3D Printer Sand Casting Innovating Traditional Foundry Techniques
In recent years, the world of manufacturing has undergone a significant transformation thanks to advancements in technology. One of the most fascinating innovations is the integration of 3D printing with traditional sand casting methods. This combination brings forth a revolutionary way to produce complex metal parts with enhanced precision, reduced lead times, and decreased costs.
3D Printer Sand Casting Innovating Traditional Foundry Techniques
By utilizing a 3D printer, manufacturers can produce highly intricate and detailed patterns that would be very difficult, if not impossible, to achieve through traditional methods. This capability enables designers to explore more innovative designs and modify existing ones without incurring significant costs for new tooling or complicated adjustments. Complex geometries can be manufactured with ease, leading to improved performance in the final product.
3d printer sand casting
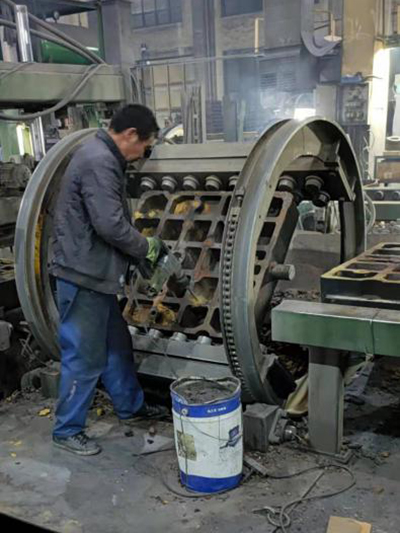
Moreover, using 3D-printed sand molds offers several environmental benefits. Traditional foundry processes can be resource-intensive, often resulting in a significant amount of waste. With 3D printing, materials can be utilized more efficiently. The capability to print molds layer by layer minimizes material waste and optimizes the use of resources. Additionally, the process can be more energy-efficient, as it reduces the need for extensive post-processing work and reduces the overall energy consumption involved in traditional casting methods.
The potential of 3D printer sand casting extends across various industries, from automotive to aerospace, and even art and sculpture. Manufacturers in these sectors are increasingly adopting this technology to enhance their production capabilities. For instance, in the automotive industry, the ability to quickly produce complex engine components allows for rapid prototyping and validation, speeding up the development cycle of new vehicles. In aerospace, the precision of 3D-printed sand casting contributes to the fabrication of lightweight, intricate components that meet stringent safety and performance standards.
Despite the many advantages, some challenges still need to be addressed. The reliability and quality of the printed molds and cores must consistently meet industry standards. Furthermore, the transition from traditional methods to 3D printing requires skilled personnel who can operate and maintain sophisticated machinery. However, as technology continues to evolve, training programs and resources are developing to equip the workforce for these modern manufacturing techniques.
In conclusion, the convergence of 3D printing and sand casting represents a significant leap forward in manufacturing technologies. This innovative process enhances design flexibility, reduces waste, and can lead to substantial cost savings. As industries continue to explore the possibilities of this technology, the future of manufacturing looks promising, with 3D printer sand casting paving the way for a new era of efficiency and creativity. The marriage of traditional craftsmanship and modern innovation promises to unlock new potentials that can transform how we approach product design and fabrication for years to come.
Post time:11-р сар . 05, 2024 20:27
Next:materials used for sand casting