Understanding Foundry Sand Types
Foundry sand plays a critical role in the metal casting industry, serving as a crucial component in the formation of molds and cores. The type of sand used can significantly influence the quality of the final cast product, affecting factors such as strength, surface finish, and dimensional accuracy. This article will explore various types of foundry sands, their properties, and applications to provide a comprehensive understanding of this essential material.
Types of Foundry Sand
1. Silica Sand Silica sand, composed primarily of silicon dioxide (SiO2), is the most commonly used foundry sand due to its excellent casting properties. It has a high melting point, good thermal stability, and is readily available. Silica sand is beneficial for both green sand casting and resin-coated sand processes. However, it can be abrasive and may require careful handling during preparation.
2. Chromite Sand Chromite sand, derived from chromite ore, is known for its high thermal stability and low thermal expansion. This type of sand is particularly valuable for casting high-temperature alloys. It provides excellent resistance to metal penetration and is often used in the production of molds for casting ferrous metals and iron. It is also used in applications that require superior surface finish and dimensional accuracy.
3. Zircon Sand Zircon sand is another type of foundry sand that possesses exceptional thermal resistance and low thermal expansion properties. It is often used for casting high melting point metals such as titanium and nickel-based alloys. Additionally, zircon sand contributes to a smooth surface finish and can be reused multiple times, making it a sustainable option for foundry applications.
4. Olive Sand Olive sand is an innovative synthetic sand made from a mixture of different minerals, providing unique advantages over traditional sands. Known for its excellent flowability and strength, olive sand is often used for high-precision castings in automotive and aerospace industries. Its unique composition allows for easy mold release and reduces the risk of defects in the final product.
foundry sand types
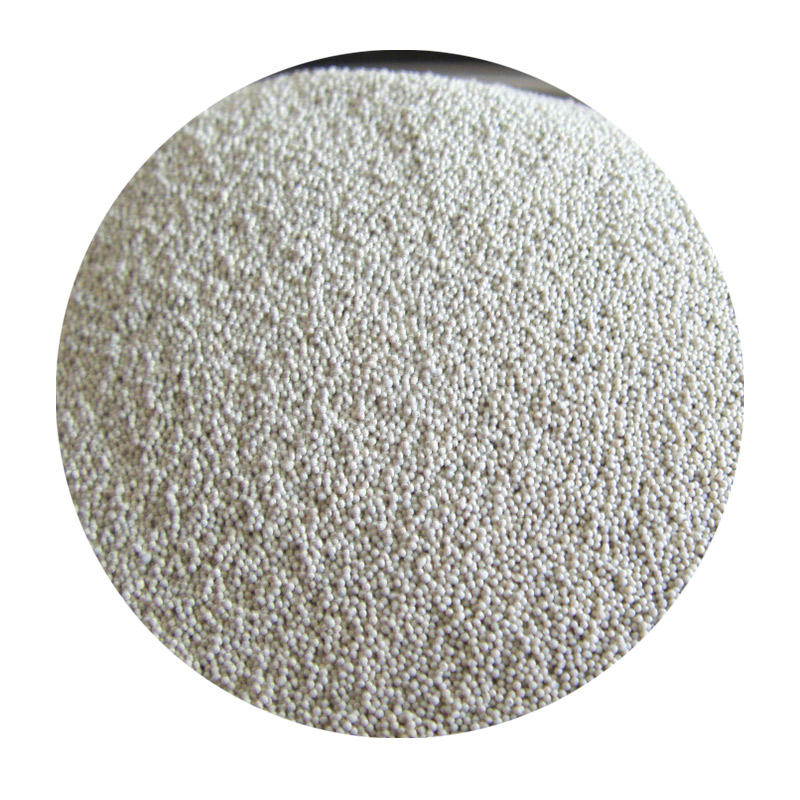
5. Investment Casting Sands Investment casting involves creating a mold by building a shell around a wax pattern. The investment casting sand used is typically fine-grained for superior detail and surface finish. Common materials for investment casting sand include fine silica sand or specially formulated synthetic materials that provide the required rigidity and thermal resistance during the casting process.
Comparison of Foundry Sand Types
While the choice of foundry sand can depend on specific project requirements, it is essential to consider factors such as grain size, shape, and thermal properties. For instance, silica sand is often favored for its availability and cost-effectiveness, but in high-performance applications, chromite or zircon sand may be preferred due to their superior thermal stability.
Environmental Considerations
As the foundry industry faces increasing pressure to adopt sustainable practices, the selection of foundry sand types has also evolved. Some manufacturers have started using recycled sands and synthetic materials that reduce environmental impact. Additionally, innovations like green sand, which uses naturally occurring bentonite clay as a binder, have gained popularity for their eco-friendliness.
Conclusion
The type of foundry sand selected can have a profound impact on the casting process and the quality of the final product. Understanding the properties and applications of various sand types, such as silica, chromite, zircon, and investment casting sands, allows foundries to make informed decisions tailored to their specific needs. As the industry continues to innovate towards sustainability, the exploration of new materials and methods will undoubtedly shape the future of foundry sand usage. Ultimately, the right choice of foundry sand not only enhances casting outcomes but also contributes to a more sustainable and responsible manufacturing process. By keeping abreast of advancements in sand technology and environmental practices, foundries can remain competitive in an ever-evolving landscape.
Post time:10 сар . 14, 2024 06:14
Next:Sustainable Solutions for Recycling Foundry Sand in Modern Industries