Foundry Sand An Essential Material in Metal Casting
Foundry sand is an indispensable component in the metal casting industry. It plays a crucial role in shaping various metal products, from everyday items to sophisticated machinery components. Comprised primarily of silica, foundry sand possesses unique characteristics that make it ideal for the casting process, such as high melting points, excellent thermal stability, and the ability to withstand high temperatures. This article will explore the properties, applications, and environmental considerations of foundry sand.
Properties of Foundry Sand
The primary component of foundry sand is silica (SiO2), often derived from quartz. This natural mineral provides the sand with its signature properties, such as grain size, sphericity, and durability. Foundry sands are commonly classified into two categories silica sand and synthetic sand. Silica sand is naturally occurring and is used in various casting processes due to its remarkable mold-making properties.
One of the key characteristics of foundry sand is its ability to form a stable mold. When mixed with binding agents such as clay or resin, foundry sand can hold its shape well, allowing for intricate mold designs with fine details. Additionally, foundry sand exhibits excellent permeability, allowing gases produced during the melting and pouring of metal to escape, thus preventing defects in the final product.
The thermal properties of foundry sand are equally significant. It can withstand high temperatures, making it suitable for use in the casting of ferrous and non-ferrous metals. The high thermal conductivity of silica sand ensures that heat is evenly distributed throughout the mold, reducing the risk of thermal shock and ensuring a consistent final product.
Applications of Foundry Sand
Foundry sand is widely used in various sectors of the metal casting industry. Its primary application is in the production of metal components through sand casting, a technique that involves pouring molten metal into sand molds. This method is favored for its cost-effectiveness and flexibility, making it suitable for producing small to medium-sized batches of components.
foundry sand
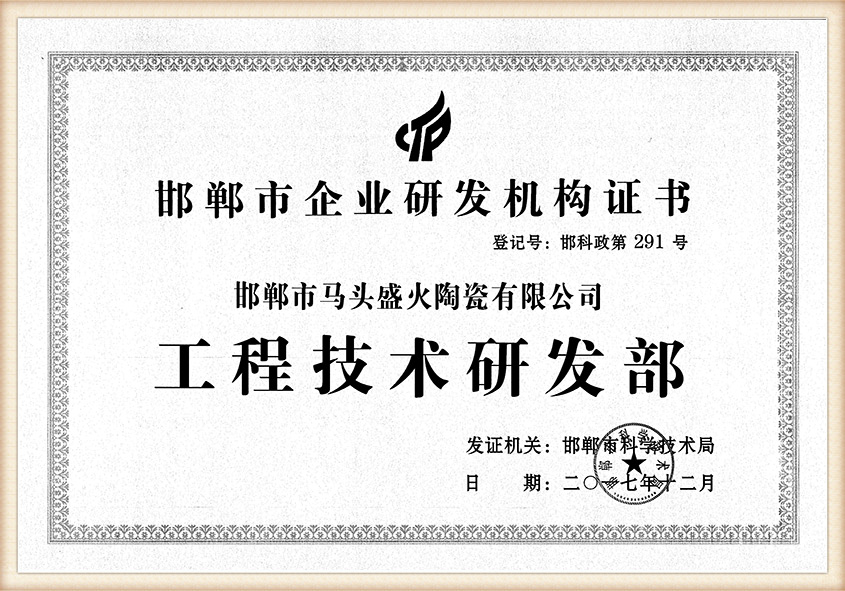
In addition to traditional sand casting, foundry sand is also used in investment casting and shell mold casting processes
. Investment casting, or lost-wax casting, uses a wax pattern coated with a layer of sand to create detailed molds, while shell mold casting utilizes a thin shell of sand to enhance mold strength and accuracy.Industries such as automotive, aerospace, and construction rely heavily on foundry sand for producing engine blocks, transmission housings, and various structural components. The durability and precision of sand-cast products make them ideal for high-stress applications, ensuring that they meet stringent industry standards.
Environmental Considerations
While foundry sand is essential for metal casting, environmental impacts must also be taken into account. The extraction of silica sand can lead to habitat disruption and ecological imbalance. Additionally, the disposal of used foundry sand presents challenges, as it can contain contaminants from the casting process.
To mitigate these issues, many foundries are now exploring recycling options. Used foundry sand can be reused in various construction applications, such as making concrete, road base, or as a soil amendment. Recycling helps reduce waste and minimize environmental impact while also providing cost savings for the industry.
Moreover, several regulations govern the use of foundry sand and its disposal. The industry is increasingly adopting sustainable practices, including the use of eco-friendly binding agents and exploring new materials to replace traditional foundry sands.
Conclusion
In summary, foundry sand is a vital material in the metal casting industry, characterized by its unique properties that enable the production of high-quality, durable metal components. With its extensive applications and integral role in various industries, foundry sand remains a cornerstone of modern manufacturing. However, as concerns about environmental sustainability rise, it is crucial for the foundry industry to embrace recycling initiatives and sustainable practices to ensure the long-term viability of this essential material. By doing so, the industry can continue to innovate while minimizing its ecological footprint, paving the way for a more sustainable future in metal casting.
Post time:12-р сар . 13, 2024 08:48
Next:Understanding the Composition and Properties of Sand Cast Iron in Metalworking Applications