Lost Foam Casting Coating An Innovative Approach to Precision Casting
Lost foam casting is a modern method of metal casting that has gained significant attention due to its ability to produce complex geometries with high precision and minimal machining. One of the critical aspects of this process is the coating used to enhance the properties of the foam pattern before pouring the metal. This article will explore the significance of lost foam casting coating, its composition, application, advantages, and challenges.
Understanding Lost Foam Casting
Lost foam casting (LFC) involves creating a pattern from expanded polystyrene (EPS) foam, which is coated with a refractory material. The foam pattern is then placed in a mold, and molten metal is poured over it. The foam evaporates due to the heat of the molten metal, leaving a void that perfectly replicates the foam's shape. This method is widely used in various industries, including automotive, aerospace, and art, due to its efficiency and versatility.
The Role of Coating in LFC
Coating the foam pattern is a crucial step in the lost foam casting process. The primary functions of the coating are to provide strength and integrity to the foam pattern, to protect it from molten metal, and to facilitate the smooth flow of metal into the mold cavity. The coating is typically made of a mixture of sand and a binder, which forms a robust shell around the foam pattern.
Composition of the Coating
The lost foam casting coating usually consists of fine sand (often silica) mixed with a binding agent, such as sodium silicate or other chemical binders. The choice of binder affects the thermal stability and strength of the coating. In addition to sand and binder, coatings may also include additives to improve properties such as adhesion, thermal shock resistance, and surface finish. The goal is to create a coating that will withstand the high temperatures of the molten metal while providing excellent detail replication.
Application of Coating
Coating the foam pattern typically involves a dipping or spraying technique. The foam pattern is first cleaned to remove any contaminants before applying the coating. The coated pattern is then dried at ambient temperature or in a controlled environment to ensure the coating adheres properly. Proper application is crucial as it influences the final casting quality. Uneven or insufficient coating can lead to mold breakage or defects in the cast product.
Advantages of Using Coatings
lost foam casting coating
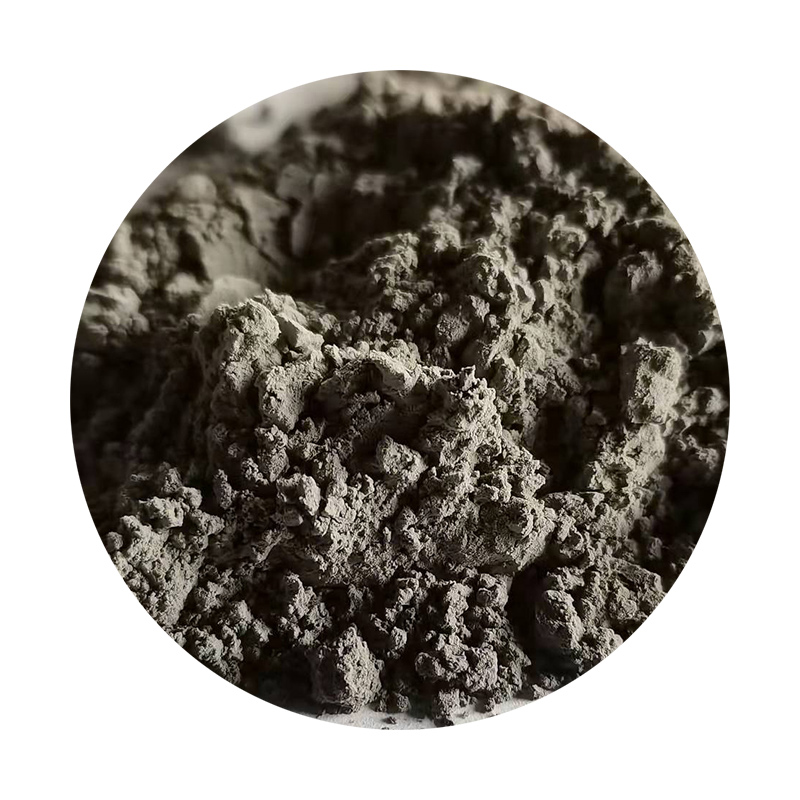
The use of coatings in lost foam casting offers several advantages
1. Enhanced Detail and Surface Finish Coatings improve the surface finish of the final product by minimizing defects and enhancing precision.
2. Improved Strength The coating adds strength to the foam pattern, enabling it to withstand the pressure of the molten metal.
3. Better Thermal Stability A well-formulated coating can resist thermal shock, reducing the risk of failure during the metal pouring process.
4. Reduced Waste The precision of lost foam casting and the use of coatings can lead to significant waste reduction compared to traditional casting methods.
5. Versatility The coating can be tailored for different applications, making lost foam casting suitable for a wide range of industries.
Challenges and Considerations
Despite the advantages, there are challenges in using coatings for lost foam casting. Developing a coating that balances strength, thermal resistance, and fluidity can be complex. Additionally, environmental concerns regarding the use of certain binders and chemicals necessitate the development of more eco-friendly alternatives. Manufacturers must also invest in proper training and equipment to ensure the coating process is executed correctly.
Conclusion
Lost foam casting coating plays a vital role in enhancing the effectiveness and efficiency of the casting process. As industries continue to seek precision and sustainability in their manufacturing methods, the development of innovative coatings and techniques will likely evolve, making lost foam casting an ever more attractive option for producing complex metal parts. By understanding and addressing both the benefits and challenges associated with coatings, manufacturers can significantly improve the quality and viability of their cast products.
Post time:11-р сар . 09, 2024 07:21
Next:Golden Shores Enterprises Innovative Solutions for a Bright Future