The Importance of Sand Casting A Versatile Manufacturing Process
Sand casting, one of the oldest and most widely used metal casting processes, has played a pivotal role in various industries for centuries. Despite the evolution of advanced technologies in manufacturing, sand casting continues to be a popular choice for many engineers and designers due to its unique advantages. Understanding the importance of sand casting involves exploring its processes, benefits, applications, and the trends shaping its future.
The Sand Casting Process
The sand casting process involves several key steps, beginning with the creation of a mold. The first step is to form a pattern, typically made of metal, plastic, or wood, that replicates the desired end product. This pattern is then surrounded by a mixture of sand and binder (usually clay) to form a mold. Once the mold is ready, the pattern is removed, creating a hollow cavity in the sand that matches the shape of the desired component.
Next, molten metal is poured into the mold. The heat from the molten metal causes the sand to harden, forming a strong, durable shell that holds the shape of the intended object. After the metal has cooled and solidified, the sand mold is broken away, revealing the finished casting. This process allows for intricate designs and complex shapes, making sand casting an attractive option for various applications.
Advantages of Sand Casting
One of the primary reasons for the sustained popularity of sand casting is its versatility. Sand casting can accommodate a wide array of materials, including aluminum, iron, steel, bronze, and other alloys. This adaptability enables manufacturers to produce a diverse range of products, from automotive components to intricate sculptures.
Another significant advantage is cost-effectiveness. Sand casting is an economical method for producing both small and large quantities of parts, making it suitable for everything from one-off prototypes to mass production. The materials used in sand casting, primarily sand, are relatively inexpensive and readily available.
The sand casting process also allows for excellent dimensional accuracy, especially when dealing with large parts. It can effectively produce complex geometries without the need for extensive machining, saving time and reducing production costs. Furthermore, the process can be easily scaled to accommodate various production needs, from small workshops to large industrial facilities.
importance of sand casting
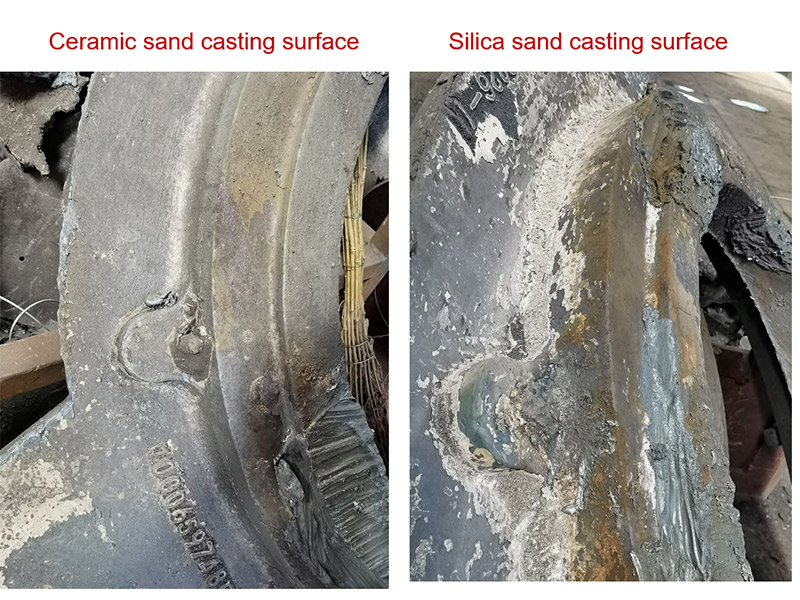
Applications of Sand Casting
Sand casting is prevalent in numerous industries due to its flexibility and efficiency. In the automotive sector, it is commonly used to produce engine blocks, transmission cases, and other crucial components that require high strength and durability. The aerospace industry also employs sand casting for parts that can withstand harsh operating conditions, such as brackets and housings.
Moreover, the construction industry benefits from sand casting through the production of intricate architectural elements, such as decorative facades and unique fixtures. The energy sector, particularly in the manufacturing of wind turbines and other renewable energy components, also relies on sand casting to create robust and efficient parts.
Trends Shaping the Future of Sand Casting
Despite the rise of new manufacturing techniques such as 3D printing and die casting, sand casting remains competitive due to ongoing innovations in the field. Advancements in technology, including the integration of computer-aided design (CAD) and simulation software, are enhancing the design and production processes. These tools allow engineers to optimize mold designs, improve accuracy, and reduce waste, leading to more sustainable manufacturing practices.
Additionally, there is a growing focus on environmentally friendly sand casting methods. The use of green sand, which is made from natural clay and silica without harmful additives, is becoming increasingly popular. This shift not only minimizes the environmental impact of the casting process but also aligns with global trends towards sustainability.
Conclusion
In conclusion, the importance of sand casting lies in its unique advantages, wide-ranging applications, and adaptability in various industries. As technology advances and environmental concerns grow, the sand casting process continues to evolve, allowing manufacturers to optimize production while maintaining cost-effectiveness and quality. Its legacy as a timeless manufacturing method remains, proving that despite the changes in technology, sand casting will likely remain a cornerstone of metal casting for years to come.
Post time:11-р сар . 08, 2024 06:32
Next:A Guide to Sanding Resin for Smooth Finishes and Professional Results