Applications of Sand Casting Process
Sand casting is one of the oldest and most versatile metal casting processes. This technique has been used for centuries across various industries to create a wide range of components, from intricate designs to large structural parts. Its adaptability to different materials and scalability makes it a popular choice for many applications. In this article, we will explore the key applications of the sand casting process and its numerous benefits.
One of the primary applications of sand casting is in the automotive industry. This sector heavily relies on sand casting for producing engine blocks, cylinder heads, and other critical components. The process allows manufacturers to create complex shapes that meet precise engineering specifications, which is vital for vehicle performance and safety. Furthermore, sand casting can accommodate various metals, including aluminum, iron, and magnesium alloys, making it suitable for lightweight components that improve fuel efficiency.
Applications of Sand Casting Process
In addition to automotive and aerospace, sand casting is widely used in the construction industry. The process allows for the efficient manufacturing of various structural components, such as beams, supports, and decorative elements. Sand casting enables the production of intricate designs that can enhance the aesthetic appeal of buildings and infrastructure while maintaining structural integrity. The versatility of sand casting also allows it to be adapted for different materials and project requirements, making it an essential technique in construction.
applications of sand casting process
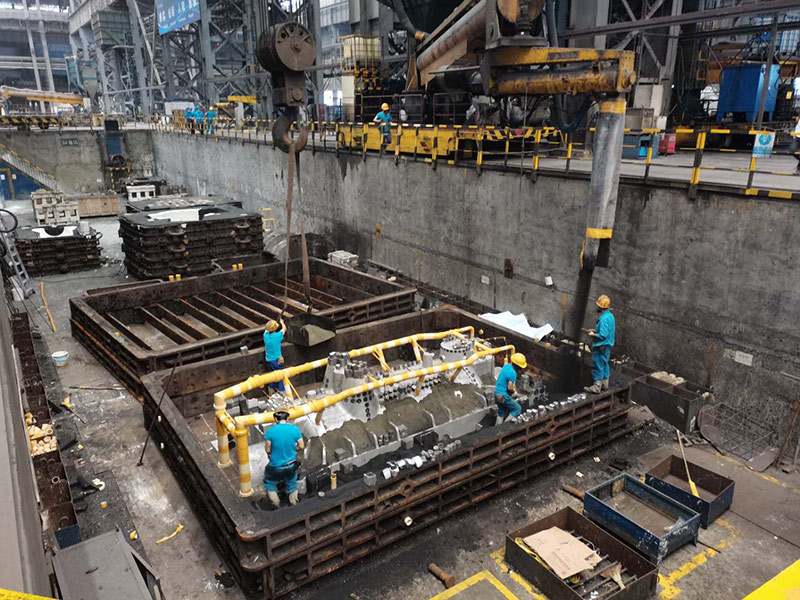
Moreover, sand casting finds applications in the energy sector, particularly in the manufacturing of components for power generation equipment. Items such as turbine blades, casings, and valve bodies are often produced using sand casting. The ability to create large, durable parts that can withstand high temperatures and pressures is essential in this industry. Sand casting also supports the production of castings that require excellent thermal conductivity, which is important for heat exchangers and other related components.
Additionally, sand casting is increasingly being utilized in the art and sculpture field. Artists and sculptors leverage the process to create unique pieces and large installations. The ability to mold sand into intricate shapes enables creativity and freedom in design. Furthermore, the relatively low cost of sand casting makes it accessible for artists seeking to produce limited editions or one-off pieces.
The benefits of sand casting go beyond its applications. This process is cost-effective, particularly for low to medium production volumes. The raw materials required—sand, clay, and water—are abundant and inexpensive. Additionally, the process is highly flexible, allowing for quick adjustments to mold designs and parameters. This adaptability makes sand casting suitable for prototypes and custom projects where design changes may be frequent.
In conclusion, the applications of the sand casting process are vast and varied. From automotive and aerospace components to construction elements and artistic creations, sand casting continues to be a fundamental technique in the manufacturing sector. Its combination of cost-effectiveness, versatility, and the ability to produce complex geometries makes it an invaluable tool across industries. As technology advances, the sand casting process is likely to evolve further, opening new doors for innovation and creativity.
Post time:12-р сар . 14, 2024 05:45
Next:Advancements in Sand Casting Techniques for Enhanced Manufacturing Efficiency and Precision