Lost Foam Casting Coating An Overview
Lost foam casting is an innovative metal casting process that offers remarkable advantages in terms of precision, surface finish, and cost savings. One critical aspect of this process is the coating used on the foam patterns before they are filled with molten metal. In this article, we will explore the significance of lost foam casting coatings, their composition, application, and impact on the overall casting process.
The lost foam casting method involves creating a foam pattern, typically made from polystyrene or similar materials. This pattern is coated in a special material and then placed in a sand mold. When molten metal is poured into the mold, the heat vaporizes the foam, allowing the metal to take its shape. This process eliminates the need for core boxes and allows for complex geometries and intricate designs, which are more challenging to achieve with traditional casting methods.
The coating applied to the foam pattern plays a pivotal role in the success of the lost foam casting process. One of the primary functions of this coating is to provide a barrier between the foam and the molten metal, which helps to prevent the molten metal from deforming or dissolving the foam pattern. Additionally, the coating helps form a shell, which influences the final surface finish of the cast product. Although the lost foam casting process typically results in an excellent surface finish, the right coating can significantly enhance this aspect, leading to even greater precision and fewer post-processing steps.
Lost foam casting coatings are usually made from a mixture of silica sand and a bonding agent, often a colloidal silica or an inorganic binder. This mixture creates a hard shell around the foam pattern that can withstand the intense heat of molten metal. While selecting the right coating materials, foundries consider factors such as thermal conductivity, strength, and compatibility with the specific metal being cast. Some coatings are also enhanced with additives to improve performance; for instance, refractory materials can be included to withstand higher temperatures and reduce thermal expansion.
lost foam casting coating
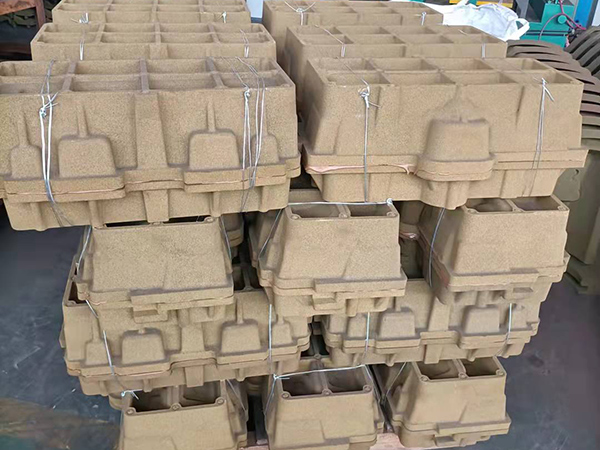
The application of the coating typically involves a dipping, brushing, or spraying process. Each method has its nuances, and the choice depends on factors such as the complexity of the pattern and production volume. The coated foam pattern is then dried to ensure a solid bond between the coating and the foam before it is placed in the mold. This drying step is crucial, as any moisture left can lead to defects such as gas porosity or even explosions during casting.
One of the main advantages of using lost foam casting coatings is the reduction of material waste. As the foam is completely vaporized during the casting process, there are no remnants of the pattern left behind. Furthermore, the coatings can lead to faster production cycles due to reduced machining requirements, which translates into cost savings for manufacturers.
However, it is essential to meticulously monitor the properties of the coating and ensure that optimal application techniques are employed. Quality control in the coating process, from material selection to application techniques, can significantly impact the end product's quality.
In conclusion, lost foam casting coatings are a fundamental component of the lost foam casting process, enabling the production of high-quality metal parts with intricate designs. By providing a barrier to protect the foam pattern and enhancing the surface finish, these coatings contribute significantly to the overall efficiency and effectiveness of the casting process. Understanding the different aspects of coating selection and application is vital for foundries aiming to maximize the benefits of lost foam casting in their operations.
Post time:11-р сар . 07, 2024 13:51
Next:Steel Sand Casting Techniques and Applications for Optimal Manufacturing Efficiency