The Resin Coated Sand Process Revolutionizing Foundry Practices
The resin coated sand process has emerged as a pivotal technology in the foundry industry, enabling manufacturers to produce high-quality castings with improved precision and surface finish. This innovative method involves the application of a phenolic resin coating to sand grains, creating a sophisticated molding material that significantly enhances the casting process.
Process Overview
The resin coating process begins with the selection of high-quality silica sand, which serves as the base material. This sand is then mixed with a liquid resin, typically a phenolic resin, that is heated and subsequently coated onto the sand grains. The heating process allows the resin to bond firmly to the sand surfaces, creating a robust and thermosetting material that can withstand the high temperatures encountered during metal casting.
Once the sand has been coated, it is generally cured through a process known as catalytic curing, involving the addition of a hardening agent or catalyst. This curing step is crucial as it solidifies the coating, giving the sand its unique properties of strength and flexibility. The result is a sand that retains its shape under high temperatures, enabling it to be packed tightly in molds and providing excellent dimensional accuracy.
Advantages of Resin Coated Sand
One of the primary advantages of resin coated sand is its ability to produce intricate and precise casting shapes that would be challenging to achieve with traditional sand casting methods. The superior flexibility and strength of the coated sand allow for the creation of thin-walled sections and complex geometries without the risk of casting defects such as sand erosion or mold collapse. This characteristic is particularly advantageous in industries that demand high precision, such as automotive and aerospace manufacturing.
resin coated sand process
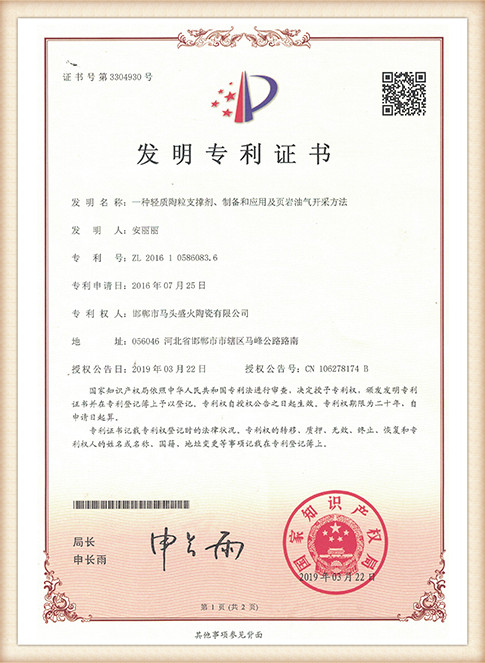
Additionally, resin coated sand exhibits superior surface finish characteristics. This is largely due to the smoothness of the coated sand grains, which results in a diminished roughness on the casting surface. A finer finish reduces the need for extensive post-casting treatments, thereby saving time and production costs. This not only enhances the aesthetic quality of the castings but also improves their mechanical properties, making them more durable and reliable for critical applications.
Environmental Considerations
In recent years, there has been growing concern regarding the environmental impact of foundry operations. The resin coated sand process offers several eco-friendly advantages. The amount of waste generated during casting is minimized, as the reclaimed sand can often be reused multiple times without significant degradation in quality. This reusability promotes sustainability within the industry.
Moreover, advancements in resin formulations have led to the development of more environmentally friendly options that emit fewer volatile organic compounds (VOCs) during the curing process. Such innovations not only comply with stringent environmental regulations but also improve working conditions for foundry employees.
Conclusion
In summary, the resin coated sand process stands at the forefront of modern casting technologies, offering unparalleled advantages in precision, surface finish, and environmental sustainability. As industries continue to demand higher efficiencies and product quality, the adoption of resin coated sand in foundries will likely expand, encouraging further research and development in this field. As manufacturers seek innovative ways to improve their processes and meet customer expectations, the resin coated sand process represents a significant step forward, blending traditional methods with cutting-edge technology to create a more efficient and eco-friendly future in metal casting. By embracing these advancements, the foundry industry can ensure its competitiveness in a rapidly evolving marketplace while contributing to a more sustainable environment.
Post time:12-р сар . 07, 2024 15:10
Next:sanding 3d printed objects