Advantages and Disadvantages of Sand Casting
Sand casting is one of the oldest and most widely used metal casting processes. It involves creating a mold from sand to shape molten metal, which is then poured into the mold to solidify and form the desired object. While sand casting has numerous advantages, it also comes with its own set of disadvantages that must be considered when deciding whether it is the appropriate method for a specific project.
Advantages of Sand Casting
1. Cost-Effectiveness One of the primary advantages of sand casting is its low cost. The materials used in the process, primarily sand and some binders, are inexpensive and readily available. Additionally, the equipment needed for sand casting is relatively simple and can often be produced in-house or with minimal investment.
2. Versatility Sand casting can accommodate a wide variety of metal types, including aluminum, brass, and iron. This flexibility allows manufacturers to use a single casting method for different metal compositions, making it a popular choice in various industries.
3. Complex Shapes Sand casting is capable of producing complex shapes and intricate details. The pliability of sand allows for the creation of molds that can replicate fine features, which is particularly beneficial for producing parts with detailed geometries.
4. Large Size Capability Unlike other casting methods that may be limited by the size of the mold, sand casting can produce very large components. This makes it ideal for industries such as automotive and aerospace, where large and heavy parts are often required.
5. On-Site Production The sand casting process can be performed on-site, reducing transportation costs and lead times associated with shipping raw materials to a foundry or casting facility. This locality advantage can be crucial for urgent projects.
advantages and disadvantages of sand casting
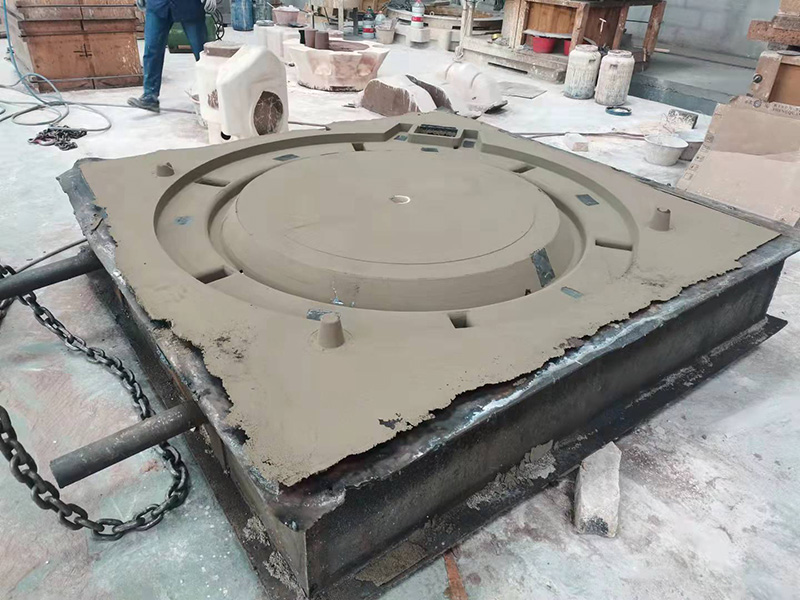
Disadvantages of Sand Casting
1. Surface Finish One of the main drawbacks of sand casting is the rough surface finish of the final product. The texture of the sand can leave a coarse finish, which may require additional machining or surface treatment, adding to the overall production costs.
2. Dimensional Tolerances Sand casting typically offers poorer dimensional accuracy compared to other casting processes, such as investment casting or die casting. The shrinkage of metal during solidification and the potential for sand shifting can result in dimensional deviations that need to be corrected.
3. Labor Intensive While the basic equipment is simple, sand casting is often labor-intensive. The process involves several manual steps, including mold preparation, which can lead to higher labor costs, especially if skilled labor is required.
4. Environmental Concerns The production of sand molds can pose environmental concerns, particularly with the use of certain binders and additives. In addition, spent sand must be disposed of or recycled properly to minimize environmental impact.
5. Limited Production Rate Although sand casting is flexible, it may not be the most efficient choice for high-volume production. The time required to create molds and castings can slow down the production rate, making it less suitable for mass production compared to die casting processes.
Conclusion
In summary, sand casting is a versatile and cost-effective method for producing metal components, especially suited for complex shapes and larger parts. However, challenges such as surface finish, dimensional accuracy, and labor intensity must be carefully weighed against its benefits. When making casting decisions, manufacturers should consider the specific requirements of their project and evaluate whether the advantages of sand casting align with their production needs.
Post time:9-р сар . 22, 2024 04:30
Next:molding sand for metal casting