mold Preparation The mold for sand casting is created by packing sand around the pattern in a molding box. The sand used in this process is typically a mixture of sand, clay, and water, which provides the necessary binding strength. The pattern is removed after the sand has been compacted, leaving behind a cavity shaped like the desired casting. This process can be performed in two halves—known as the cope and drag—allowing for a more complex and detailed mold.
2. Pouring the Metal Once the mold is prepared, metal in a liquid state is poured into the cavity. The choice of metal depends on the required properties of the end product and can include alloys like aluminum, iron, or brass. The pouring process should be controlled to minimize turbulence, which can lead to defects, such as porosity or inclusions.
3. Cooling and Solidification After the metal is poured, it begins to cool and solidify, taking the shape of the mold. The cooling time depends on the type of metal used and the thickness of the casting. During this phase, care must be taken to ensure consistent cooling to avoid warping or cracking of the casting.
4. Mold Removal Once the metal has solidified, the sand mold is broken apart to reveal the casting. This is typically done through mechanical shaking or vibration to facilitate the removal of the sand. The casting is then inspected for any defects and may undergo further processing, such as trimming excess material, machining, or surface finishing.
Advantages of Sand Casting
Sand casting is favored in many industries due to its numerous benefits
sand casting foundry process
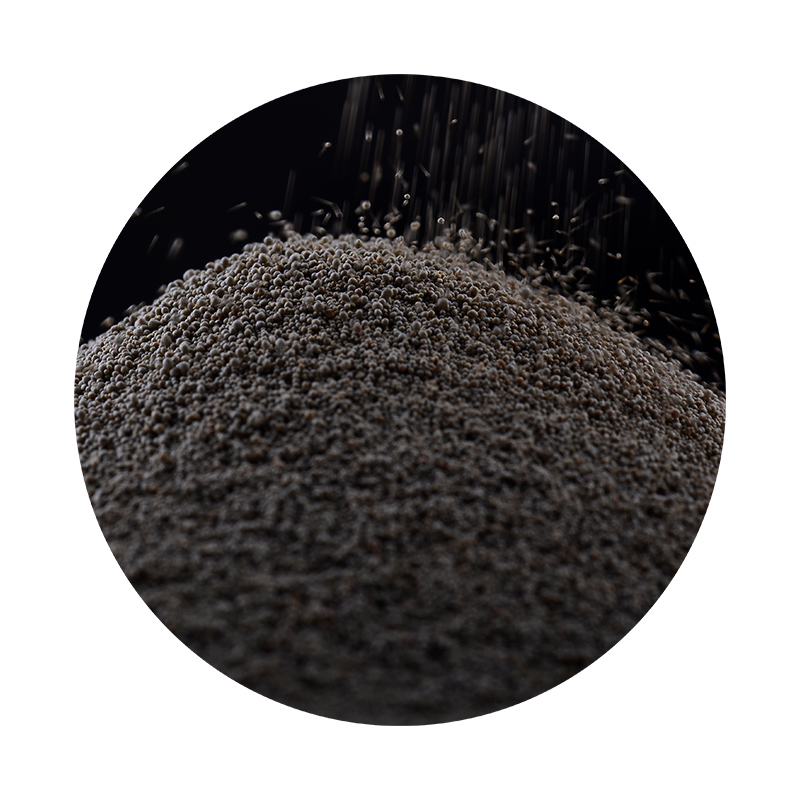
- Flexibility The process allows for intricate designs and various sizes of castings, making it suitable for a wide range of applications—from automotive components to artistic sculptures. - Cost-Effectiveness The materials required for sand casting are relatively inexpensive, and it is economical for both small and large production runs compared to other casting methods.
- Compatibility Sand casting can be used with a variety of metals and alloys, providing flexibility in material selection based on the desired properties of the finished product
.- Ease of Modification Changes can be made to patterns and molds relatively easily, enabling rapid prototyping and adjustments in design.
Applications of Sand Casting
The versatility of sand casting makes it suitable for various industries, including automotive, aerospace, and construction. Common applications include engine blocks, valve bodies, gear housings, and decorative items. Furthermore, sand casting is also employed in the manufacturing of heavy machinery parts, where durability and strength are paramount.
Quality Considerations
While sand casting offers many advantages, attention to detail during the process is essential for ensuring high-quality castings. Factors such as mold design, sand composition, pouring temperature, and cooling rates can significantly impact the final product. Implementing strict quality control measures, including inspections and testing, is crucial for identifying and mitigating potential defects early in the production process.
Conclusion
The sand casting foundry process stands out as an efficient and versatile manufacturing method that plays a vital role in producing metal components across various sectors. By understanding the intricacies of the process, manufacturers can harness its benefits to create high-quality, reliable castings that meet the demands of ever-evolving industries.
Post time:12-р сар . 01, 2024 23:36
Next:Understanding the Density Characteristics of Foundry Sand for Optimal Casting Performance